Brass vs. Bronze; Know your Underwater Alloys – Editorial: Boat Show Season is Upon us Once More
From the Editor 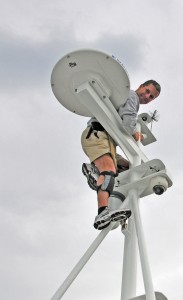
Boat show season is upon us once again. It began, for me, last month when I lectured at the International Boat Builders’ Exhibition (IBEX), an annual gathering of marine industry professionals. I routinely sing the praises of that event, pointing out to my peers in the industry the value of getting out and spending time among colleagues, networking and of course attending some of the many informative seminars. Dozens of presentations, workshops and “super-session” topics range from proper use of torque wrenches and in house apprentice programs, to 3D printing and battery bank design and installation. Many of the presenters are industry rock stars who know their subjects inside and out. The show also consists of a large exhibit hall with aisle after aisle of manufacturers showing their wares and services. Because the event caters only to the trade, exhibitor booths tend to be staffed with the gearheads and geeks that manufacturers only let out for shows like this, where they aren’t likely to encounter boat owners. I never fail to walk that show floor without coming back with a fistful of business cards. In my business, having the right contacts can make the difference between a quick right answer to a problem, and no answer at all, or worse, the wrong answer. I’m forever looking for ways to bring greater value to my clients and readers, and this is one of the ways I do it. Yet, sadly, many in the industry simply don’t see the value in the event, and I lament that sentiment to no end.
Steve discusses technical details about Charles transformers with long-time acquaintance engineer Larry Budd.
As a boat owner (I dislike the word “consumer”, when did we go from being “citizens” to “consumers”?), you can do your part by asking marine industry professionals with whom you deal, how and where they get their continuing education, what trade-related events, education or training to they attend, do they go to IBEX and if not why? As valuable as IBEX is, it’s the best thing going Stateside, there’s an event that tops it, the Marine Equipment Trade Show (METS), which is held in Amsterdam, the Netherlands each year. It’s many times the size of IBEX and among my favorite shows; I’ll attend and report on it in late November.
The day after IBEX I flew to the Newport Boat Show in Newport, Rhode Island. I haven’t attended this show in several years, it seemed to be waning in popularity and relevancy. I was, however, pleasantly surprised as it was busy, and filled with high quality exhibits and a wide range of manufacturers and boat builders. It didn’t hurt that the weather was simply gorgeous. I went to the show specifically to meet with clients, to review the details of the boat they are having built, a Palm Beach 50. While there they asked if I would help them look for a starter vessel for their son, daughter-in-law and grandchildren. With the budget they had I was skeptical, however, I was once again pleasantly surprised to find at least one worthy contender in the 22-foot, 200 hp four stroke outboard, under $50k range (the price was a boat show special), complete with the requisite enclosed toilet. Ensuring young families can get on the water is important, especially to those of us in the trade.
From a consumer, I mean boat owner, perspective, the Fort Lauderdale International Boat Show, which takes place in early November, is next. Traditionally this is one of the most productive shows for me, I wouldn’t miss it. I’ll host a breakfast for my Captains Club members as well as meeting with clients, boat builders and equipment manufacturers. I’ll share some of what I see from the show via this editorial column and my Facebook page.
Know your Underwater Alloys
Photos and text by Steve D’Antonio
Copyright © SDMC, Inc. 2015
Brass simply isn’t suitable for seawater applications. Insidiously, however, when new there’s no immediate means of determining the difference between brass and bronze.
It’s one of those metals that has an indelible aura about it, while its presence is intricately and indelibly woven throughout our lives, both ashore and afloat. However, be wary of it as it is imbued with an inherent weakness, one that can put your vessel’s watertight integrity at risk.
This brass plug, installed in a raw water strainer, is a recipe for dezincification and failure.
Copper
Brass is an alloy of copper, which has been a worthy boat building material for centuries. Its most notable place was in copper cladding hull bottoms to prevent teredo worms from digesting the timbers, as well as being corrosion resistant and a natural antifoulant. In fact, in one form of another copper is the antifouling additive in many bottom paints. It is an excellent biocide and as a result, on today’s cruising boats, in addition to bottom paint, its primary use is in domestic water systems. Beyond its ability to inhibit biological growth, a worthy attribute in a fresh water system, it is opaque. This robs plant-based biological growth, or algae, of one of the necessary ingredients of life, light.
