“Zinc” Anode Selection and the Role Played by Galvanic Isolators – Editorial: Fire Extinguisher Selection
From the Masthead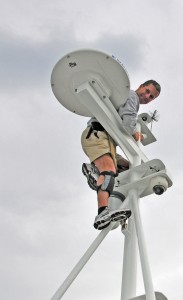
Last month I received an e-newsletter form BoatU.S.® entitled “Boat Fire Extinguishers: Four Myths From the BoatUS Foundation”. Some were very useful, like not using a mallet to beat on the bottom of the extinguisher, to prevent caking of the powdered extinguishing agent, or recommending having more than the minimum number of extinguishers aboard. Others, however, left me scratching my head, or thinking they’d missed a good opportunity to expand on this subject, including and especially the one that identified, as a myth, the need for installing every fire extinguisher using a bracket. While it may not be part of the Code of Federal Regulations for recreational vessels, I can think of few circumstances where it is desirable to not use a bracket. Unsecured fire extinguishers can become deadly missiles in a seaway, as well as disappearing into the nether regions of deep lockers, making them inaccessible when needed most. Don’t get me wrong, anything that raises awareness about fire extinguisher etiquette is welcomed, and I applaud the efforts of BoatU.S.®.
My own list of common fire extinguisher myths, developed over my nearly three decades of work in the marine trades, is as follows.
Myth #1: It doesn’t really matter what kind of fire extinguisher I have, or its size, it’s probably OK.
In fact nothing could be further from the truth. Different classes of fires, A, B, C, D and K, require different fighting techniques. For more on extinguisher options and selection see http://stevedmarineconsulting.com/portable-fire-extinguishers-not-all-are-created-equal/ This article will also help you decipher the codes used to classify portable fire extinguishers, and shown in the tables below.
Myth #2: I don’t need a fixed engine room fire extinguisher.
Fixed engine room fire extinguishers are among the most valuable, and least expensive firefighting insurance money can buy. While it may not be required by law, compliance with ABYC guidelines calls for installation of these systems, Standards section A-4.5 states, “Inboard and sterndrive boats with engine compartments shall have either: a fixed fire extinguishing system installed in the machinery space, or a single suitably sized clean agent portable fire extinguisher provided and installed in proximity to a port to permit discharge directly into the engine compartment without opening the primary access.”
Myth #3: The Coast Guard says my fire extinguishers must be inspected annually.
While it’s unlikely that you’ll get a ticket for an uninspected fire extinguisher aboard a recreational vessel, it is a good idea to have your fixed system inspected periodically. This inspection should include weighing the cylinder as well as testing the automatic engine/ventilation shut down system, which is mandatory for ABYC compliance in diesel-powered vessels. The manual discharge cable should also be tested to ensure it’s not seized (I’ve encountered this scenario). I’ve found that many fire extinguisher maintenance companies know very little about fixed systems aboard yachts, so before you hire one ask them what their inspection includes. Inspections for portable dry-chemical extinguishers are often primarily visual, check for proper pressure, and corrosion, and make sure the bracket is in good working order. Clean agent portable extinguishers should be weighed.
Finally, myth #4: I only need a fire extinguisher in the galley.
While it’s a good idea to have a fire extinguisher in the galley, you must have them elsewhere as well. Once again, ABYC Standard A-4.6.3 covers this subject well, “Number and Location – Portable fire extinguishers shall be provided and conspicuously installed in accordance with the minimum required in TABLE II or TABLE III [see below]. All extinguishers shall be located adjacent to exit paths. It shall not be necessary to travel more than one-half the length of the boat or 33 ft. (10 m.), whichever is less, to reach an extinguisher.” While that’s good, and a higher standard than the USCG requirement, my personal rule is as follows, You should never be more than three giant steps from a fire extinguisher.
ABYC A-4 Table II
TABLE II NOTES:
- If a discharge port is installed (ABYC A-4.5.2.2 ), a USCG type B-I portable fire extinguisher may not be adequate (see Table IV ).
- Extinguishers intended for engine compartment protection in accordance with A-4.5.2.2 or A-4.6.4 are not required to have a Class A rating.
- Boats under 26 ft. in length without enclosed accommodation spaces or enclosed galleys may be equipped with a bucket with attached lanyard and a Class “BC” rated extinguisher in lieu of Class “ABC” rated portable fire extinguishers.
- On boats having galley stoves, one of the required extinguishers shall be readily accessible thereto.
ABYC A-4 Table III
TABLE III NOTES:
- If the total horsepower exceeds 1000 B.H.P. an additional B-II portable fire extinguisher is required for each additional 1000 B.H.P. or fraction thereof.
