Editorial: Hotel Quarantine – Feature Article: Over-Current Protection
Text and photos © 2020 Steve D’Antonio Marine Consulting, Inc.
From the Masthead
Hotel Quarantine
Imagine spending two weeks in a hotel, without setting foot outside the door for the entire time. Other than Howard Hughes, how many people can say they’ve done this? I never thought I would, but then again COVID has ushered in many firsts.
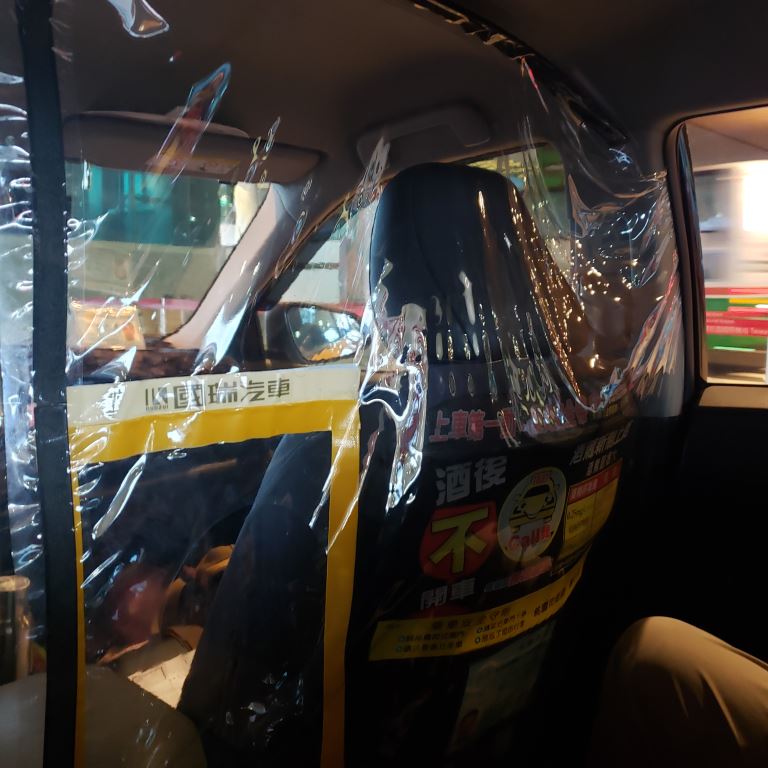
I traveled to Taiwan recently for a pair of new build inspections; one of the stipulations for doing so, in addition to obtaining a special visa, was a strict two-week quarantine upon arrival. Typical of the Taiwanese, the quarantine ran like the proverbial well-oiled machine, in advance of, during and after arrival there were numerous forms and documents to sign and review. An entire hotel in Taipei was converted to a quarantine facility, and there was even a “Pandemic Taxi” to take me from the airport to the lodging. Once there, the few staff I encountered were covered from head to toe in gowns and face shields (it reminded me a little of that sci-fi movie “The Andromeda Strain”), and yet they were ever friendly and supportive. Meals, which were delivered three times a day (this was accompanied by a pre-recorded notification call on the room phone), were interesting, healthy and varied, mostly Taiwanese but occasionally including a western favorite like pizza, pancakes, French toast or chicken nuggets. A special website was made available to guests, enabling them order more varied food (fortunately this included ice cream). Internet was fast and with no interruptions, enabling me to work normally, as well as engage in regular video conferences.
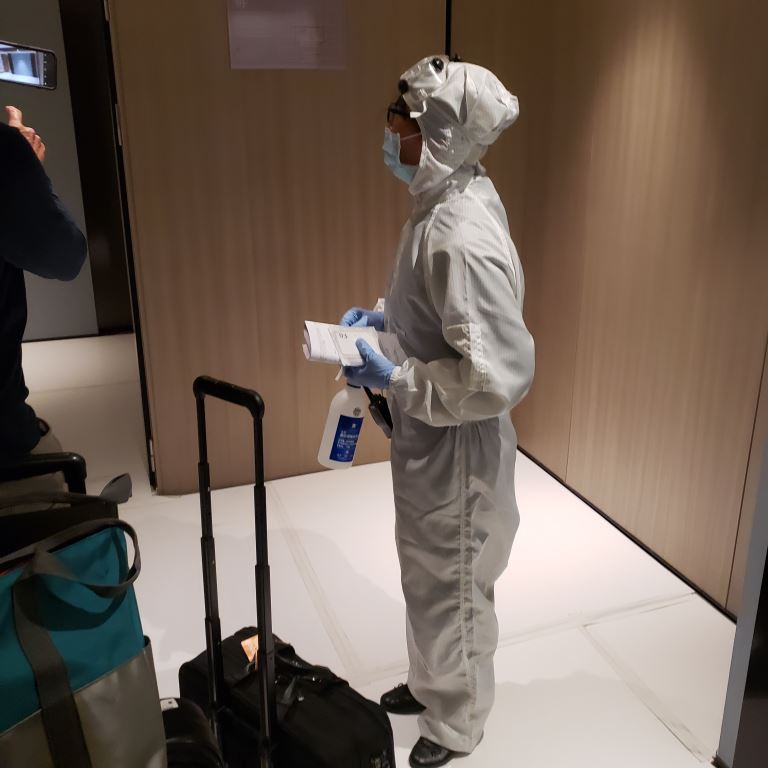
Every meal included a small card inscribed with a prayer (one came with a picture of a cow driving a locomotive adorned with flags), and every few days a meal included a surprise, a small game, or puzzle.