Bronze, unlike brass, contains little or no zinc and is therefore ideally suited to seawater applications.
Copper tube is also used by some engine manufacturers to carry raw water to and from cooling pumps. This usually works well, although the tubing is often of proprietary alloys and shapes, which means it can be difficult to source and expensive. Additionally, it is susceptible to two forms of corrosion that are likely to be seen aboard a cruising vessel. Impingement attack or erosion corrosion is caused by swiftly moving water in a copper pipe or tube. Since copper is relatively soft it can literally be worn away by swiftly moving water, especially sea water. This is especially true at ninety degree turns and restrictions where turbulence and velocity are greater. Copper can also fall prey to decay by exposure to hydrogen sulfide, a common constituent of polluted water.
With its pinkish hue, this failed seawater street elbow is a text book example of brass dezincification,
Brass
Brass, a metal that is almost synonymous with the sea, is actually a family of copper alloys whose primary ingredients, in varying ratios, are copper and zinc. In fact, some brasses are comprised of as much as 50% zinc. Some of the more common “seagoing” brasses are; red brass-85% copper, 15% zinc; cartridge brass-70% copper, 30% zinc; Muntz metal-60% copper, 40% zinc; admiralty brass-70 copper, 30% zinc; naval brass-60% copper, 40% zinc; aluminum brass 76% copper, 22% zinc, 2% aluminum, and finally, manganese “bronze”, 60% copper, 40% zinc. The last in the list, manganese bronze, is, because of its zinc content, actually not bronze at all; it resides squarely in the brass family.
Most shaft bearing shells are made from brass, and this is intentional. Because they are replaceable, they, rather than the strut of shaft log, will corrode.
While brass has many familiar uses aboard; from clocks and joiner work trim to lamps and electrical components, it should, with rare exceptions, be avoided for use below the water line or in raw water applications. It is worth noting that many small (1/4″-3/8″ NPT) plumbing fittings, such as pipe to hose adaptors, pipe plugs and bushings are made of brass while their larger cousins are bronze. Most seacock and sea strainer drains utilize 1/8″NPT plugs. Under no circumstances should these be replaced with brass. Where replacements are needed, one eighth inch bronze plugs can often be obtained from the equipment manufacturer. If unsure of the plug material, avoid using it below the water line or in raw water applications. In my experience, chandlery clerks and many marine equipment vendors cannot be relied upon to provide accurate alloy information, many are unaware of the important distinction between brass and bronze and related prohibitions for use of the former in raw water applications.
Can you tell which of these plugs is brass and which is bronze? While it’s far from scientific, bronze, left, tends to be darker and more copper-like, while brass, right, is often yellow.
Another location where brass is often inadvertently used involves water injection ports on stuffing boxes. These often call for a threaded pipe to hose adaptor of the 1/4″ or 3/8″ variety. Rest assured, and I’ve seen the results personally, making an error of this sort can have dire consequences, including the loss of a vessel.
The green patina or verdigris that forms on copper, while ominous looking, is essentially harmless and no cause for alarm.
If its primary constituent is copper, why is brass so susceptible to corrosion? The answer is simple, because many of the brasses also contain a substantial amount of zinc they are especially susceptible to a type of corrosion referred to as “dezincification”. This is a process whereby the zinc selectively corrodes leaving a porous copper shell that retains its shape but little of its strength. Dezincified components can often be identified by their splotchy reddish or pink coloring. A common example involves propellers. Contrary to popular belief, many propellers are fabricated from a brass alloy (regardless of what it’s called, in order to be considered a true bronze, by definition a copper alloy must contain little or no zinc), and as such are especially susceptible to dezincification. It is, therefore, imperative, to protect this often substantial investment, that sacrificial shaft anodes be monitored and renewed when necessary. In a stainless steel alloy shaft, brass propeller combination, once the anode is gone the next least-noble metal (or metal most likely to corrode) is the brass prop. It will begin to corrode, sacrificing itself for the shaft, which is nobler. Brasses are susceptible to other forms of corrosion in addition to dezincification. A common ingredient of household cleaners, ammonia, will readily attack brass, causing it to weaken and crack. Mercury is also an enemy of brass, as is the aforementioned polluted water.
This high zinc content, leaded red brass pipe nipple nearly resulted in the loss of a vessel. Installed in the air conditioning system raw water plumbing, it failed after less than a year of use.
