Hose Clamps Part II: Installation and Use
From the Editor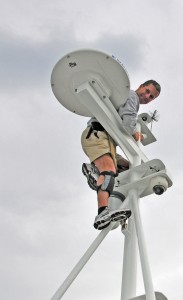
A colleague of mine, the editor of a respected marine industry magazine, one for which I write, recently made an editorial leap of faith. In his monthly column he said what many know, what many have thought, and what many have experienced first-hand, yet he committed to print what so few have the courage to write. For that he is to be commended, it was a bold move, one which will no doubt generate a great deal of discussion among readers and advertisers alike. The real value of this column is, however, in alerting readers to the existence of this scenario. An excerpt of that editorial follows, I hope you find it as thought provoking as I did.
“Know Your Sources: …Advertorial, native advertising, or sponsored content—call it what you may—is a trend that blurs the line between editorial content and paid advertisement, and it leaves readers with no way to differentiate between credible editorial information and carefully composed, subtly placed product advocacy. Readers of any publication deserve to know the sources of all the printed material in it. This is particularly true for a magazine like Professional BoatBuilder, which delivers often-complex technical material written by experienced industry professionals. If readers are to trust our printed words to influence how they make their living, it’s important that they can identify our writers and sources, know their credentials, and, in some cases, what their professional affiliations are. It should also be reassuring to know that we determine our editorial lineup without giving any special consideration to advertisers. In short, editorial is not for sale here.
But even with that crystal-clear policy in place, the recent shift in publishing standards too frequently leads new marketing reps from advertisers to ask when we will publish a story about their work or product, or to offer us such “articles,” composed by their hired writers, free of charge. More insidious, we’ve found seemingly legitimate writers pitching stories when, unbeknownst to us, they are being paid by the subject company’s marketing department upon whose behalf they submitted the idea. This is marketing masquerading as editorial content to deceive editors as well as readers. We’ve identified and rejected a few of these would-be Trojan-horse sources over the years, but I still feel paranoid when we vet new, unfamiliar writers…Indeed, much of the work of creating this magazine is vetting sources, asking for supporting documentation, and demanding some names of known and trusted builders or experts who might have used a new product or material [before we print an article about it].”
Aaron S. Porter
Editor
Professional BoatBuilder Magazine
This month’s Ezine column is the second of a two part series on hose clamps, I hope you find it both interesting and useful.
Hose Clamps Part II: Installation and Use
Text and photos by Steve D’Antonio
Copyright SDMC, Inc. 2015
Two hose clamps are not always better than one. If both clamps can’t bear properly on the barb beneath, then the second clamp is of little use. This pipe to hose adapter is deceiving, it looks as if the hose is simply not pushed completely home, however, this is in fact a stepped adapter, the portion over which the hose has bene installed is a smaller diameter
Last month I discussed various hose clamp designs, materials and selection. This month we’ll look at clamp installation, installation tools and pipe to hose adapters.
Installation; one clamp or two?
Questions regarding hose clamp installation abound. Among the most common is the seeming “requirement” for double clamps. The ABYC (American Boat and Yacht Council) recommendations (they are just that, recommendations, rather than binding law) call for double clamps in only two locations, fuel fill hoses and exhaust systems (my own guidelines add stuffing boxes to this list). Double clamps are required for some international boat building guidelines, including those of ISO (International Standards Organization, which cover vessels built in Europe), which mandate, in addition to other locations, double clamping of hoses used on seacocks. While double clamps are undeniably desirable, in any other location they are optional where ABYC compliance is sought. The most common double clamp faux pas involves the use of the second clamp in applications where it is not properly supported. For example, using a second clamp where its pressure cannot bear fully on the pipe to hose adapter (more on those in a moment) beneath it is extremely common. This phenomenon is often the result of an overzealous installer who believes or often insists two clamps are mandatory and without them failure is imminent. That’s simply nonsense and ironically, the actions of such a well-meaning individual may lead to damage to, or a premature failure of the hose over which the clamp is installed. In locations other than those mentioned above, where they are required for ABYC compliance, and especially if the clamp cannot properly and fully bear on the pipe to hose adapter, without overlapping of clamps, then only a single high quality, all stainless steel, sold band clamp should be used.
