Engine Room Ventilation – Editorial: Carcasses and Wishy-Washy Quote-Filled Articles
From the Masthead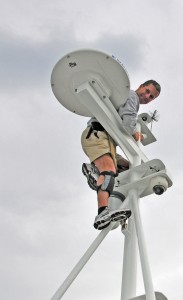
Carcasses and Wishy-Washy Quote-Filled Articles
I’ve been a technical journalist in the marine industry for almost 30-years, and I’ll readily admit that good copy editors are invaluable. When I first began writing, my drafts would be sent back to me with so much red ink, they looked as if they’d been handled by Jack the Ripper. Yes, in those days one actually submitted a typed draft, double-spaced, affording the editor room to make remarks and changes. In many cases the editor simply made the changes, which I didn’t see until the article was published. Usually that was good, sometimes it wasn’t, as the intent, or a technical detail had been altered, sometimes with dire consequences.
After a visit to Southampton, in the UK, I wrote an article about HMS Victory, Admiral Lord Nelson’s flagship at the Battle of Trafalgar; it was on the deck of that ship that he was mortally wounded, it is a hallowed place, and event, in British maritime history, and the culture as a whole; there are countless memorials, along with Lord Nelson pubs and inns, across the country. For reasons I was never able to ascertain, the copy editor, who was British himself, changed “Admiral Nelson’s body…” to “Admiral Nelson’s carcass…”, with the latter term for a deceased individual being far less dignified, especially for someone of Nelson’s stature; it was a word I would never use under the circumstances. I only discovered what had been done after it went to print, and I began receiving mail from sailors in the UK and various Commonwealth nations, deriding me for being so grossly disrespectful to a national legend, and I didn’t blame them. The magazine refused to print a correction. That left its mark on me, and as my career progressed, I began to insist on editorial control, which meant, other than minor grammatical, spelling or punctuation, no changes could be made to my work without my approval.
Not long ago I read two articles, each published in a different national boating magazine. The first was about lightning, the second about fuel additives. While the subject matter could not have been more different, they shared a common theme, one I encounter on an increasingly common basis, each was filled with quotes, some attributed, some unattributed. Quoting experts or otherwise knowledgeable individuals in an article can be useful under some circumstances (I avoid it, more on why in a moment), especially if they are attributed to someone whose credentials speak for themselves, an engineer, a very experiences mariner, a naval architect, boat builder, an ABYC certified technician etc., for example ‘“Additives containing alcohol should never be used in diesel engines unless specifically recommended by the engine manufacturer” says John Smith, 25 year industry veteran and ACME Engines engineer’.
Unattributed quotes, on the other hand, are tantamount to ‘unnamed sources’. There was a time when no self-respecting editor would even consider printing a quote from an unnamed source, today things are different. One of these articles included unattributed sources, which sound something like this, ‘an experienced charter skipper once told me, “Lightning never strikes the same place twice”’ (these aren’t actual quotes from the articles). The problem with unnamed sources is, they are unnamed, which means there’s no way to assess their validity, it’s essentially hearsay.
If an author chooses to use material directly from individuals, he or she should quote them, and include first and last name, title, and a brief c.v. Unnamed sources are best left to tabloids.
Why do I rarely quote others in the articles I write? I believe, as an author, my job is to know enough about a subject, either with first-hand knowledge and experience, or learn enough about it, in order to form an opinion, which I temper through the lens of my own experience, and then share with readers. The problem with many of the quote-filled articles I read is the quotes are often contradictory, and the reader is left wondering which of the quoted individuals’ advice to follow. This represents lazy journalism, once again the author should know enough, or learn enough about the subject to take a definitive stand, something like this, “Based on my own experience, and after speaking with three acknowledged lightning experts, it’s clear that contrary to popular belief, lightning rods don’t attract lightning, they simply act as a safe conduit should a strike occur”.
This month’s Marine Systems Excellence eMagazine column covers the subject of engine room ventilation, I hope you find it both useful and interesting.
Engine Room Ventilation for Diesels
While engine room temperatures can vary considerably depending on where they are taken; cooler is always better.
I looked at the thermometer attached to the engine’s air inlet filter and raised an eyebrow, it read 117°F, and it hadn’t stopped climbing. Before looking at it, however, I knew this engine room was hot, too hot, in addition to my drenched coveralls, many surfaces were simply too hot to touch, including the hand rail around the engine.