Suitable Alloys
The requirement for corrosion resistance limits the range of materials from which seacocks and their related components may be made. Only bronze, DZR (more on that in a moment) brass, glass-reinforced plastic and, in some cases, stainless steel may be used. The terms “brass” and “bronze” encompass a wide range of copper alloys. The primary determining factor is zinc content. Zinc is an especially ignoble metal; it corrodes very easily when in the presence of other metals and an electrolyte, such as seawater, which is why it’s used in sacrificial anodes. Zinc, however, also imparts strength to copper, mixing the two, often in about a 40-60 ratio respectively, results in a brass suitable for clocks, lamps and cabin hardware, but most definitely not, with few exceptions, for seawater plumbing.
Copper-zinc alloys used below the waterline undergo a process called dezincification whereby the zinc corrodes from the alloy, leaving behind a pink, porous and very fragile structure that’s almost certain to fail. For the most part, true bronze alloys are zinc-free, their primary elements being copper and tin. Other alloying elements include silicon and nickel (technically making them something other than bronze, but still acceptable for use in seawater plumbing). These are the best alloys for use below the waterline because they are not susceptible to dezincification
Unfortunately, a huge range of alloys lies between true bronze with no, or very little zinc and true brass which contains a high percentage of zinc. Two common alloys often used in marine applications are 85-5-5-5 (or C83600) and DZR. 85-5-5-5 contains 85 percent copper, 5 percent zinc, 5 percent lead and 5 percent silicon and can be used below the waterline. Some European manufacturers use something referred to as DZR brass, a dezincification-resistant brass alloy. This alloy has a higher zinc composition than many other copper alloys (30 percent or more), but it also includes trace amounts of other metals meant to retard zinc corrosion or leaching. Neither of these alloys resists dezincification nearly as well as the zinc-free or near-zinc free bronze alternatives; but as they are less expensive and unlikely to become a problem in the early years of the boat’s life, they can be an attractive alternative for more cost conscious builder.
These chrome-plated brass sex-bolts, installed in a damp wood substrate, eventually succumbed to dezincification.
Bronze
Bronze, although it is a copper alloy, is different from brass in that it is free of any appreciable amount of zinc and as such it is not susceptible to dezincification. Its parent alloying element is, like brass, copper, however, that’s where the similarity ends. Unlike brass its primary alloying element is tin. As a result, pound for pound it is often more expensive than brass, which contains less costly zinc.
On a chandler’s shelf, it’s impossible to determine the zinc content of copper alloys.
Gunmetal, as its name suggests, was, in days of old, used for firearms manufacture. It is a bronze alloy consisting of 88% copper, 10% tin, 2% zinc. It is not especially strong, but corrosion resistant and perfectly acceptable for below the waterline use. It is often used to fabricate such cast items as cleats, chocks and shaft logs.
Installed on the closed cooling, or anti-freeze side, of an engine this pipe worked well until the system was inadvertently filled with ordinary tap water, after which it began to dezincify.
Yet another bronze alloy, aluminum bronze, is strong, but susceptible to de-aluminification. This can be prevented with the addition of nickel, and this alloy is typically referred to as NI-BR-AL (nickel, bronze, aluminum). Propellers are often made of this material and with good reason; it’s strong and corrosion resistant. Manganese is sometimes added to this already mixed soup of metals to further increase strength. Prop repair shops sometimes charge a premium for reworking NIBRAL props due to their tendency to take on a set or memory. This alloy should not be confused with the inferior manganese bronze, which is actually brass.
When copper alloys turn pink, it’s a clear indication of high zinc content, and dezincification.
Silicon bronze is by far the most popular alloy for the fabrication of underwater hardware. Most quality seacocks are constructed of this extremely resilient metal, or one closely related to it. It is made up of 96% copper, with the remainder being silicon and other trace elements, sometimes including very small amounts of zinc, often measured in single percentage points. Bronze hardware such as nuts, bolts and screws are often made of this alloy and can be expected to give long, corrosion resistant service.
This brass drain plug, installed in a seawater strainer, dezincified, and fell out when simply touched.
Phosphor bronze is typically made up of 85-95% copper and 5-10% tin, with the addition of a small amount of phosphorous. The phosphorous improves the hardening characteristics of the bronze, making it a choice material for bearings and springs.
Above all else, remember, brass is ill-suited for most application where it’s called upon to convey or stem the flow of raw/sea water, regardless of whether it’s used above or below the waterline. This includes plumbing associated with raw water strainers, stuffing boxes, seacocks, sanitation and air-conditioning systems.