A magnet is used to identify a plated steel screw (with perforated band) hose clamp. This type of clamp should not be used in any marine application.
Clamps should be installed so that one quarter of an inch of hose is visible between the band and the hose end (and an estimated ¼ inch between the end of the pipe to hose adapter and the clamp), and approximately a quarter of an inch between any two clamp’s bands. In short, it’s critically important to confirm the length of the pipe to hose adapter under the hose before installing a clamp or clamps.
I’m often asked, if twin clamps are used do the screws need to be installed 180° apart. The fact is, in my experience I don’t believe it matters; clamps are designed to impart even pressure on a hose regardless of the position of the screw. If it makes you feel better installing them with this orientation, go for it.
How tight is tight?
Hose clamps should be tightened to their manufacturer rated specification. Yes, most hose clamp manufacturers do provide a torque specification for their clamps, typically in inch pounds. While I don’t expect most folks to use a torque wrench for clamp installations (mini palm-size torque wrenches, suitable for hose clamps, are available, however), doing so once or twice would give you a feel for just how much tension is required by clamp manufacturers to ensure a positive seal between the hose and pipe to hose adapter. Most full size solid band hose clamps call for 30-40 inch pounds of torque, which is easily achieved using a screw driver or proprietary hose clamp installation tool.
A mini-torque wrench being used to ensure proper hose clamp tension.
A ¼ inch drive ratchet is among the most effective and reliable tools for installation of hose clamps. Because of the leverage it is, however, prone to over tightening, particularly perforated thread clamps.
Common screw drivers work well for clamp installation, however, the blade tip is prone to slipping out of the screw recess. If installing or tightening more than a few clamps, a socket drive is preferred.
Flexible socket drive designed specifically for hose clamp installation embody the best of screw drivers and ¼ inch ratchet drives, with the ability to access hard to reach locations.
Over-tightening clamps leads to damage to (automotive) clamp’s threads and damage to the hose, and increases the likelihood of crevice corrosion (through micro-cracking of the clamp’s band, again more of an issue on perforated clamps). Clamps often require less tension than is believed, which is why the torque wrench test is beneficial. By the way, proprietary hose clamp drivers are among my favorite tools. Their flexible shank makes accessing hard to reach clamps easier and the ergonomic handle allows the installer to impart the right amount torque without straining.
A proprietary cast bronze pipe to hose adapter. The ridges or barbs make it virtually impossible for a properly clamped hose to slip off.
I’ve used the term pipe to hose adapter on several occasions. A pipe to hose adapter, often abbreviated in the industry as PTH, is a device that looks vaguely like a short length of pipe with one important difference, with a few specific exceptions, the area over which the hose is installed is neither smooth nor threaded. Instead, it’s made up of a series of barbs, sort of bumps with one ramped and one square edge. These barbs ensure that the hose is securely retained when clamped. Often, however, installers will use a pipe nipple instead of a PTH adapter.
Because of their smooth surface, uncut or cut-off pipe nipples, like the ones shown here, are inappropriate for making hose connections.
Pipe nipples have both smooth and threaded section; however, they do not include barbs. The smooth section provides insufficient grip for the hose and the helical nature of the thread creates a path for fluid leakage. These deficiencies conspire to make the pipe nipple an inappropriate and unreliable method of terminating any hose. Incidentally, fuel fill and exhaust pipe to hose adapters may be smooth, un-barbed surfaces, however, they may not be threaded at the hose interface area, i.e. pipe nipples may not be used.