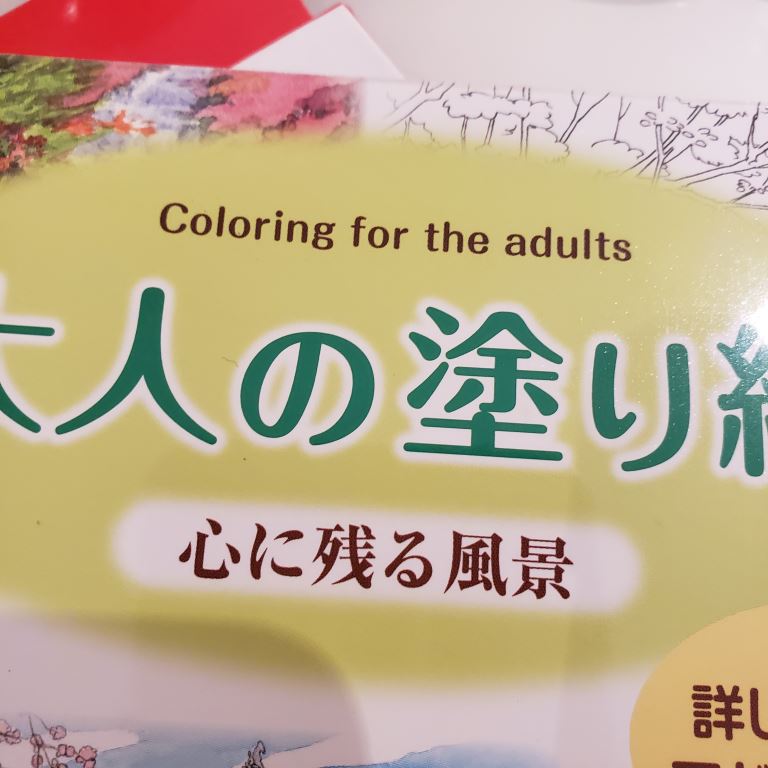
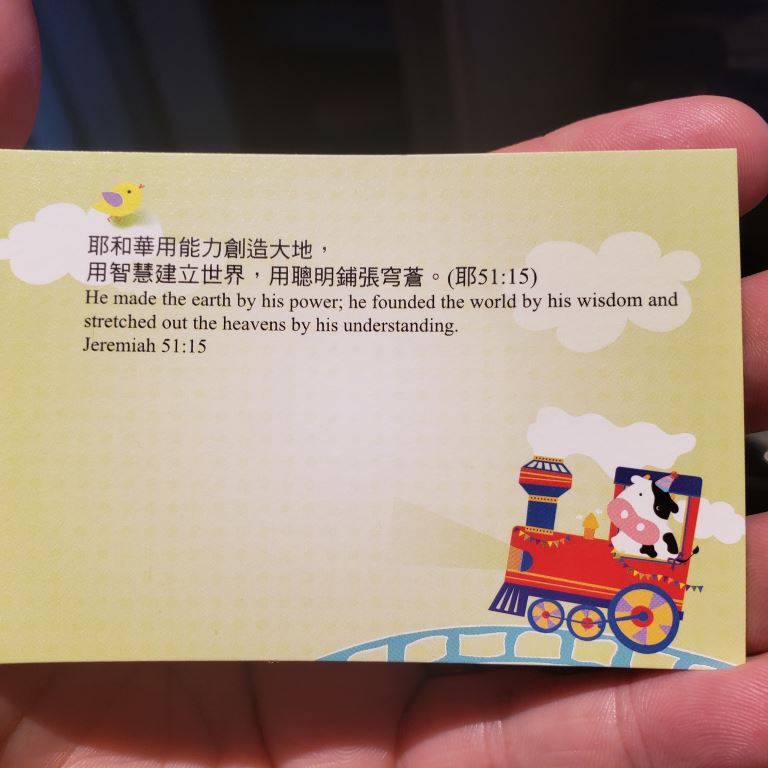
Staying busy wasn’t a problem, I have a deep backlog of articles to write, PowerPoint presentations to prepare, photos and book chapters to edit. By nature, I’m a solitary person, I don’t mind being alone, and I don’t get lonely. By day two, however, I realized I would need to establish an exercise routine; while I am solitary, I’m not sedentary. I began a minimum of four 20-minute power walking sessions a day, the room was 15 paces end to end, netting me about 11,000 steps/day.
On the second day of quarantine I was visited by two police officers, they gave me a cell phone; they explained they would use it to check in with me on a daily basis, either by voice or text. Sure enough, I received text messages every day asking how I was feeling. However, I also received a call from a woman asking if I wanted Chinese language lessons. I politely declined, however, she called back a few times so I stopped answering the phone. That worked OK until the police tried to call me, and I didn’t answer. They became concerned and eventually called my client, who had arrived with me to confirm I hadn’t escaped. I called them back and set the record straight, assuring them I had not left the room.
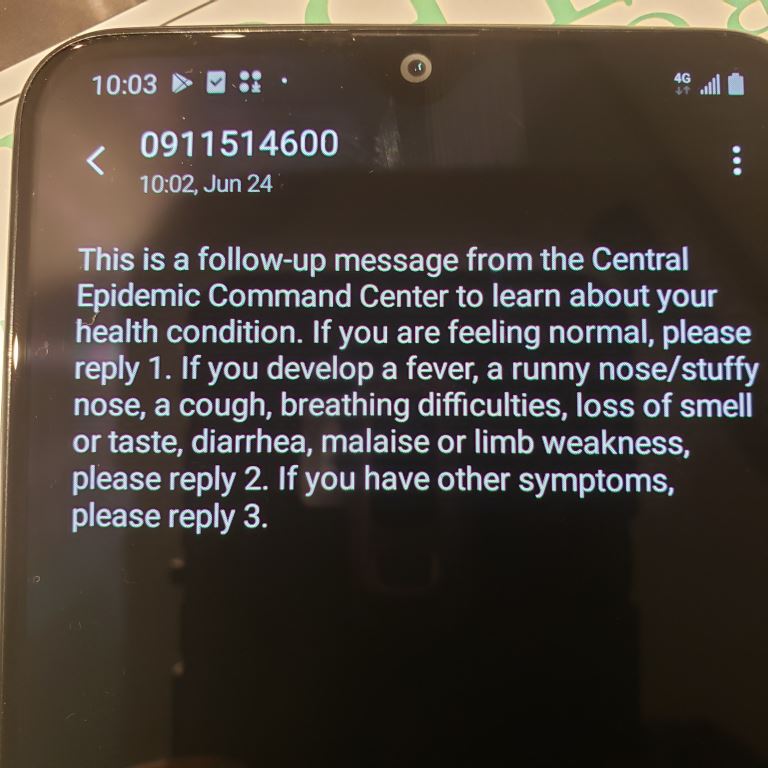
Once released, I was able to travel around Taiwan freely. It was a respite in that they have so few cases, thanks to their strict measures and being an island they can control entry very easily, and thus there are very few restrictions, masks are optional, people are shaking hands (it felt strange), hugging, and meeting in crowded restaurants. As I’ve said in this column in the past, I can’t speak highly enough of the Taiwanese, they are among the most industrious, hard-working and goal-oriented, as well as kind and generous people I’ve ever had the pleasure of working with. My hat is off to them in managing not only COVID, but allowing select business travelers to enter the country and doing so in a safe, efficient manner.
