Moisture Testing
Text and photos © 2020 Steve D’Antonio Marine Consulting, Inc.
Moisture Testing
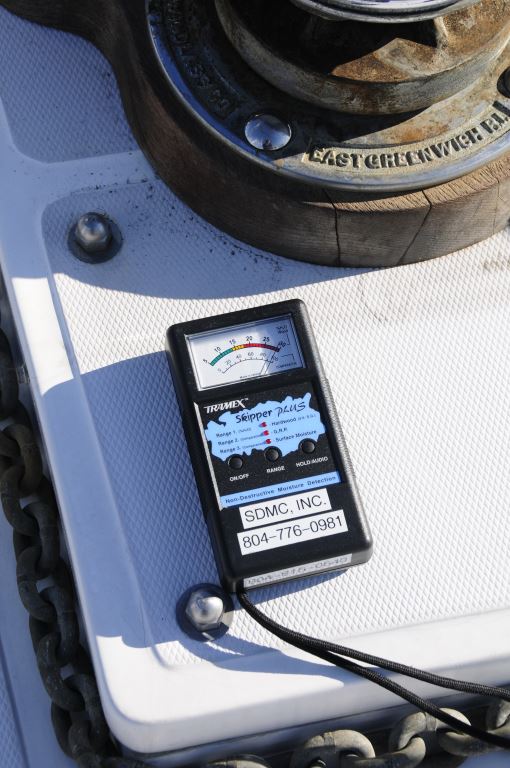
Moisture in fiberglass laminate and in cored composite construction is the source of significant consternation for boat owners, buyers and builders alike. Nothing can kill a used boat sale faster than the banshee-like shriek of a moisture meter being passed over saturated core or wet hull laminate.
Moisture meters have been used in the marine industry for decades; some would say they’ve been a boon, others a curse. I’m one of the former, while many of my broker colleagues are the latter. So, who’s right?
Non-destructive moisture meters work by sending an electromagnetic or radio wave, through the material being measured, interpreting the affect on that wave by moisture, and then converting it into a useful reading on a digital or analogue scale.
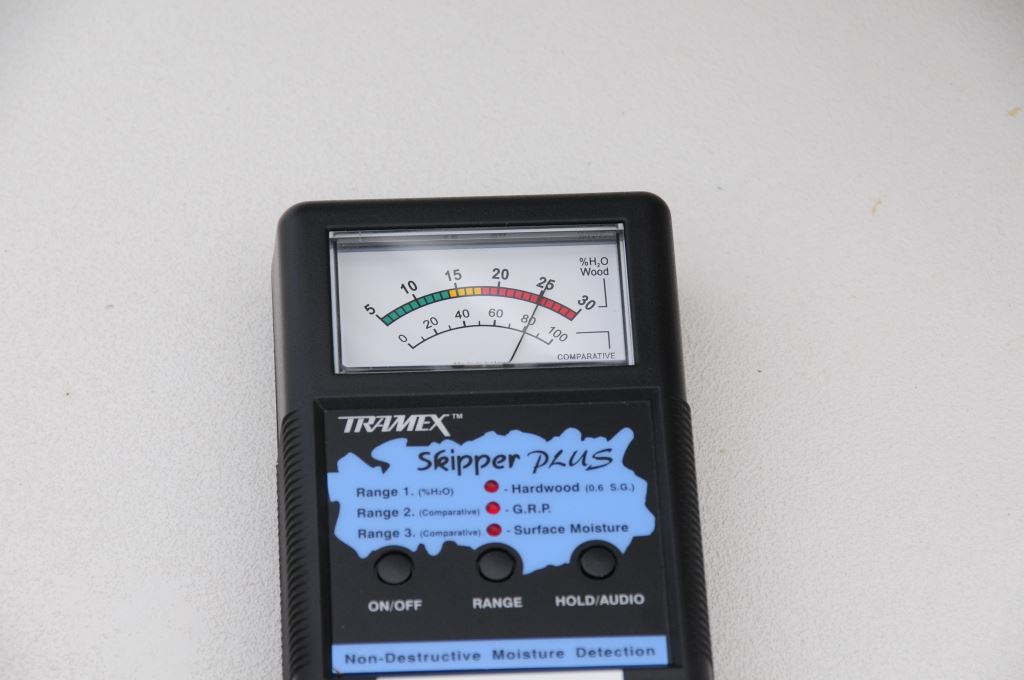
The most common applications for moisture meters, in the marine industry, are for the detection of moisture within cored composite structures, otherwise known as fiberglass sandwich construction, and for the assessment of solid fiberglass laminates in cases of osmotic blister analysis and repair.
