Selecting Primary Fuel Filters; There’s more to it than meets the eye – Editorial: A Loose Bolt, a Cigarette Lighter and Distracted Work
From the masthead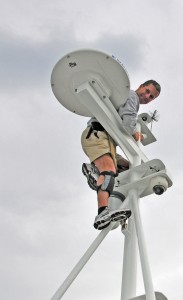
A Loose Bolt, a Cigarette Lighter and Distracted Work
Last year I wrote an editorial about a ship that lost control, and struck a pier, causing over $2m in damage. The culprit…an incorrectly torqued set screw, one that had been installed more than four years before the accident occurred.
In April of 2021 a similar, albeit more costly, event took place, “An improperly tightened fastener led to a diesel engine failure on a Washington State Ferries passenger and car ferry near Bainbridge Island, Washington…” from a recent story in the online publication gCaptain.
When I managed boat yards, one of my greatest frustrations, and the thing that kept me up nights, was absent-minded, forgetful or routinely distracted technicians, they were the ones responsible for, among other things, installing but failing to tighten hose clamps. It was an egregious and unforgivable error, one that ultimately led to me establishing a rule, ‘no fastener, including clamps, shall be installed unless they are completely torqued, if you can’t complete the installation, leave it disassembled so it’s obvious it isn’t done’, thus avoiding the case of me finding a loose fastener/clamp, and having the installers offer the excuse of, “I wasn’t finished”, or, “I was going to come back and tighten it later”, maybe they would, maybe they wouldn’t, I hated not knowing.
The gCaptain story continues, “…details the NTSB investigation [into the] …catastrophic failure of the no. 3 main engine aboard the Wenatchee during a sea trial in Puget Sound. The failure led to the ejection of components from the engine and resulted in a fire in the no. 2 engine room. …damages were estimated at nearly $3.8 million.”
The report continues…
“During the maintenance period, two of the four main diesel engines, numbers 2 and 3, were overhauled by factory-trained technicians. Following the completion of engine overhauls… the vessel crew conducted engine tests. [Low oil pressure] alarms activated for the no. 3 main engine. Crew members found pieces of a cigarette lighter in the lube oil system. Technicians returned to inspect the engine and recover the pieces, [subsequently] advising WSF it was acceptable to run the engine.”
From the NTSB report, “Shortly after starting the no. 3 main engine for the inspection, a low lube oil pressure alarm and a low turbocharger oil pressure alarm activated. Crewmembers stopped the engine, inspected the lube oil system, and found pieces of plastic in the lube oil system relief valve. Technicians were notified and returned to the vessel. They identified the plastic as parts of a cigarette lighter.”
A cigarette lighter?! “The technicians drained the oil and searched the lube oil system for 2 days, recovering about 70% of the cigarette lighter’s plastic and metal components from the engine. After their debris removal efforts, the technicians advised WSF that it was acceptable to run the engine. None of the engines were run again until the vessel made departure preparations for a sea trial in April.”
The vessel then went on the sea trial, during which a catastrophic failure occurred, including an engine room fire, more from the NTSB report, “Engineers inspecting the affected engine room found a broken connecting rod, part of a piston, and an inspection cover laying on the deck outboard of the no. 3 engine. Inside the engine, part of the piston had fallen down and was resting on top of the crankshaft.” Essentially, a piston and connecting rod were blown out the engine’s side inspection cover.
The NTSB report attributed the failure to incorrectly torqued connecting rod bolts; the cigarette lighter was not mentioned in the root cause analysis, which, at least to me, seems somewhat peculiar.
I am no marine engineer and I can’t pass judgement on those who carried out the repairs, and failed to properly torque the connecting rod fasteners, any more than the NTSB has already done, however, that coupled with the lost lighter, is an indication of inattentiveness, likely caused by distraction.
Almost every day I’m in the field I see marine industry professionals distracted in their work by one thing, and I know this comes as no surprise to anyone, cell phones. Studies indicate smart phones account for about eight hours a week of lost productivity. While productivity is vital to any business that wishes to remain profitable, the potential for cell phone-driven distraction leading to physical losses, or catastrophe, is also very real, just look at the meteoric rise in “distracted driver” accidents.
Many of the tasks marine industry professionals perform carry with them the potential for disaster. A technician working on propulsion, raw water plumbing, steering, shift and throttle or electrical systems bears a heavy burden of responsibility, a moment of inattention or distraction can lead to a potentially dangerous or even deadly scenario, it has no doubt already occurred. I’ve seen captains piloting vessels while talking on their phones, and two clients have over the years confessed to me that they ran aground while talking on or looking at their phones. Who among us has not been distracted, sometimes dangerously, by our phones? What’s the solution? A client I’m working with now, one who operates a factory that includes thermal reactors, which run at 2,000 degrees, prohibits the use of cell phones during their employees’ shifts…
Folks, this is an epidemic of untold proportions. Where this issue is concerned, the marine industry, the nation for that matter, must self-reflect and endeavor to do better.