On its own that temperature reading, while seemingly high, isn’t of much value without knowing the ambient temperature, the temperature of the air outside the boat, or the air that is being drawn into the engine room for cooling. The difference between these two numbers, often referred to as ‘delta t’, tells an important story about engine room ventilation design and efficiency.
This exposed section of dry exhaust, it’s the flange that interfaces the turbo-charger and riser, is far too hot. Not only is it radiating heat into the engine room, which must be removed by the ventilation system, it represents both a burn and fire hazard. Standards established by the American Boat & Yacht Council dictate that no portion of an exhaust system that can be touched should exceed 200°F.
The overall importance of proper engine room ventilation is driven by efficiency and longevity. In short, engines that ingest hot air burn fuel less efficiently than those that ingest comparatively cool air, and the warmer an engine room is, the harder it is on the gear and systems housed there; heat equates to accelerated aging, higher failure rates and greater operating expense. Perhaps of equal importance, the failure of a builder or boat yard to meet engine manufacturer temperature guidelines can result in denial of warranty coverage for the engine or generator if a failure can be proven to be heat-related.
Ventilation Basics
Engine room ventilation requirements fall into two categories, those required for cooling the space, and those needed for combustion. The air used to cool the compartment improves the longevity and efficiency of the aforementioned gear located in this space, including engines, generators, and compressors, electrical and electronic components, along with making it a more comfortable place to work, while, as mentioned above, improving combustion efficiency. Where generators are concerned, while the engine portion is typically liquid cooled, the electrical generation end relies on air from the engine room for its cooling (a small number of generators rely on liquid cooled stators). When engine room temperature is excessive, generator manufacturers will, for this reason, often lower the unit’s rated output. Premature failure of generator voltage regulators can frequently be traced to overly hot engine rooms.
Potted generator voltage regulators, like the one shown here, are the proverbial engine room high temperature canary in the coal mine. If the potting is cracked, as this one is, it’s a good indication that the engine room is, or has been running, too hot.
Additionally, hot engine rooms take a toll on ‘soft goods’ such as generator couplings, belts, motor mounts, torsional vibration dampers, transmission damper plates, hoses, insulation, electronic shift and throttle controls, engine ECUs, and other electrical and electronic components, as well as batteries.
Engines aren’t the only victims of high engine room temperature, heat is the nemesis of electronic components as well.
Whenever possible, it’s always preferable to located batteries, particularly the house bank and especially lithium-ion batteries), outside engine compartments. Guidelines for calculating the cooling needs of engine rooms abound, however, as a general rule of thumb, (these apply to wet exhaust engines) to determine the necessary air flow rate, in cubic feet per minute, use this formula (2.75 x hp) – 90. Having said that, it’s wise to defer to requirements established by engine manufacturers, or whichever is greater.
Ideally, and while it varies from engine manufacturer to engine manufacture, the delta t, which should be measured at the engine or generator air inlet or filter, and at the louver where air is drawn into the engine room from the deck (in the shade), should not exceed 30°F (While Cummins and John Deere specify 30°F, Caterpillar’s requirements, as well as those of ISO 8861, are more stringent, they call for a maximum delta t of 22.5°F), with a maximum overall air inlet temperature of 122°F (again it differs from manufacturer to manufacturer, Cummins specifies an absolute maximum of 150°F). Temperature can be measured in various locations around an engine room, and can vary widely as a result, doing so at the engines’ air inlet, however, ensures that engine manufacturer guidelines are being met (or not), and it ensures standardization for record keeping purposes, as well as comparisons with other engine rooms.
While engines are invariably liquid-cooled, the electrical ends of the vast majority of generators are air cooled; they can expel a significant amount of hot air into an engine compartment.