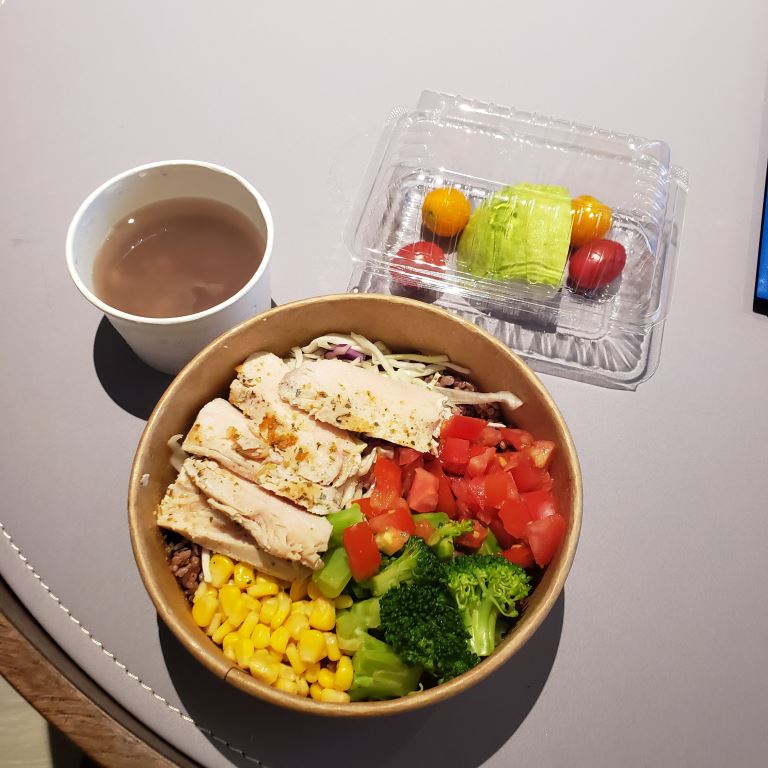
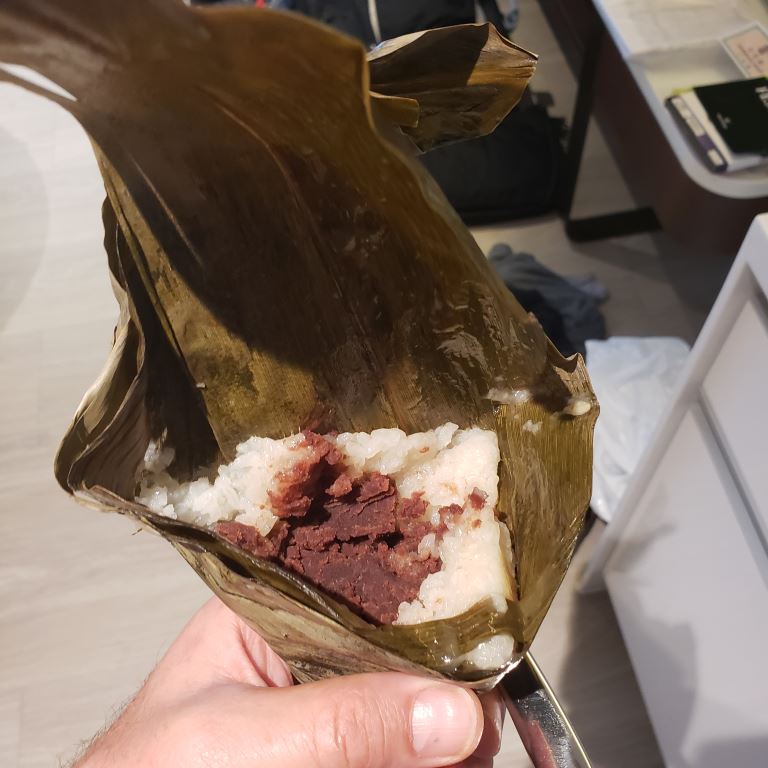
While a two-week quarantine is not something I’m anxious to repeat anytime soon, it was gratifying to know I could do it.
This month’s Marine Systems Excellence eMagazine covers the subject of over-current protection. I hope you find it both interesting and useful.
Over-Current Protection, and Why it’s so Vitally Important
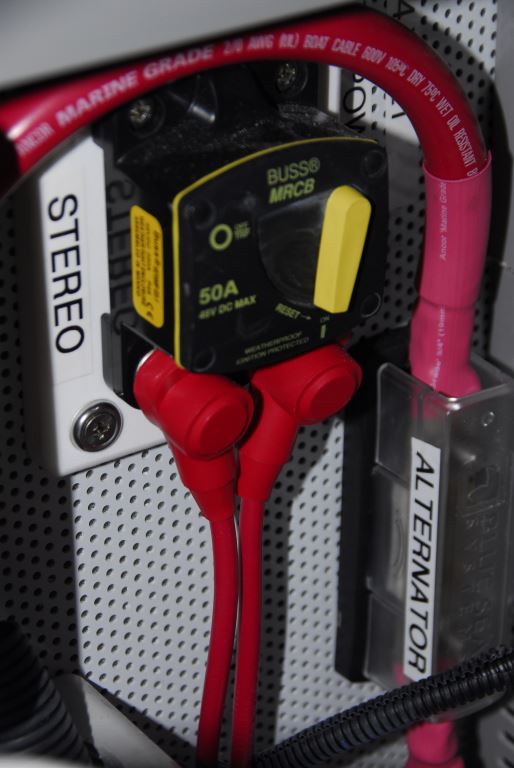
I vividly recall my first encounter with over-current protection, or more accurately the lack thereof. As a teen-age would-be marine electrician, with more ambition than knowledge, I’d wired a light under the foredeck of the family 16-foot outboard runabout. The wire run passed adjacent to the steel fuel tank and the shelf on which it rested. After a summer’s worth of use the wire, which I had neglected to secure properly, worked its way under the tank, whose sharp metal edge chafed through the insulation while underway. In an instant a cloud of dense white smoke erupted from under forepeak, enveloping the cockpit and its occupants. Mercifully, the wire was a small gauge, and it melted, breaking the circuit before it could ignite the shelf, or ‘plasma cut’ its way through the light-gauge, and somewhat rusty, sheet metal fuel tank, it was all over in just a few seconds. While I quickly figured out what had happened, at that young age I assumed my only error was in not properly routing the wire; however, as I grew older and wiser, I eventually learned about over-current protection and its importance. That episode, however, and the acrid smell of that short circuit, has stayed with me ever since.
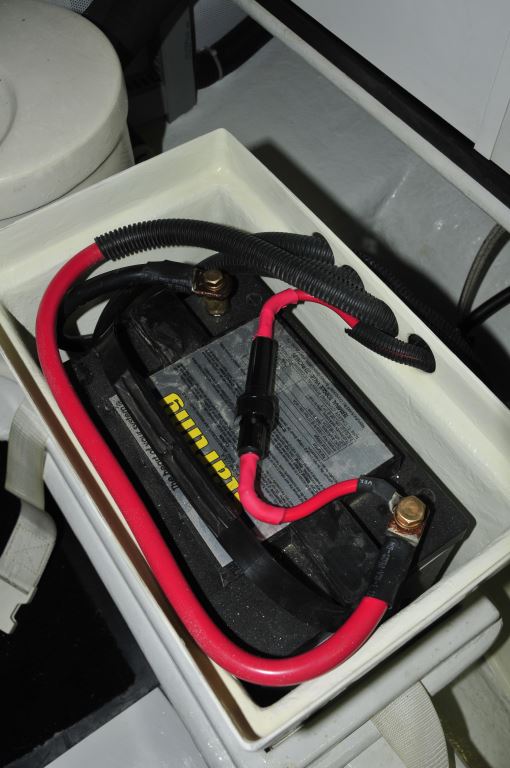
Over-current protection, OCP for short, is simply a catch-all phrase for the proper implementation of fuses and circuit breakers. With just a few exceptions, which are detailed below, OCP plays one primary role in ensuring the safety of an electrical system; it protects wiring, and contrary to all too popular belief, not the power consumer or appliance, from overheating and a potentially starting a fire.