Size it Right
Hose clamps are available in a wide assortment of diameter ranges and for that reason a pet peeve of mine is clamps that are too large for the application. While an oversized clamp may do the job, it invariably leaves an undesirable legacy in the form of a long, potentially sharp “tail” that is just lying in wait for an unsuspecting forearm or finger to scrape past. If this occurs in a bilge, under a galley or head sink, or worse in the bilge, where hands and arms are wont to go, the potential for an injury becoming infected is considerable (all cruisers and mechanics should have an up to date tetanus vaccination, they are typically good for ten years).
While over-sized hose clamps present a laceration hazard, ultra-sharp ‘field-trimmed’ clamps are far worse.
In addition to using the right size clamp for the job, you can go a step further by either slightly bending any remaining tail down into the tensioned portion of the band or by installing one of the proprietary silicone clamp finishers or “jackets”.
Hose finishers can be used to reduce the likelihood of injury when working around hose clamps, consider using these in high traffic areas, adjacent to valves, under galley and head sinks, and elsewhere.
The finisher safely envelopes the sharp end of the clamp and is especially useful in high traffic areas, the aforementioned galley and head sink, bilges etc. Beware of clamp finishers that are made of hard materials such as PVC, as they easily fall off clamps, often clogging bilge pumps. Those made of silicone are especially supple and sticky, enabling them to adhere tenaciously to the clamp.
A scythe-like clamp lying in wait for an unsuspecting crew member to reach beneath this head vanity. Avoid using over-sized clamps, and in areas where hands and forearms are likely to reach, ends should be covered with finishing caps.
The same caveat holds true for the exposed portion of the shank on T bolt clamps, while less sharp these still present an injury hazard and are a nuisance as they tend to catch clothing and gear. And, while on the subject of T bolt clamps, if an oversized T bolt clamp is used there is the risk of it “two blocking” or running out of adjustment before it imparts the proper amount of tension to the hose installation. It’s easy to see if this is the case, if both ends of the clamp are making contact with each other, with no room for adjustment, then the clamp is incorrectly sized and could allow the hose to separate from its adapter. This scenario is especially insidious because the installer feels tension building as the nut is being tightened, leading him or her to believe the clamp is tightening the hose when in fact it’s simply running out of adjustment.
An oversized T bolt clamp, it’s ends bottomed out, can be insidious in that the installer may believe, as tension increases, the clamps is properly compressing the hose, when in fact it’s simply running out of adjustment.
Does it really matter how the hose is attached?
Recently, while carrying out an engine room inspection aboard a vessel undergoing sea trials, I experienced firsthand just how flawed the pipe nipple as a PTH can be. While the vessel was operating at full power I made my way through the engine room and, using an infrared pyrometer, checked the temperature of various components. After I had completed my rounds I stepped out of the space and closed the hatch behind me. As I did so, even through my hearing protection, I heard a loud whoosh. My hand was still on the handle and I instinctively re-opened the hatch; when I did so a cloud of steam billowed through the opening. After telling the operator to shut down the engine I re-entered the space and determined that the source of the steam was a failed coolant hose. The vessel was equipped with a keel cooler that was plumbed to the engine via a set of 1 7/8 inside diameter hoses, which were terminated at the engine using a set of pipe nipples. In spite of the fact that the hose was double clamped it slipped off of the threaded nipple, spewing the entire contents of the cooling system, roughly ten gallons of 200°F coolant, around the engine room. Just moments before this had occurred I was standing in front of the engine, where these hoses were located, taking temperature readings of the expansion tank. Had the hose released while I was standing there it’s likely that I would have been severely burned.
This cooling system hose parted from its makeshift pipe to hose adapter a close pipe nipple, spewing near boiling coolant into the engine room, nearly scalding the author. Prior to the failure the installed hose gave few indications of the fault that lie beneath.
When it comes to hose clamps and their installation, take no chances. Use only the highest quality, most durable, properly torqued clamps and ensure that they are installed over proper pipe to hose adapters. If the pipe to hose adapter will support two clamps, by all means double up and if double clamps are required for ABYC compliance, then ensure twin clamps are used.