Cored composite structures are especially susceptible to water entry. If the core is hygroscopic and organic, balsa or plywood for instance, water entry will eventually lead to deterioration and production of the dreaded coffee-colored stains issuing from penetrations. By the time those make an appearance, the damage has already started, so it’s best caught early, making a moisture meter valuable, as it can “see” through fiberglass skin to determine if water is present, even if there’s no external evidence.
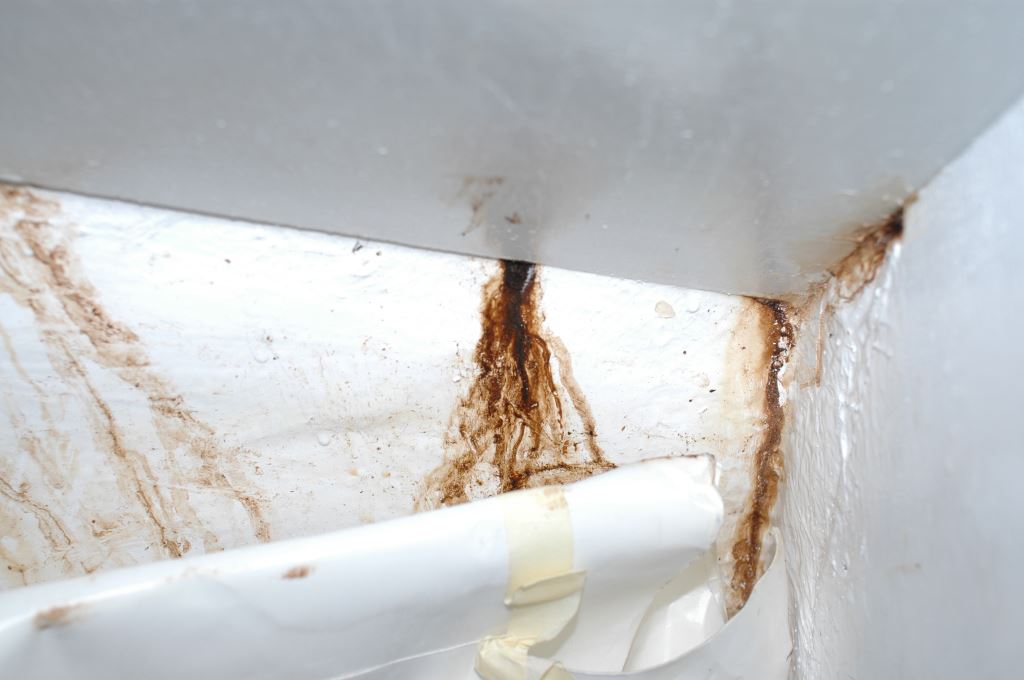
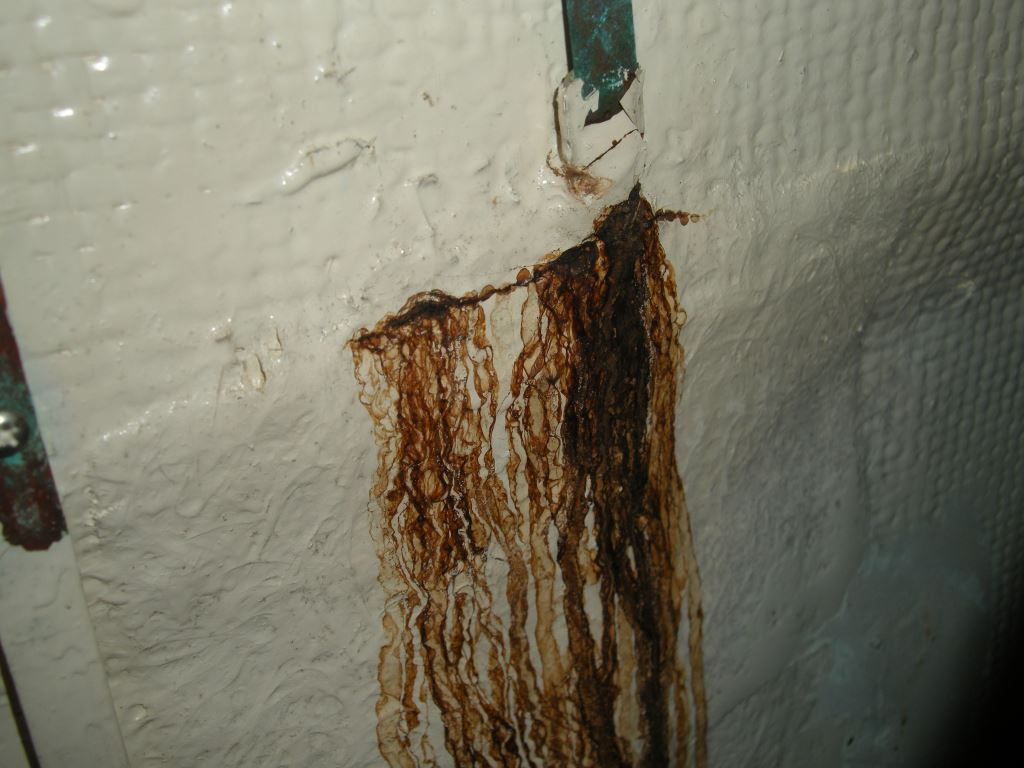
Non-hygroscopic, synthetic core is not entirely immune from the woes of water entry, voids between core blocks (these should be filled with resin or putty) can channel water over long distances. It’s important to note, even core that feels dry to the touch can contain significant water.
In the case of solid laminates, I have used moisture meters on countless occasions to assess the extent of osmosis coverage and penetration. Once again, the meter can determine if moisture is present in a solid laminate even if all looks well to the naked