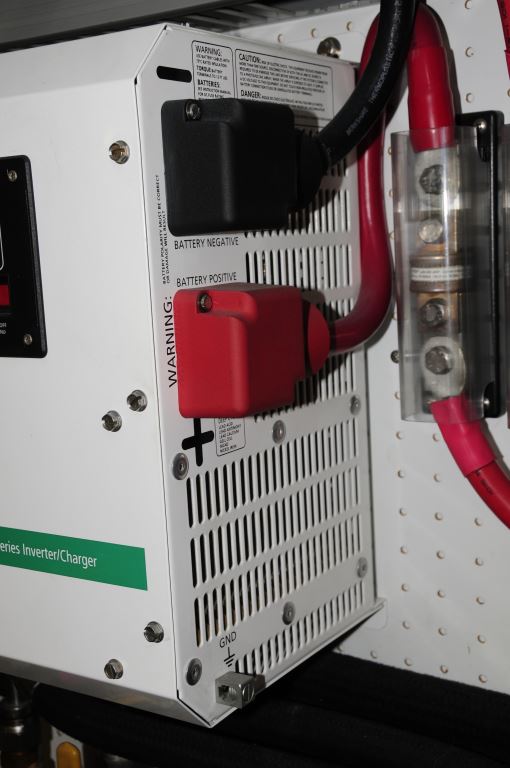
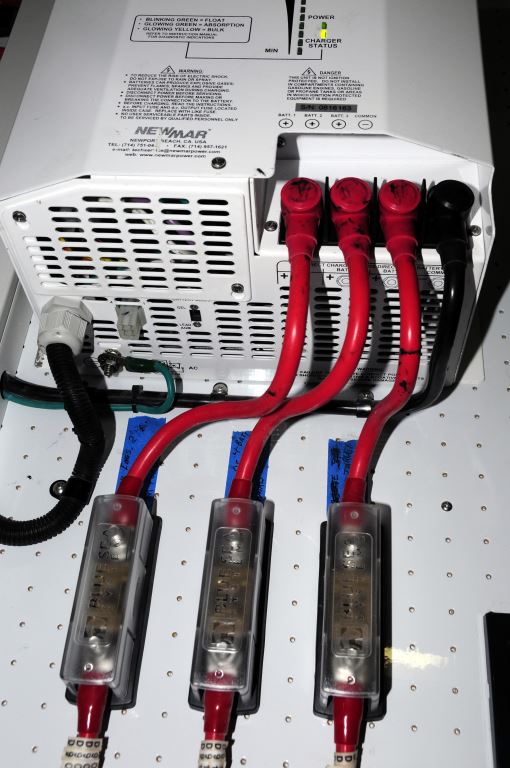
In the vessel inspections I conduct, incorrectly-installed, incorrectly-placed, incorrectly-selected, or altogether absent, OCP is a dreadfully common occurrence, one all savvy marine technicians, not just electricians, must understand and be able to identify. Ideally, boat owners too should have at last a rudimentary understanding of the basic requirements where OCP is concerned.
Complicating this issue is a common misunderstanding regarding high resistance vs. low resistance electrical faults. The latter, essentially a short circuit, can be dealt with by OCP, the former cannot. A corroded or loose connection presents high resistance (and typically low current or amperage flow) to current flow, while a single screw driven through positive and negative conductors represents a low resistance (typically associated with high current flow) short-circuit. Therefore, a poor, high resistance connection, think of a corroded, wet, salt-encrusted shore power plug, can generate significant heat, leading to a fire, without ever causing the OCP to trip or blow. OCP provides protection for low resistance faults, such as short circuits, or overloaded circuits, which might occur, for instance, when operating three air-conditioning units, a water heater and battery charger on a single 30-amp shore power cord, or if a shore power cable gets pinched between a hull and steel piling.
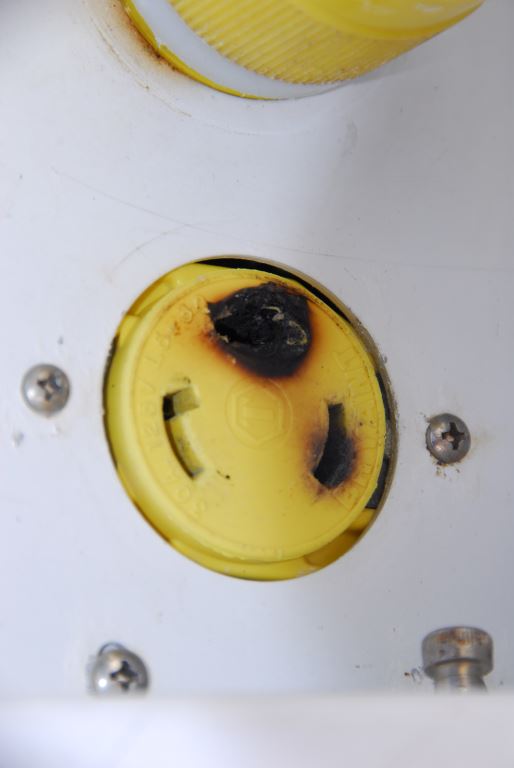
General Requirements
Where AC and DC systems are concerned, American Boat and Yacht Council guidelines are exceedingly clear on where and how OCP must be employed. For DC systems, OCP must be installed within 7 inches of the source of power, measured by wire length. The exceptions to this mandate, which are critically important, quoted from ABYC E-11.10.1.1, are as follows…
- Cranking motor conductors [because no OCP is required, special care must be taken in routing of the positive cable, among other things it must not make contact with the engine other than at the point where it connects to the starter positive post].
