Feature: Raw Water Plumbing Etiquette – Editorial: The Marine Equipment Trade Show and Electrification
From the Masthead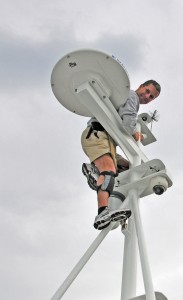
The Marine Equipment Trade Show and Electrification
I’m writing this month’s column while in flight, as I am homeward-bound from the Marine Equipment Trade Show, an event held annually in Amsterdam, the Netherlands. It is the largest, and undeniably the most important, event for boat builders, repairers, and equipment manufacturers. Its acres of floor space, spread out over 12 separate halls, is occupied by over 1,600 vendors. I describe it as the most valuable “boat” show I attend, one which includes no boats; it is exclusively equipment, and it is attended almost exclusively by industry professionals. Here’s a well-kept secret, if you are having a boat built, or refit, you too can attend this show; I highly recommend attendance for my clients.
In last month’s column I tackled the subject of high-tech overload and the damage it is doing to the credibility and viability of the marine industry. As I walked the floor of the METS show, where lithium-ion battery and electric propulsion options abound, I was overcome with the same feeling, is this what’s best for the boat owner? As hard as I try to understand this equation, I remain skeptical. Assuming the goal is environmental friendliness, and/or reduction of carbon dioxide emissions, unless the power generated for these propulsion systems is “green”, i.e., hydro, solar, and wind (you might include nuclear, depending on your politics), and even these sources (and batteries) aren’t truly green if you follow them back to their source materials, then what’s the advantage to electrification?
Unless fusion becomes reality, there is no clean energy revolution on the horizon, one that will make electric propulsion for marine (or automotive) applications, truly “green” or low/no carbon; almost nothing has zero carbon emissions. Unlike electric vehicles’ regenerative braking, there is very little opportunity for recapturing energy in electric marine propulsion systems (back driving the propeller on a sailing vessel is one option, with the consequent added drag). While some of this might be debatable, there are pure electric vessels that rely on a solar array for recharging batteries, for the most part, where cruising vessels are concerned, the limited range is a non-starter. Then there’s the 600 pound gorilla in the room, the added complexity, and lack of uniformity of design, encompassed by electric or hybrid systems, and the effect it has on reliability, serviceability, user friendliness and cost.
I recently inspected a vessel equipped with a diesel electric hybrid system, where the hybrid components completely impeded access to the transmission, making it impossible to check the oil level, or change the oil, without removal of much of the hybrid components.
Is electric propulsion progress, is this a better, more reliable, safer, and more cost-effective propulsion system for boat owners, and how much of electrification is driven by subsidies? I welcome readers’ thoughts.
The Fate of Professional BoatBuilder Magazine
Finally, as many of you have likely heard, Professional BoatBuilder magazine, often referred to as ‘ProBoat’, ceased publication with the November 2024 issue. ProBoat’s premier edition was released in October/November 1989, it’s been in existence almost as long as I’ve worked in this industry; I have been a reader from the start, and a contributor for over 20 years, and have served as the magazine’s Technical Editor since 2008. It ranks as my second longest editorial gig after Cruising World (I’ve written for them since 1994).
While I’m biased, the value of this publication to the marine industry cannot be over stated. Every issue included something of interest to virtually every industry professional, from naval architecture, design and engineering, to hands-on boat building and systems, and thanks to the skills of its editor Aaron Porter (a classically trained newspaper man), the quality and integrity of the editorial content was virtually without equal.
Now for the good news, it was announced at METS that the International Boatbuilders’ Exhibition and Conference (IBEX), has acquired ProBoat, along with Aaron Porter, and while I have already been asked to submit content for IBEX’s ProBoat, the exact picture of what the new publication will look like is still a work in progress. It’s unlikely that it will continue as a monthly print periodical (there’s talk of one annual print edition to coincide with IBEX and METS); instead, it will carry on electronically, via its own website, and as a result content can be more regular and timelier, with both editorial and video-based material. I’m optimistic, and look forward to ProBoat’s next chapter.
This month’s Marine Systems Excellence eMagazine feature covers the subject of raw water plumbing, I hope you find it both useful and interesting.