eye. Where osmosis repair is concerned, the moisture meter will enable a fiberglass specialist to determine how deeply the moisture has penetrated using a technique called patch testing. At this point the non-destructive moisture meter requires destructive technique, as an approximately 10” by 10” patch is ground into the hull, one laminate at a time, measuring moisture content with each pass, until a “dry” reading is obtained. With that information, it is then possible to determine how many laminates require removal and replacement. Without a moisture meter, this would be an impossible task.
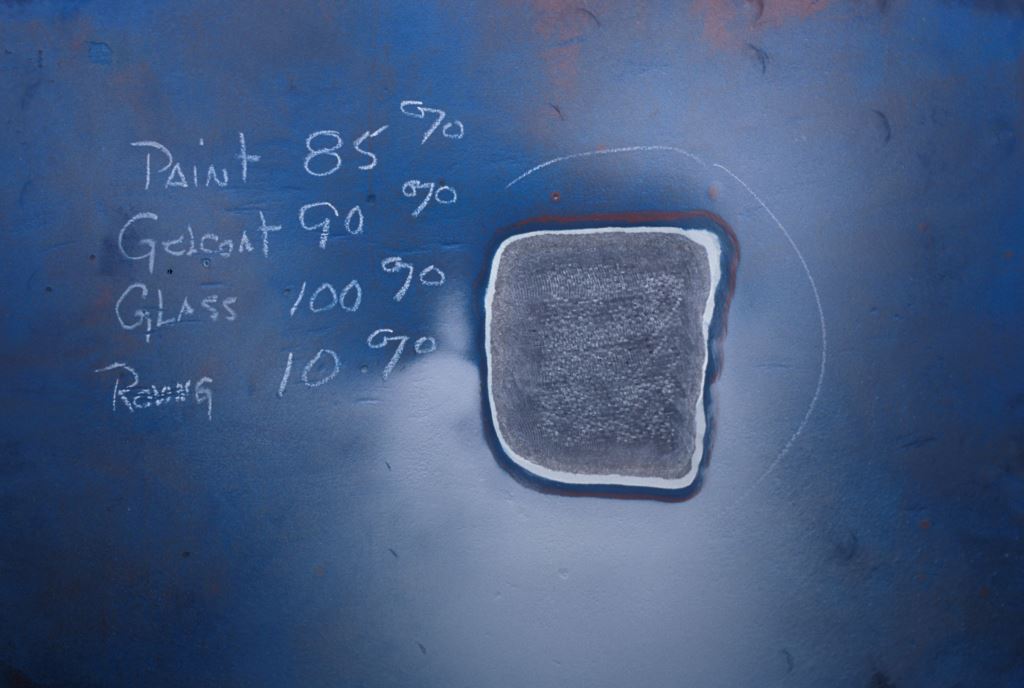
As good as moisture meters are, they do have a few potential short comings. Primary among these are the tendencies to read metal has complete saturation, and ice as dry. Therefore, moving a moisture meter over a laminate structure that has embedded metal, a metal backing plate or a metal tank on its far side, will likely yield false results. Likewise, using a moisture meter in sub-freezing conditions is virtually guaranteed to show anything over which it’s passed as dry, regardless of moisture content.