This month’s Marine Systems Excellence eMagazine feature covers the subject of primary fuel filters. I hope you find it both useful and interesting.
Selecting Primary Fuel Filters
There’s more to it than meets the eye
Racor Turbine Series filters offer users a host of advantageous features, and in the tandem arrangement like the one shown here, this includes built-in redundancy.
There’s a nautical truism, ‘It isn’t a matter of if you will run aground, but when’. Similarly, it’s the rare vessel operator or marine industry professional who hasn’t encountered a clogged primary diesel fuel filter. It’s a veritable fact of life if you run or work around diesel engines. However, it doesn’t necessarily have to be an especially unpleasant, or potentially dangerous experience. Losing power while transiting a rough, narrow inlet, or in heavy seas, both of which are exactly the circumstances that often result in agitated fuel within tanks, and thus filter clogging, can lead to the loss of the vessel, and the crew. If you show some care and forethought in the selection process, however, you might make such events more of an inconvenience than a catastrophe.
Because some engine manufacturers describe them as otherwise, a definition is in order; “primary” refers to the first filter the fuel encounters on its way to the engine, while “secondary” is, intuitively, the second filter the fuel encounters, which is sometimes referred to as the “on engine” filter. Traditionally, the primary filter is supplied and installed by the boat builder, while the secondary filter is on, and part of, the engine. Some marine engine manufacturers, John Deere among them, provide two “on engine” filters, one of which is specifically designed for water removal, with an included alarm, affording the operator of such engines triple filtration protection.
The dirt and water holding capacity of Turbine filters carries with it near legendary status. The engines served by the filters shown here continued to operate without issue.
More is Better
When it comes to fuel filtration, there’s no such thing as too much. I’m often taken to task by boat builders for suggesting to buyers that a larger primary filter be installed. “It’s overkill and a waste of money”, “it costs too much”, or “it takes up too much space” they exclaim. Perhaps, however, there’s a method to the madness. Larger filters are clearly capable of capturing and safely holding more water and debris, the very job with which such filters are tasked. However, equally as important, larger filters, like the Racor MA Turbine (the name is derived from the rotational motion they induce in fuel that passes through them, which in turn, along with the ‘coalescer cone’ induces centrifugal removal of water and dirt) series for instance, are infinitely easier to inspect, when equipped with clear bowls, more on that below, and service when compared to smaller filters that may be technically correct for a given engine or genset. Small, spin-on or sandwich-type filters are cumbersome and messy to replace and inspect, especially in a seaway, they are more prone to air ingestion, they retain less contaminants, and their replacement elements are often more difficult to obtain; most can’t be inspected for water or debris and meet ABYC flame resistance requirements. All of these obstacles make it less likely that a boat owner will be willing, or able, to tackle this sort of challenge.
Furthermore, and unlike larger aforementioned Turbine series filters, in order for them to meet the UL Marine/ABYC requirements for flame resistance, these smaller filters cannot include a clear plastic bowl; it must instead be metal, which means it can’t be monitored for water or accumulation of debris.
Smaller, non-turbine series filters may meet the fuel flow needs of generators and smaller propulsion engines, however, they are cumbersome to service, and in order to meet flame resistance standards they must forfeit their clear sight bowls, robbing them of one of their most valuable features.
Turbine MA series filters, and others like them, embody a series of extremely valuable yet often overlooked traits that include a large, clear bowl, a T handle that makes for easy, tool-free replacement, provisions for a water in fuel indicator – a must in my view – full ABYC and UL Marine compliance for fire resistance, O ring fittings that are virtually guaranteed to be leak free, and readily available replacement elements in the appropriate primary ratings of 10 and 30 microns.
The spot-face O ring seals used in Racor Turbine filters are virtually leak-proof.
Details
Far too few primary fuel filter installations take advantage of a small, relatively inexpensive yet invaluable component, a vacuum gauge. Without it, you have no way of knowing how much contamination has accumulated within the filter, and therefore no accurate means of knowing when it should be replaced. If a filter element shows no vacuum restriction, there’s no need to replace it; a vacuum gauge also serves as a useful troubleshooting tool. Additionally, a vacuum gauge can serve as a very handy troubleshooting tool, if an engine is running erratically, or lacks power, the vacuum gauge will almost certainly simplify the troubleshooting task. For more on vacuum gauges see this article.
Without a vacuum gauge, you are flying blind… short of an engine shut-down, they are the only means by which filter condition can be determined. Running without one is tantamount to operating an engine with no coolant temperature, or oil pressure, gauges.