Raw Water Plumbing Etiquette
While this raw water discharge manifold is made from bronze, the leverage it imparts on the through hull fitting, as well as the thread type incompatibility, presents a serious fracture risk.
I looked at the plumbing arrangement, scratched my head and marveled at how it had managed to survive for this long. A ball valve attached to a through hull fitting, each with different, incompatible, threads, to which a pipe nipple and plastic strainer were attached. I was certain it wouldn’t withstand an application of five hundred pounds for thirty seconds, the long-established ABYC guideline detailing recommendations for seacock installations. On the contrary, I suspected it might fail if I simply leaned against it.
How Strong? How Reliable? How Robust?
Where this and many other raw water plumbing installations fail is in their robustness, their ability to endure stress and strain. While ABYC guidelines regarding seacock installations are amply clear; the aforementioned five-hundred-pound rule, which I have discussed on several occasions in previous Marne Systems Excellence columns, they are mute on the subject of raw water plumbing beyond the seacock and inside the vessel. I believe this represents a shortcoming in the Standards, in that a failure of any of these components could flood or sink a vessel just as handily as a failed seacock. The saving grace being, presumably, that in the event of such a failure the seacock could be closed, provided the vessel is occupied and provided the seacock is not submerged by the time the leak is discovered.
Non-metallic, purpose made, ABYC compliant seacocks like the one shown here are well-suited to raw water applications. The material from which these are made, reinforced Nylon, is durable, however, unlike PVC it is not brittle.
In June 2011 a Nordhavn 75 Expedition Yachtfisher sank at its slip in San Jose de Cabo, Mexico. The culprit was the failure of an after-market installation of a device known as a tuna tube, which is used to keep live bait. The plumbing for this component utilizes two inch inside diameter raw water plumbing, connected to a seacock, which was open. The failed component utilized a PVC pipe fitting that was secured in place with a nut similar to those seen on domestic sink drains. Predictably, much discussion circulated around internet forums regarding the failure, watertight bulkheads, bilge pumps and high water alarms. Interestingly, only a few of these discussions centered on the real cause of the sinking, the plumbing.
The PVC 90 degree fitting, and the clear PVC hose used in with this watermaker raw water pump, lack the necessary robustness and durability needed for seawater plumbing. A preferable alternative is bronze or glass reinforced Nylon, and a SEA J2006 hose.
Raw Water Plumbing Components
While there were, in my opinion, virtually no new lessons to be learned from this unfortunate event, there are lessons worth reiterating. Foremost is the need to ensure that all raw water plumbing installations are rugged, durable and robust. This includes any component that, if it should fail, will allow water to flood or be pumped into the vessel; including engines, generators, wash-down, watermakers and air conditioning systems, among others. In the latter two cases, a failure of plumbing on the outlet or pressurized side of the pump, even if above the vessel’s resting waterline, can lead to rapid and catastrophic flooding because rather than simply flooding, the water is being pumped into he vessel. Many vessels are left unattended with air conditioning systems operating, making them ripe for a failure of this sort.
I’m often surprised by the lack of robustness when inspecting installations for these systems. The primary failings are excessive leverage, and poor support, imparted by long, rigid fittings that often rely on gossamer plumbing components and materials. The combination is a veritable recipe for failure.
Leverage where raw water plumbing is concerned is an invitation to failure. Add PVC to that equation and the odds of failure go up considerably.
While its use is often fiercely defended by its devotees, with rare exceptions PVC plumbing has no place in raw water installations. It is used within or as an integral part of equipment by some chilled water air conditioning, and water maker, manufacturers. In those cases, if a failure occurs in their component, you or your insurer may have some legal recourse, which is still a less than an appealing prospect.
Clear PVC hose, even when wire reinforced, must not be used for raw water plumbing.
I have seen, on many occasions, PVC components used by installers of this and other equipment, to facilitate the various plumbing requirements in the field, as it were. In this case, should a PVC plumbing failure occur, it’s difficult to see how they would not bear some responsibility for damages. At the very least, it is assumed, at least for reputable manufacturers, that the PVC components are well-engineered, and well supported.
Its versatility, corrosion resistance, and ready availability, make PVC tempting for use with raw water systems. It is, however, ill-suited for this application.