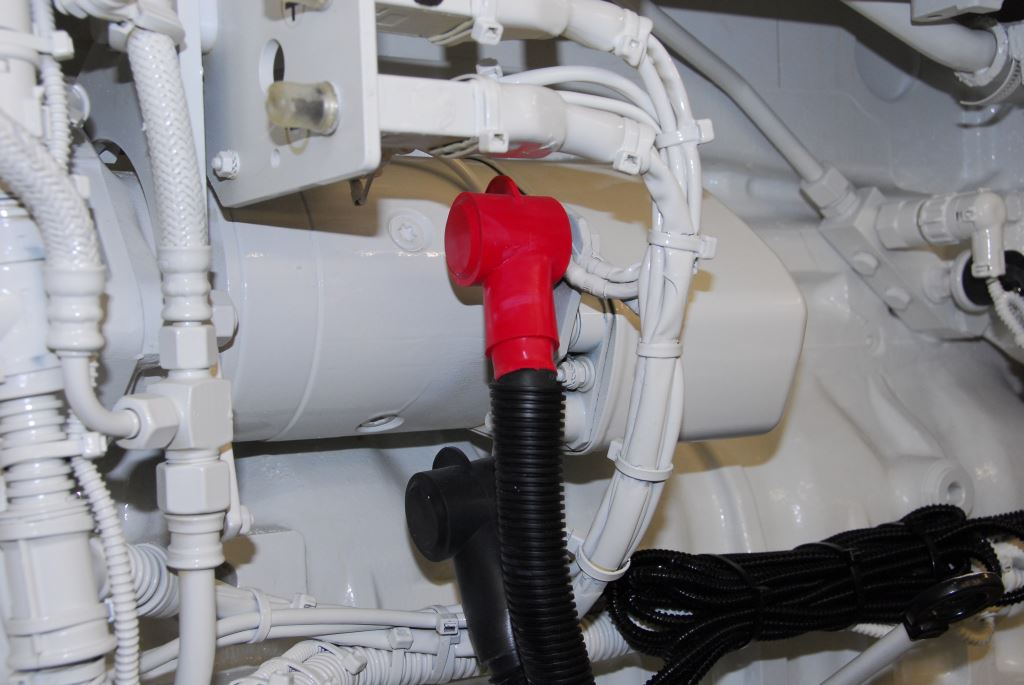
- If the conductor is connected directly to the battery terminal and is contained throughout its entire distance in a sheath or enclosure such as a conduit, junction box, control box or enclosed panel, the overcurrent protection shall be placed as close as practicable to the battery, but not to exceed 72 inches (1.83 m).
- If the conductor is connected to a source of power other than a battery terminal [this could be a battery switch, starter post or bus bar] and is contained throughout its entire distance in a sheath or enclosure such as a conduit, junction box, control box or enclosed panel, the overcurrent protection shall be placed as close as practicable to the point of connection to the source of power, but not to exceed 40 inches (1.02 m).
- Overcurrent protection is not required in conductors from self-limiting alternators with integral regulators if the conductor is less than 40 inches (1.02 m), is connected to a source of power other than the battery, and is contained throughout its entire distance in a sheath or enclosure.
- Overcurrent protection is not required at an alternator if the ampacity of the conductor is equal to or greater than the rated output of the alternator.
- Pigtails less than 7 inches (178 mm) in length are exempt from overcurrent protection requirements.
In addition to [these provisions], the ungrounded conductors to a battery charger, alternator or other charging source shall be provided with overcurrent protection within the charging source, or within seven inches (178 mm) of the charging source, based on the maximum output of the device.
EXCEPTION: Self-limiting devices [this includes alternators and chargers].
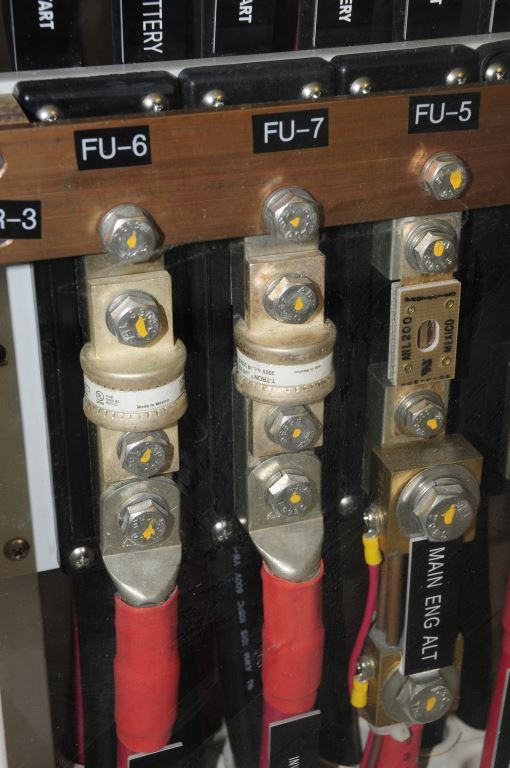
For AC circuits, the requirements are slightly different.
- Each ungrounded current carrying conductor shall be protected by a circuit breaker or fuse.
- A circuit breaker or fuse shall be placed at the source of power for each circuit or conductor except…
- If it is physically impractical to place the circuit breaker or fuse at the source of power, it can be placed within seven inches (178 mm) of the source of power for each circuit or conductor, measured along the conductor.
- If it is physically impractical to place the circuit breaker or fuse at or within seven inches of the source of power, it can be placed within 40 inches (102 cm) of the source of power for each circuit or conductor, measured along the conductor, if the conductor is contained throughout its entire distance between the source of power and the required circuit breaker or fuse in a sheath or enclosure such as a junction box, control box, or enclosed panel.
- Additional Overcurrent Protection – If the location of the main shore power disconnect circuit breaker is in excess of 10 ft (three meters) from the shore power inlet or the electrical attachment point of a permanently installed shore power cord, additional fuses or circuit breakers shall be provided within 10 ft (three meters) [the closer the better] of the inlet or attachment point to the electrical system of the boat. Measurement is made along the conductors.
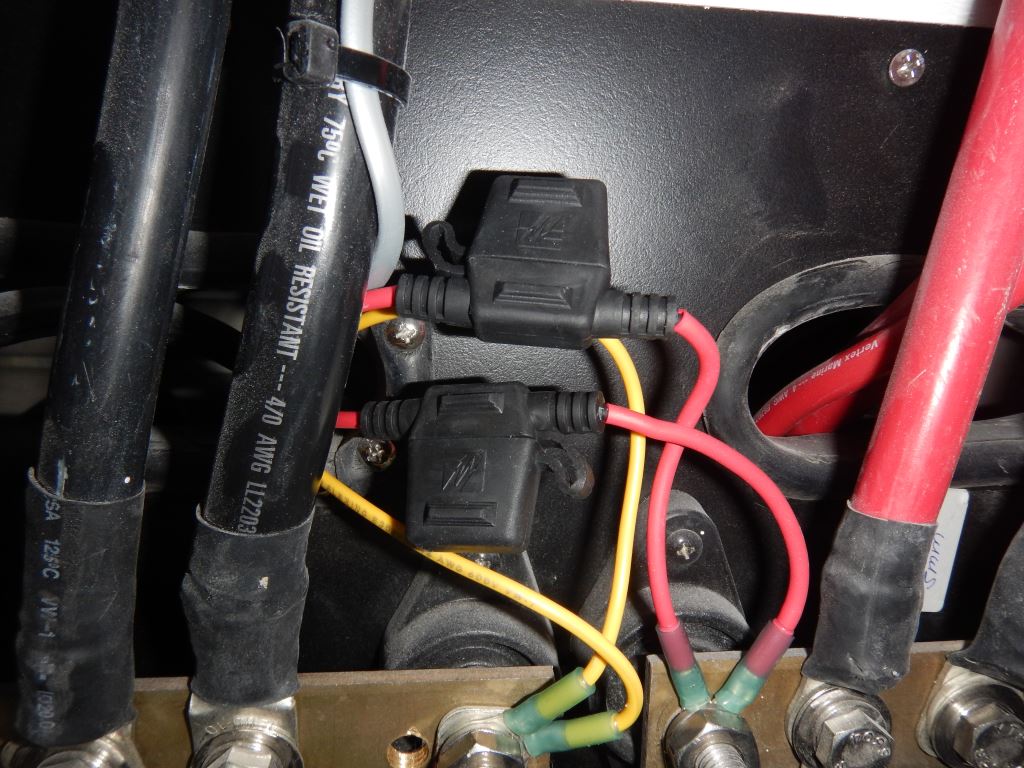
The italics are mine, emphasizing the need to place OCP as close as possible to the source, rather than at the maximum allowable distance. Remember, each inch of wire between the power source and OCP is unprotected and, in the event of a short circuit, could lead to a fire.