Moisture meters are also susceptible to being fooled by surface moisture, however slight it may be. For the meter I use, A Tramex Skipper Plus, the electrodes consist of two soft foam rubber like pads that are pressed against the surface being measured. The slightest degree of surface moisture, even that from a sweaty palm, can have an affect on readings. Therefore, it’s critical the surface be absolutely dry. Additionally, if measuring moisture in bottoms, the hull should be allowed to dry for at least 24 hours depending on climate and temperature, as anti-fouling paint can retain moisture. Additionally, the metal contained in some paints, bottom and topside, can skew meter readings. If I encounter a reading, which I consider to be unusually high, I may call for removal of paint in a small area, to determine if it’s having an effect on the meter’s readings. That’s relatively easy to accomplish on a bottom, but not so easy for topsides. In the latter case, taking readings from inside the hull is an approach that may be useful.
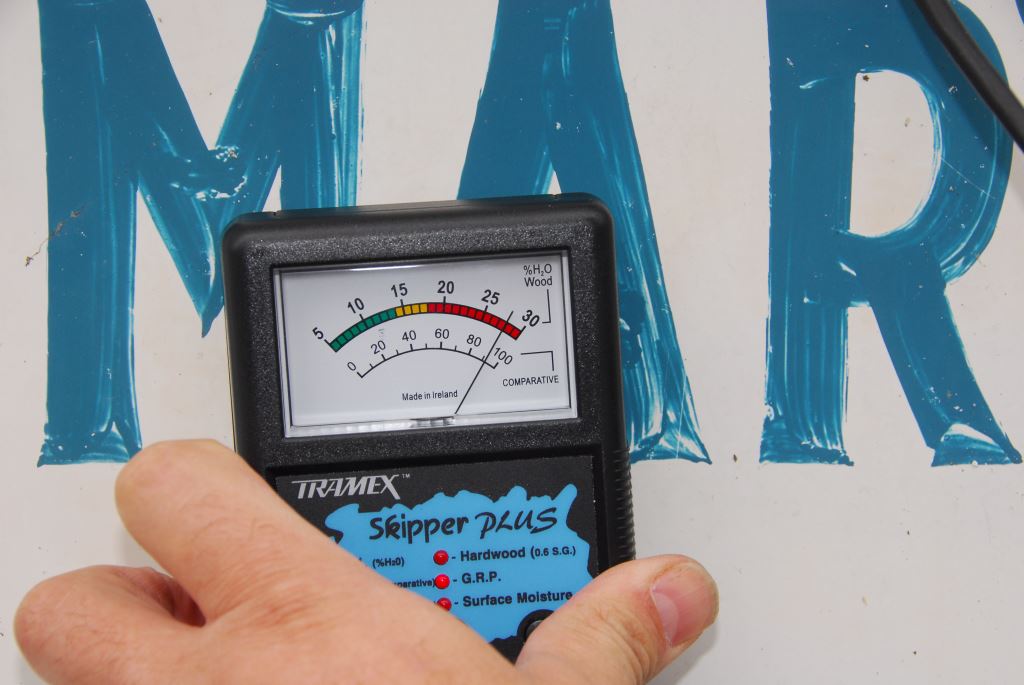
Finally, while anyone can learn how to use a moisture meter, I don’t believe this is a do it yourself tool. In the hands of an amateur, or an inexperienced professional, the results can be questionable, fueling the skepticism of, among others, the brokerage community.
The most effective way to learn the idiosyncrasies of a moisture meter is to use it often, on a variety of vessels, and then see what’s actually beneath the surface as it’s (destructively) exposed for repairs. That type of experience is difficult to obtain outside the industry. If you suspect the presence of water in a laminate or core, hire a professional who has hundreds of hours of moisture meter experience under his or her belt; doing so is likely to yield the most reliable results.