In my experience PVC is frequently used out of convenience, rather than being the most suitable material for the application. A wide variety of shapes and sizes are readily available from any hardware or home improvement store. Many point to its enviable and seemingly indestructible record ashore.
Just say no to PVC…
However, while it works well in domestic applications, and it is immune to corrosion, a shipboard environment, with extremes of temperature, g-force, foot and gear traffic patterns and vibration, is significantly more stressful. I have encountered many PVC failures, more than enough to convince me that the material is, with rare exceptions, ill-suited for raw water applications.
Bronze is durable, abrasion and corrosion resistant, it has been reliably used in raw water applications for over a century. The challenge, however, is in knowing the exact alloy, as there are countless copper alloys, and many look alike. Some bronze plumbing fittings, like this one, are labeled. most are not.
Alternatives include bronze alloys such as ASTM B62, sometimes referred to as 85-5-5-5, because it consists of 85% copper and 5% each of lead, silicon and zinc. Although available in only a limited range of options, fiberglass is an excellent alternative for conveyance of raw water, as are plastics specifically designed by their manufacturers for marine, raw water applications. These include Forespar’s proprietary reinforced Marelon as well as TruDesign’s line of raw water plumbing fittings, among others, both of which are made from glass reinforced Nylon.
Unlike PVC, glass reinforced Nylon is ideally suited for raw water applications.
Regardless of which material is used, large cantilever sections should be avoided; other than a pipe to hose adapter, nothing should be plumbed directly and rigidly to a seacock, hose should always separate seacocks from other components, manifolds or fittings.
Bronze is a proven, reliable material for use with raw water. However, there is no way to distinguish between bronze and brass in the field, and the latter is strictly forbidden with seawater applications. This brass pipe to hose adapter failed in less than a year of use.
Hose
Hose used for raw water applications must be equally as durable, and without exception it should be specifically designed and rated by its manufacturer for the application. Most clear, flexible PVC hoses lack a marine raw water rating. The primary weakness in most clear, PVC hose is its susceptibility to chafe, and especially when warm, crushing and kinking.
The SAE J2006 EPDM hose used in conjunction with this HVAC system is rugged and robust; in that respect it’s well-suited for the application. However, it is also very stiff, and it is plumbed to a PVC manifold. In the limited, approved locations, where PVC is used for raw water applications, every effort should be made to avoid excess strain, and to provide adequate support. In this case, a preferable alternative is SEA J2006 corrugated silicone hose, it is far more flexible than the EPDM variety.
Ideally, hose used for raw water applications should be clearly embossed or printed with the manufacturer’s name and the model and, ideally, its intended use, and date of manufacture. Marine raw water and wet exhaust hose (it’s typically black, however, silicone exhaust hose can also be blue or orange) that carries a SAE J2006R rating is suited for this application, it’s rugged, durable and crush resistant, as is opaque PVC sanitation hose (it’s usually white). These hoses are also more expensive and more difficult to route than lighter weight clear PVC hose.
In addition to lacking the necessary durability for use with raw water, clear PVC hose like the one shown here is both kink and crush prone, and it is especially ill-suited for intake or vacuum applications.
For suction applications, particularly engine and generator intakes, the wire reinforced J2006R variety should be used. When in doubt, contact the manufacturer or distributor of the hose and ask, “Is this hose rated for marine, seawater use, and is it warranted against failure in such applications?”
As durable as it is in above the waterline applications, stainless steel, even highly corrosion resistant alloys like AISI 316, will corrode when exposed to stagnant raw water, and the only thing worse than stainless steel raw water plumbing is welded stainless steel raw water plumbing. If stainless steel use is unavoidable, and it is to be welded, it must be of the low carbon variety, signified by an L suffix, such as 316L.
While there are no specific ABYC guidelines for raw water plumbing within the vessel, my personal guideline goes something like this, ‘If it’s too weak, too fragile or too flimsy to stand on, then it’s not robust enough’. Essentially, every raw water plumbing component, hose, pipe, strainer, valve or manifold, should be strong enough to stand on, and of course all seacocks should be able to withstand the aforementioned five hundred pound, thirty second torture test. If any of your raw water components fail to meet these guidelines, then they need to be re-engineered or replaced with ones that do.
Please find a letter from Spears Manufacturing Company here, on the topic of using a Spears® #1436-010 in a below waterline application.