Requirements for motor loads present more variations on this theme…
- AC Motors – Each motor installation, and each motor of a motor operated device, shall be individually protected by an overcurrent or thermal protection device.
EXCEPTION: Motors that will not overheat under locked rotor conditions.
Alternators
It’s worth noting, where alternators are concerned, in spite of the exceptions, if the alternator’s positive output cable leaves the engine, it must be over current protected where it connects to the vessel’s batteries or DC bus, following the standards detailed above. Furthermore, I’m not in agreement with exception number five. If a high output alternator’s output cable shorts to an engine block or other grounded structure, a shaft or fuel tank for instance, regardless of whether or not the cable is capable of conveying the current, the ground source may not be, or may not always be, and thus the potential for arcing and substantial heat generation remains a significant concern for me. For more on this see here. It is, therefore, my recommendation that OCP be installed at both ends of an alternator’s positive output cable.
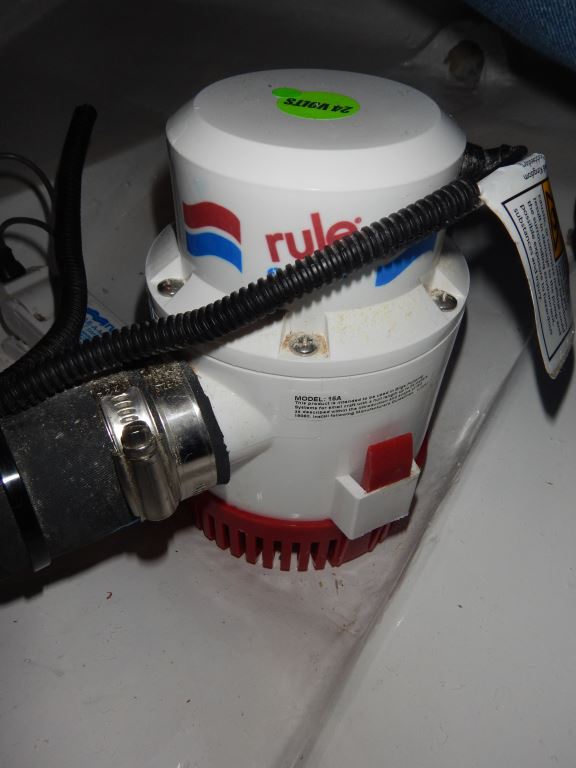
Battery Banks
Positive cables connected to battery banks used for purposes other than starting loads are, like any other DC conductor, required to be equipped with OCP in accordance with the above-described guidelines. For comparatively small banks, 2200 cold cranking amps (CCA) or 500 amp-hours or less, common ANL-style fuses are typically used (see ABYC Table IV-A for specific guidance). However, for banks that exceed this capacity, OCP that possesses a higher ampere interrupt capacity (AIC) is required. The ABYC Standard mandates that the AIC of OCP used in this application must be at least equal to the battery manufacturer’s short circuit rating (this could be up to five times the CCA rating for AGM batteries, and even higher for Lithium Ion), which often calls for a class T fuse, as the interrupt capacity of the ANL fuse is woefully inadequate. In some cases, for exceptionally large banks, even a class T fuse may not meet the requirements.
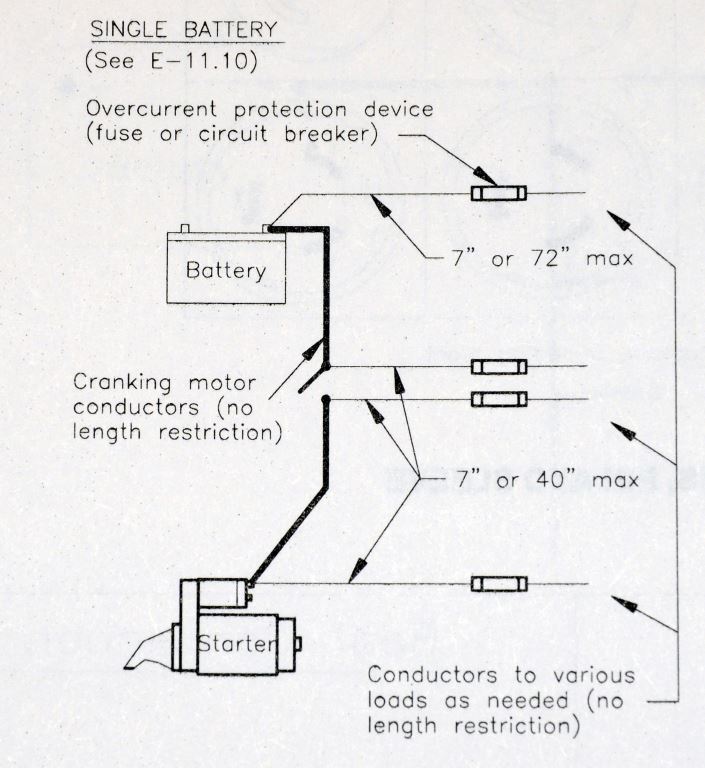
Motors
Motor loads present yet another set of challenges for OCP. ABYC E-11.10.1.3.1 clearly spells out the requirements, “Motors and motor operated equipment, except for engine cranking motors, shall be protected internally at the equipment, or by branch circuit overcurrent protection devices suitable for motor current. The protection provided shall preclude a fire hazard if the circuit, as installed, is energized for seven hours under any conditions of overload, including locked rotor.” The following guidance notes are also included for this standard, “It may be necessary to use thermally responsive protection devices on the equipment or system if the motor is not capable of operating continuously at maximum possible loading.” And, “It may be necessary to test as installed in order to assure compliance with the locked rotor requirement. Voltage drop, due to wire size, and delay characteristics of the overcurrent protection device may have to be adjusted to protect the motor.” Ultimately, unless a motor possesses the requisite internal thermal protection, and some do not, it may be necessary to install OCP at the motor to meet this requirement, in addition to OCP that’s present for the branch circuit serving the motor. Alternatively, there is no requirement to size OCP for a conductor’s maximum current carrying capability. Therefore, the main OCP for a motor’s branch circuit may be sized to provide adequate protection for the motor itself, even if it’s under-sized per se for the wire size, as the wire size may be larger in order to reduce voltage drop.