- The required B-I and B-II portable fire extinguisher may be distributed among the recommended locations as desired.
- If a discharge port is installed (See A-4.5.2.2 ), a USCG size B-I or B-II portable fire extinguisher may not be adequate (see TABLE IV ).
This month’s Marine Systems Excellence eMagazine column covers the subject of galvanic isolators and “zinc” anode selection. I hope you find it both useful and interesting.
“Zinc” Anode Selection and the Role Played by Galvanic Isolators
Stray current corrosion, which is nearly always the result of DC current leaking into and around the water in which a vessel floats, via faulty wiring, is both rapid and highly destructive. It can lead to damage like the that shown here over the course of days or even hours.
In a previous eMagazine column I discussed bonding systems and the role they play in minimizing the likelihood of stray current and galvanic corrosion. This month I’ll look at the role galvanic isolators play in this process, as well as offering tips on anode selection and installation.
As a refresher, stray current corrosion is nearly always the result of DC current that is “leaking” into bilge water or underwater metals. It’s especially destructive in that it typically causes severe damage very rapidly, often in a matter of days or weeks. Galvanic or dissimilar metal corrosion, on the other hand, while also DC in nature, is much slower and more insidious, taking months or years to do its dirty work. In either case, a sound bonding system and cathodic protection (installing and maintaining zinc or other alloy anodes, more on this in a moment) are key elements in the defense against both types of corrosion.
“Anodes” are any sacrificial metal installed on your hull, running gear or inside your engine that are used to prevent dissimilar metal corrosion. These may be made of zinc, aluminum or magnesium and for that reason they are properly referred to as anodes rather than zincs, although the vast majority of anodes are in fact zinc. In short, all zincs are anodes, but not all anodes are zinc.
Galvanic isolators present an effective means of limiting DC current flow over shore power ground wires, thereby diminishing the likelihood of galvanic corrosion occurring as a result of interaction with nearby vessels or metallic dock structures.
For anodes mounted to the hull, carefully inspect the studs themselves as well as the wiring that is attached to them inside the vessel. The external portion should be clean and free of any scale or marine growth. If necessary, remove the anodes and clean the hardware using emery cloth or scuff pad (avoid using wire brushes as they can leave behind metal that can lower protection levels which can accelerate the corrosion process, or at the very least cause staining). Make certain fasteners used to hold anodes in place are secure and complete. That is, ensure that lock washers and, if necessary washers are used and ensure they are installed in the correct order. The lock washer should always rest directly under the nut.
For anodes installed over other hardware, such as rudders, propeller shafts and trim tabs, make certain the surface has been thoroughly cleaned before installing a new anode. If the anode is installed over a surface that is contaminated with scale, paint or other debris then the protection the anode provides will be compromised. It’s important to note as well that anodes that last an unusually long time are suspect. When an anode is consumed it’s doing its job, it’s providing protection to the metal(s) to which it’s connected.
Once installed, if you are able to use an ohm meter, you can check your installation and the soundness of the bonding system by connecting one lead to the anode and the other to a bonded underwater metal, a through hull fitting, strut or rudder for instance (you may need to make extra long leads to perform this test). This test can only be performed with the boat out of the water. The resistance between any bonded underwater metals and an anode should not exceed one ohm. If it does then the hull anode is ether not making good contact with its mounting studs, or the bonding system wiring is compromised by corrosion or a loose connection.
As mentioned above, anodes are available in different alloys, aluminum, magnesium and of course zinc. Traditionally, fiberglass vessel’s operating in seawater have used zinc because it provides more than adequate protection for common underwater metals such as stainless steel and bronze. Zinc anodes are less effective in freshwater or brackish water, in most cases they develop a scale-like coating, essentially rendering them inert (in this “asleep” state they do last a very long time). The relative energy capacity of zinc, remember this is all about electricity, is 368 amp-hours per pound and their voltage is -1050 millivolts (in corrosion speak, the more negative the better). Remember those numbers.
Unlike zinc, aluminum anodes are designed to operate effectively in salt, brackish and fresh water with little or no degradation in performance.
Aluminum anodes, on the other hand, have several advantages. They are well suited for use in seawater as well as brackish and freshwater. Thus, if you find yourself transiting these water types, then aluminum anodes make the most sense. Aluminum anodes also pack more of a punch and they last longer than zinc anodes of the same weight. Their relative energy capacity is 1108 amp-hours per pound, significantly more than zinc, with a voltage of -1100 millivolts. If you opt for aluminum anodes, be sure that the change is universal, for all anodes used within the same bonding system. Surprisingly, aluminum anodes are often no more costly than their zinc brethren, offering a free lunch of sorts.