Combustion air, the air that is required to properly burn fuel consumed by the engine, relies on another series of calculations. Most engine manufacturers supply engines with specifications that detail combustion air requirements, which might call for a given cross section for passive air intake vents, or a cubic foot per minute requirement for forced ventilation. Caterpillar’s standard guidelines for forced ventilation call for 2.5 cubic feet per minute, per horsepower, while one generic rule of thumb for passive combustion air inlet surface area specifies 0.55 square inches per horsepower. The Cummins guideline for passive vent surface area size uses the following formula, rated engine air intake, specific to each model, in cubic feet per minute, multiplied by 0.272, equals required area in square inches. This, undersized inlet cross section area, is a common violation for new builders, particularly where designs evolve to accommodate larger engines with no changes made to intake size. It’s important to note that the cross section must be measured at its narrowest restriction (and louver area must be subtracted); it’s not unusual to find large intakes that supply air via significantly constricted duct work, through equally constricting louvers.
Vents like these can be used for intake and discharge air, and the less restrictive they are the better; although it will not shed water, the round rather than flat louver in this case offers less resistance to air flow; a self-draining dorade is part of this design.
Exhaust systems can also play a significant role in engine room temperature, inadequately insulated exhaust systems can act as heat radiators, appreciably raising the temperature of an engine room. Conversely, inadequate engine room air turn over can lead to excessively high exhaust system surface temperature, which in turn can lead to finger pointing between boat builders and exhaust system manufacturers.
Design and Installation
Depending on the engine room size and space available for ducts, forced ventilation may be required to achieve engine manufacturer requirements. Forced ventilation should include both inlet/supply, and exhaust air. In the ideal installation, inlet air will be ducted into the engine room low, near the sole, and away from heat sources, while exhaust air will be drawn from the top of the space, where possible directly over heat producers such as engines. Duct designs should, however, avoid blowing inlet air directly onto engines in that this can cause cool air to be rapidly heated and dispersed around the compartment. The all too common high inlet and high exhaust ventilation arrangement is among the least efficient.
Exhaust air flow should be 110%-120% of inlet air flow. This disparity will take into account thermal expansion, as well as inducing a slight vacuum in the compartment, which in turn will prevent heat and odors from being driven into accommodation spaces, which is both unpleasant and inefficient in that it places greater load on HVAC system. Engine room vacuum should not exceed 0.5” H²O. Of course, inlet and exhaust ducting should be located far enough apart to prevent short cycling of air flowing between them.
Although it appears to be an after thought, this axial fan is likely having some effect on airflow. Most axial fans are rated for continuous use.
Not all forced ventilation blowers or fans are created equal. Most in-line blowers are designed for intermittent operation, to ventilate bilges after fueling a gasoline-powered vessel for instance, rather than continuously ventilation an engine room.
In-line blowers like the one shown here are suited for periodic bilge ventilation, however, few are rated for continuous use.
The familiar ‘squirrel cage’ blower design, along with most axial fans, are on the other hand, designed for continuous duty. Make certain you (or your builder) select the right blower for the application; I encounter this error frequently.
An industrial-size ‘squirrel cage’ blower. Units like these are designed to operate continuously, while at rest or underway.
A common squirrel cage blower, these are relatively inexpensive and they can often run for thousands of hours.
The ambient air temperature of the 117°F installation mentioned at the beginning of this column was 77°F, yielding a delta t of 40°F, earning it a failing grade for its engine room ventilation design. In order to achieve the desired temperature goals, ventilation systems should be designed following formulas and guidance provided by engine manufacturers, many of whom publish stand-alone engine room ventilation guidelines or manuals. In my experience these nearly always contain a wealth of useful guidance, for those designing ventilation systems, and installing engines. Too often, however, this guidance is ignored.
Because their profile is low, axial fans can be installed in locations where others may not fit, this one is installed on an overhead.
New vessels, and those that have been repowered, should be subject to rigorous sea trials, which include running engines for an extended period, a minimum of 45 minutes, at 75% load, and briefly, a minimum of five minutes, at 100% load. It is only under these conditions that an engine compartment’s ventilation efficiency can be truly evaluated, and even then, it is not a complete evaluation. ‘Heat-soaking’, the process whereby materials in the engine room rise in temperature until reaching equilibrium, can take as long as eight hours of engine run time. If the ventilation system fails the 75% load, 45 minute run test, it is almost certain to get worse during the heat-soak period.
Far too many engine room ventilation designs take a seat of the pants approach, rather than following engine manufacturer guidelines, or industry best practices. The former frequently leads to overly hot engine rooms, which in the long run compromise both engine efficiency, and longevity of gear located in that space.