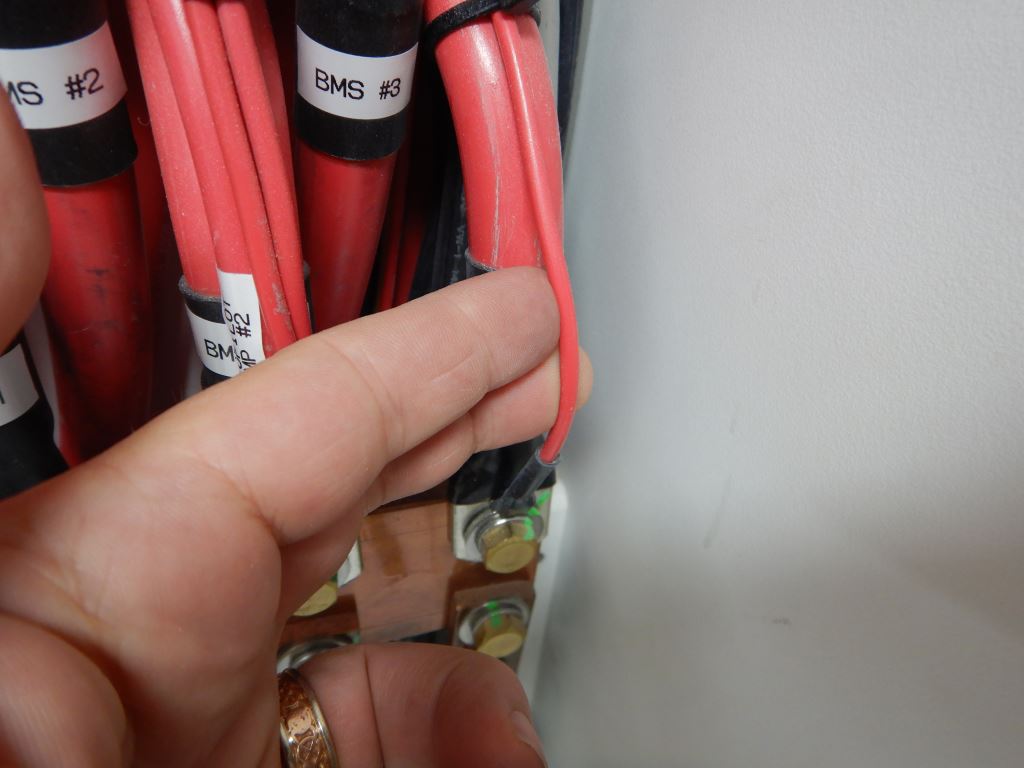
Because starter motor high current conductors are exempt from the OCP guidelines, the routing of the starter positive cable must be carried out with extreme care, it must be protected from any possibility of chafe with grounded objects, including and especially the engine itself. In fact, ABYC guidelines prohibit the starter positive cable from touching the engine, saying, “The ungrounded [positive] battery cable shall be routed to avoid contact with any part of the engine or drivetrain.” It must be routed from the starter without making contact with the engine, transmission, brackets or any other associated parts. Furthermore, my own guideline for starter cabling includes keeping positive and negative cables separated from each other; if either overheat, from a short or lightning strike, they could melt into each other.
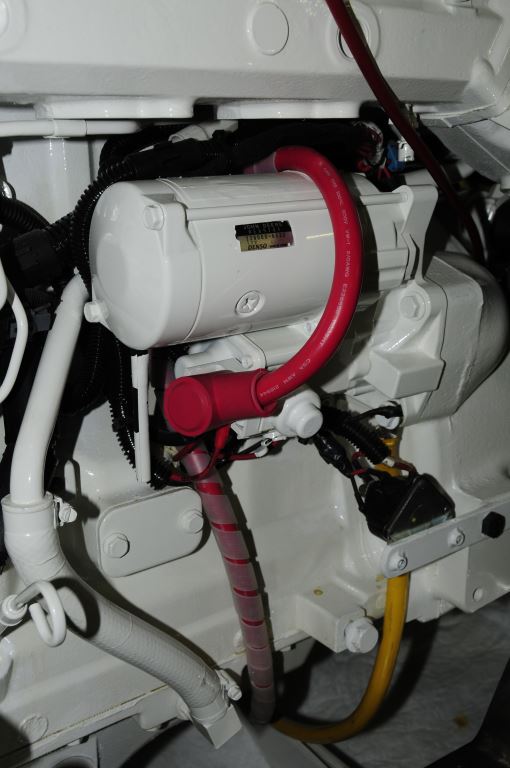
Some builders do include a fuse on starter circuits; there is no standard that prohibits this; however, many believe, and I agree, this presents a serious liability, in that a weak starter battery will induce higher starter current draw, which in turn could lead to a blown starter circuit fuse. In the event an engine needs to be started quickly, if for instance a vessel is drifting onto a lee shore, or is in danger of being run down, and the starter fuse blows, the results could be catastrophic.