When exposed to fresh water, zinc anodes develop a coating that effectively renders them inert. It can be scrubbed off using a non-metallic brush or pad, however, until this is done, or they are replaced, the vessel’s corrosion protection level remains diminished.
Magnesium, on the other hand is an alloy that is reserved strictly for use in fresh water. If that’s the only place you operate your boat, then consider using this as your anode material.
Whichever anode material you select, be certain it carries a military specification approval. Doing so will ensure, among other things, that it is free of an excessive amount of other trace metals that offer no corrosion protection and reduce anode effectiveness.
Periodically inspect your anodes; they should be eroding relatively evenly, particularly those that are the same size. The rate at which they are consumed is a function of how much metal they are protecting, the size of the anode, and boat usage (more underway time or water motion at the dock causes faster anode consumption). If your anodes appear to remain unchanged and last forever, something’s probably wrong. If, on the other hand, they are consumed very rapidly or the rate at which they are being consumed increases, then don’t ignore this symptom, it’s probably telling you something is wrong. Once the anodes are gone, the next least noble metals – often a propeller – will take its place by corroding away in much the same way the anode did.
Even if your bonding systems and anodes are in good working order, it’s possible that your vessel will still suffer from either rapid anode consumption or, worse, corrosion of underwater metals. The culprit in this, ‘you believe you are doing everything right but are still suffering from corrosion issues’, scenario is the shore power cable. Note, I said shore power cable and not shore power. One of the conductors in the shore power cable is a green wire called the safety ground. This extremely important wire ensures that a shore power fault aboard your vessel will be safely carried to ground causing a circuit breaker to trip; without it, or if it’s installed incorrectly or in poor condition, it could lead to a fire or electrocution. This wire is, by necessity, connected to your vessel’s bonding system and through it to the anodes.
Monitoring and replacing anodes in a timely fashion is a critical aspect of a corrosion prevention plan. Waiting until they completely disappear, like the one shown here, only its armature remains, on the other hand, makes galvanic corrosion a near certainty. The smaller an anode becomes, the less protection it offers.
Whenever you plug into shore power you are, often unknowingly, connecting your bonding system, and anodes, to all of the other vessels on your dock, and their underwater metals and anodes. Doing so often means that your anodes could be protecting the underwater metals of the vessel in the slip next to or across from you, especially if that vessel’s anodes are depleted. This is a simple case of galvanic corrosion and it has nothing to do with the shore power itself, it’s simply the connection that is made via the shore power cable and its green safety ground wire. Even if you turn the shore power off, the green ground wire remains connected whenever the shore power cable is plugged in to both your vessel and the dock pedestal, and as long as it’s connected potentially destructive galvanic current can flow through this medium.
There are two possible solutions to this problem. The first is very simple and it’s free, simply unplug your shore power cable whenever it’s not being used. If you are able to do that, if you are able to leave your vessel unplugged, the problem is solved. In most cases, however, that’s simply not practical, folks want to leave vessels plugged in to keep refrigeration and HVAC systems as well as battery chargers (to keep a bilge pump running in the event of a leak if nothing else) operational.
The other alternative involves the installation of a device known as a galvanic isolator. Galvanic isolators block DC current (at up to 1.4 volts DC across the isolator, anything above that is beyond galvanic corrosion potential), which, as mentioned earlier, is what causes corrosion, while allowing AC current, including the all too important shore power faults, to pass. Blocking DC current means that when you plug into shore power your vessel is now isolated from other vessels’ AC grounds and bonding systems, and you are no longer protecting your slip neighbor’s boat that hasn’t had its anodes changed in two years (i.e. you are not paying for his protection using your anodes).
For a twin 120 volt, 30 amp inlet scenario, you’d need either two 30 amp isolators, or one 60 amp unit, while for a single 120/240 volt 50 amp shore power cable you would need a single unit rated for a minimum of 50 amps.
Galvanic isolators are well worth the comparatively small expense. My recommendation is, even if you plug into shore power once a year, it’s worth having a galvanic isolator. As one might expect, not all galvanic isolators are created equal. Select yours based on the following criteria…
- A failsafe design that ensures that even in the event of a catastrophic internal fault or a lightning strike the isolator will still safely and reliably conduct AC fault current to ground (even though it may no longer isolate galvanic current).
- Full compliance with ABYC Standard A-28 Galvanic Isolators, most recently revised as of July 2008.