Replacement elements are readily available for Racor Turbine Series filters, in 2, 10 and 30 microns. For primary filtration, only 10- and 30-micron elements should be used, 2 micron elements designed strictly for secondary filtration applications. I realize that flies in the face of some strong, bordering on religious, opinions on the subject, however, this requirements comes straight from Racor, and most engine manufacturers. Follow the guidance from yours as to which micron element, 10 or 30, should be used. Typically, and in the absence of a clear directive, common rail engines call for 10 microns, while others can use 30 micron elements. When priming Turbine series filters, be sure to do so only with a new filter element installed; ensuring that fuel that leaves it is free of dirt and particulates.
Few attributes of a fuel filter trump ease of service. When priming primary fuel filters of the sort shown here, be sure to do so only with the new filter element installed, thereby ensuring all fuel that leaves the filter body has passed through the element.
Not all primary fuel filters meet ABYC/UL Marine fire resistance requirements. In order to comply with this standard, filters and other fuel-carrying components must be capable of withstanding two and a half minutes of exposure to flame without failing or leaking. Filters with plastic bowls and no heat shield nearly always lack compliance. Many boat builders, yards and DIY installers unknowingly install non-complaint filters, not realizing that they lack flame resistance compliance. Compliant Racor Turbine MA series filters incorporate two critical features; a heat shield for the bowl, and a metallic rather than plastic drain plug, the latter would melt when exposed to flame. Tellingly, the label on the marine-rated Racor Turbine MA series filters is blue; while Racor Turbine filters that lack flame resistance utilize labels with red or black lettering.
The blue font label on a MA Series Turbine filter denotes its compliance with ABYC and UL flame resistance standards.
For non-inspected vessels, i.e., non-commercial, non-paying passenger carrying, non-compliant filters, those that lack heat shields and metallic drain plugs, can be retrofitted with these parts for a fraction of the price of a complete new, compliant filter assembly.
The lack of a heat shield and the candy-apple-colored label text belie this Racor Turbine Series primary filter’s industrial, rather than marine origins.
For all other vessels, i.e., those that are required to meet USCG standards, non-flame-resistant filters must be replaced in their entirety. I once asked a Coast Guard Marine Safety Officer why this was, his answer was telling, “Because if the vessels burns; we need to be able to retrieve the remnants of the filter house, and then determine from its serial number (they are serialized) if it was a MA or other filter.
It’s worth noting, CE Certification, ABS (American Bureau of Shipping) classification society rules require the otherwise clear sight bowl used on a Racor MA Series Turbine filter to be metallic, and thus opaque. In my opinion this is counterproductive, as an unseen accumulation of water or debris in a filter is very likely to lead to unanticipated engine stoppage, which in turn could lead to the aforementioned catastrophic scenario. If the clear sight bowl with heat shield is good enough for the US Coast Guard, and Racor, I trust it, and would not be without its ability to alert a user to impending trouble long before it can affect engine operation.
While many primary filters include provisions for drain valves, few include them out of the box, they must be added, and the Racor MA series is no exception. When doing so, be sure to select, once again, only valves that meet UL Marine and/or ABYC standards. These are characterized by a lack of springs to maintain tension within the valve and fuel-tight integrity, rotation that is no more and no less than 90°, and of course flame resistance, making plastic valves unacceptable.
A UL Listed Marine drain valve must embody two features, a valve barrel whose fuel-tight seal does not rely on spring tension, and a handle that rotates through no more and no less than 90 degrees.
An added advantage of the metallic valves is they are less restrictive, and thus are less prone to clogging, and should they clog, their strait through design enables them to be easily cleared with a small screw driver, wire or similar narrow object. Compliant valves will be marked ‘UL Marine’.
This drain lacks ABYC compliance for several reasons, it relies on a spring-tensioned seal (the spring is mild steel, which can rust and break), it turns through 360 degrees, and it lacks a pipe plug to prevent spills.
Finally, valve drains must be capped or plugged to prevent a fuel spill should the valve handle be inadvertently moved. If the filter is located below the fuel level, such an inadvertently opened valve could lead to hundreds or even thousands of gallons of fuel leaking into the bilge. I once observed such a scenario, on a vessel undergoing repairs; the bilge filled with about 100 gallons of fuel. Fatefully, it was hauled at the time (and stored inside a shed), and the bilge pump had been disabled. The culprit, a technician leaving the vessel at the end of the work day bumped the valve lever with his foot, unknowingly causing it to open.
Plastic drain valves not only lack flame resistance, thanks to their smaller, and 90 degree, orifices they are more easily clogged.
The final accessory worth adding to a primary fuel filter is a water in fuel, or WIF, sensor. Such sensors enable an operator to receive a remote signal, from a dashboard annunciator, or via the vessel’s monitoring network, to the presence of water in the fuel, long before it can reach a critical level within the fuel bowl.
The value of a high quality, efficient and easily serviced primary fuel filter cannot be over-stated, it’s well worth the investment.