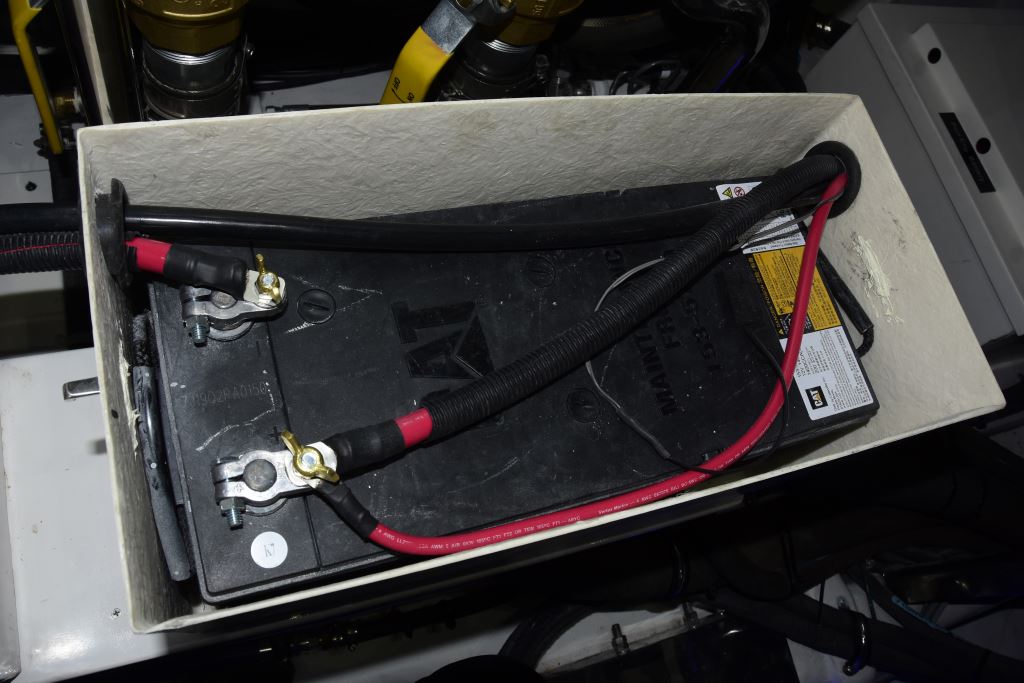
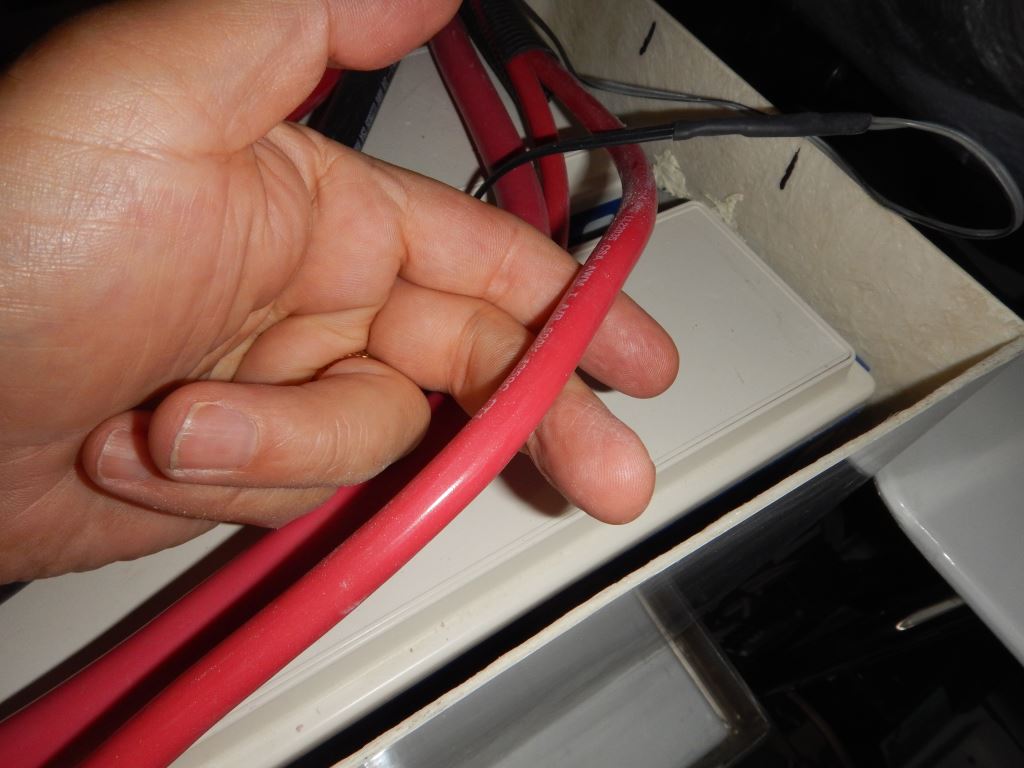
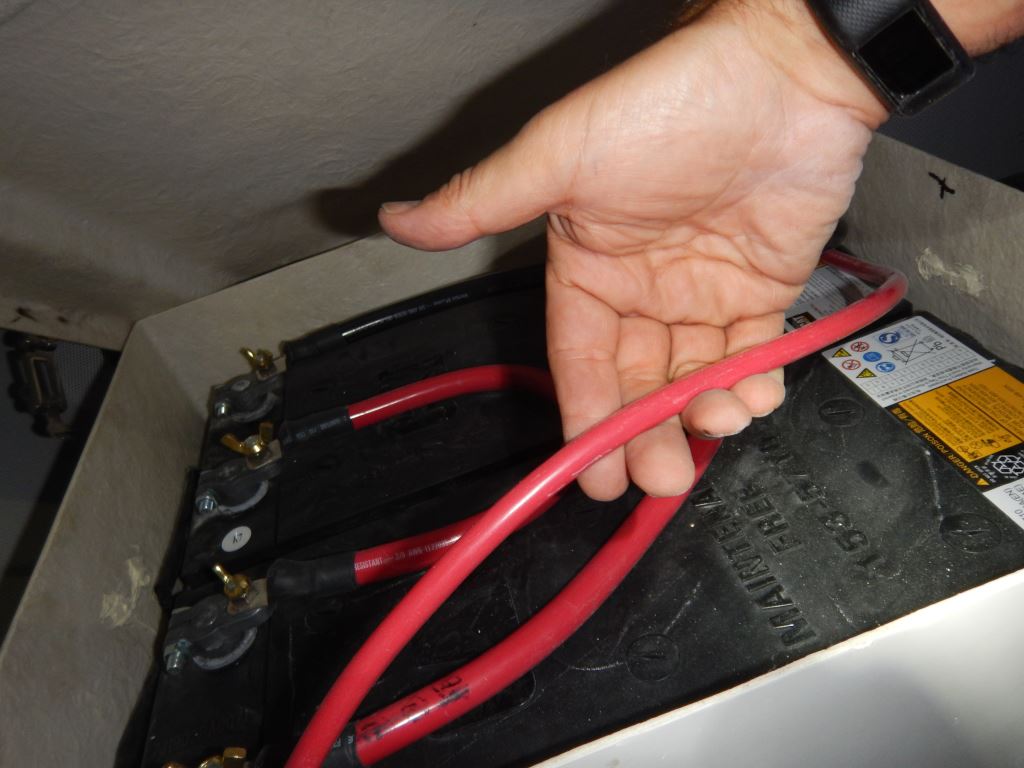
In short, if you can follow an unsheathed wire leaving a battery, one that is not used for starting, and you don’t encounter OCP within 7-inches, it represents a violation. If it is sheathed, and you don’t encounter OCP within 72-inches, that too represents a violation. Finally, every inch of wire between a battery (or other power distribution source such as a battery switch, starter post or bus bar, to which smaller gauge, and thus under-protected, cables are connected) and OCP is unprotected, if a short circuit occurs in that area, the wire will overheat, and in doing so may cause a fire. ABYC approved sheathing, by the way, includes conduit, approved (and thus fire resistant and continuous) split, rather than spiral, loom and even electrical tape, although that’s not recommended. The familiar translucent or black spiral wrap loom lacks ABYC compliance in that it provides incomplete protection, and in most cases it lacks flame resistance.
Pay careful attention to OCP requirements, they is among the most commonly violated of ABYC Standards. Failure to comply with the standards is among the most common causes of onboard fires.