Feature: Life Raft Installations – Editorial: Brokers and Commissions
Text and photos © 2020 Steve D’Antonio Marine Consulting, Inc.
From the Masthead
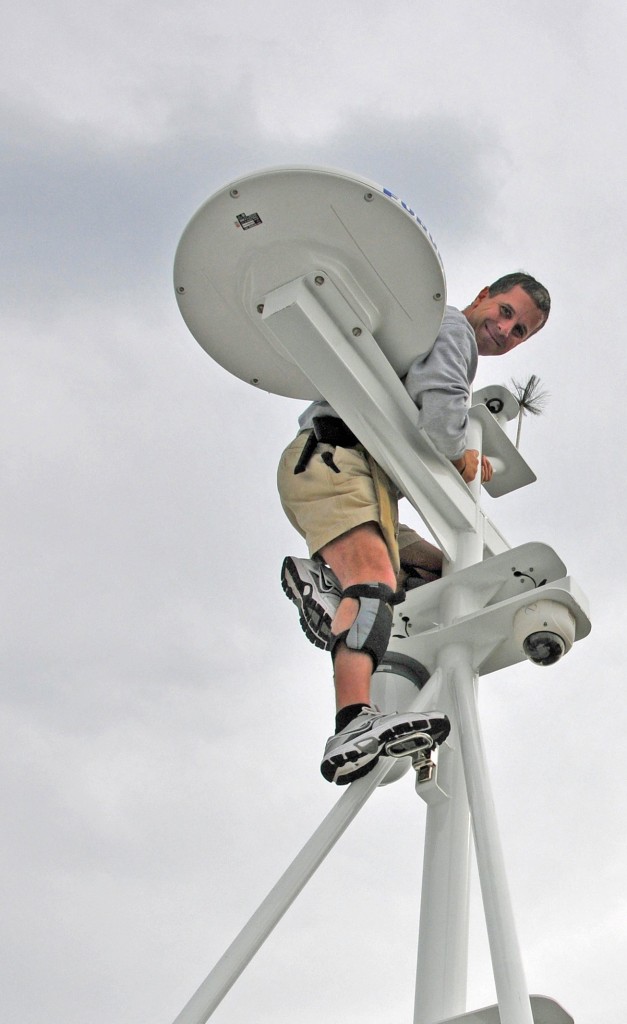
Commissioned Advice
I’ve worked with the same investment advisor for almost 20 years. His compensation is commission-based, so for every sale and purchase I request, or that he recommends, he profits. I know my advisor very well, and I trust him implicitly; the root of that trust lies in the results of his work, he has successfully grown and safeguarded my portfolio.
I’ve been a long-time advocate of incentivized, commission sales, when I ran a boat yard the bulk of my pay was commission-based, it was predicated on both overall yard efficiency, and on the amount of work I sold, while factoring in warranty. I was directly rewarded for my efforts, efficiency and for the competency and thoroughness of my oversight (if I failed to properly supervise the work, or if I failed to remain current on the latest techniques and standards, efficiency fell, warranty costs would rise, and my compensation shrunk).
The danger, of course, in such a commission-based system, as anyone who has worked with an unscrupulous stock broker, or car salesman knows, is the temptation on his or her part to drive-up short-term commissions by recommending sales or purchases, regardless of their efficacy. As a boat yard manager, I could have taken the same, albeit dishonest, tack, recommending work that was not necessary, or by recommending more costly options. In both cases, mine and the unscrupulous stock broker/salesman, the success would be short-lived, as most boat owners (and investors/car buyers) will eventually figure out when they are being taken for the proverbial ride, some more quickly than others.
In my experience, most marine industry professionals are by and large (a term with nautical roots by the way) honest and well-meaning, they want to please their customers, and they want them to return. There are, however, bad apples in every bunch. You should, therefore, remain on guard during early interactions with boat yards, contractors and brokers; while you are still “dating” so to speak. The actions of those individuals who stand to make money, based on your decisions, should be scrutinized carefully.
If, for instance, a contractor recommends replacing batteries based on their age rather than test results, or purchasing a new water pump rather than rebuilding the old one, you should seek to understand how he or she arrived at that recommendation, is there evidence the batteries are under-performing, is the water pump not rebuildable, or is rebuilding it more costly than replacement? The answers to these questions will tell you a great deal about the competency, or honesty, of those with whom you have chosen to work. If the answers you get don’t make sense, or if those being asked are clearly made uncomfortable by the question, it’s almost certainly cause for concern; trust your instincts.
In the case of boat brokers, if your buyer’s broker is repeatedly showing you boats that aren’t right for you, he or she may be simply chasing the commission, without serving your needs; it may be time to find another broker. If you are a boat buyer, remember, selling brokers work for sellers, and should have sellers’ best interests at heart, including securing the highest selling price possible, on which their commission is based. It’s reasonable, honest and to be expected, and you won’t be disappointed as long as you keep this in mind. You can learn more about working with the marine industry here.
This month’s Marine Systems Excellence eMagazine feature covers the subject of life raft installation. I hope you find it both interesting and useful.
Upcoming SDMC Webinar
Identifying the Most Common New and Used Vessel Construction and Systems Flaws Part II
New builds, repairs and refits provide ample opportunity to do things right, and to follow both ABYC and equipment-manufacturer guidelines and instructions. In many cases, however, that’s not the way it goes.
In this photo-intensive presentation marine industry consultant, and ABYC Master Technician Steve D’Antonio, will share with attendees examples of errors he’s encountered over the course of hundreds of new and used vessel inspections, including exhaust, LP gas, potable water, sanitation and fuel systems, with the goal of learning from the mistakes of others. This will not simply be a case of sharing horror stories and photos, each example will identify the flaw, as well as the fix and how the problem could have been avoided.
- When: Monday, July 20, 2020 – 1:00 PM to 3:00 PM EST (approximately 90 minutes for the lecture, and 30 minutes of Q&A)
- Delivery: Zoom Video Conferencing
- Fee: $95.00
For more information and to register, please follow this link.
Life Raft Installations
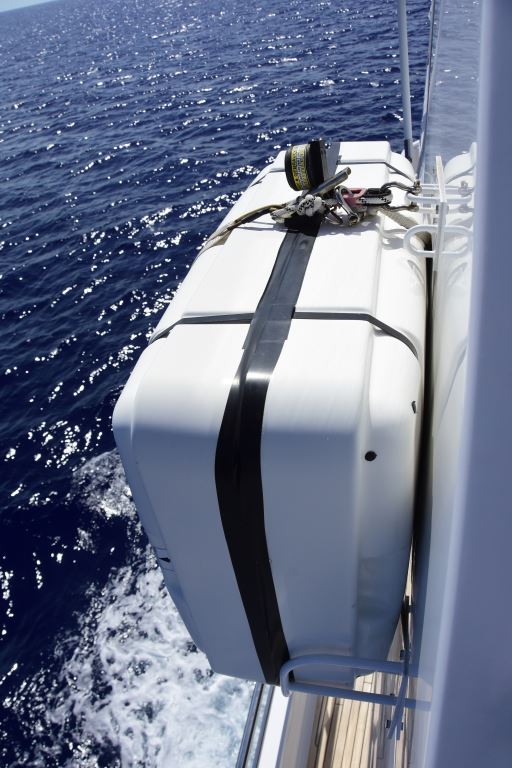
I have a theory as to why so many life rafts are poorly or improperly installed and maintained; they are, thankfully, rarely needed and thus rarely tested. Like seat belts and insurance policies, while you hope you never have to count on them, you of course want them to work with full effectiveness, should the need arise.
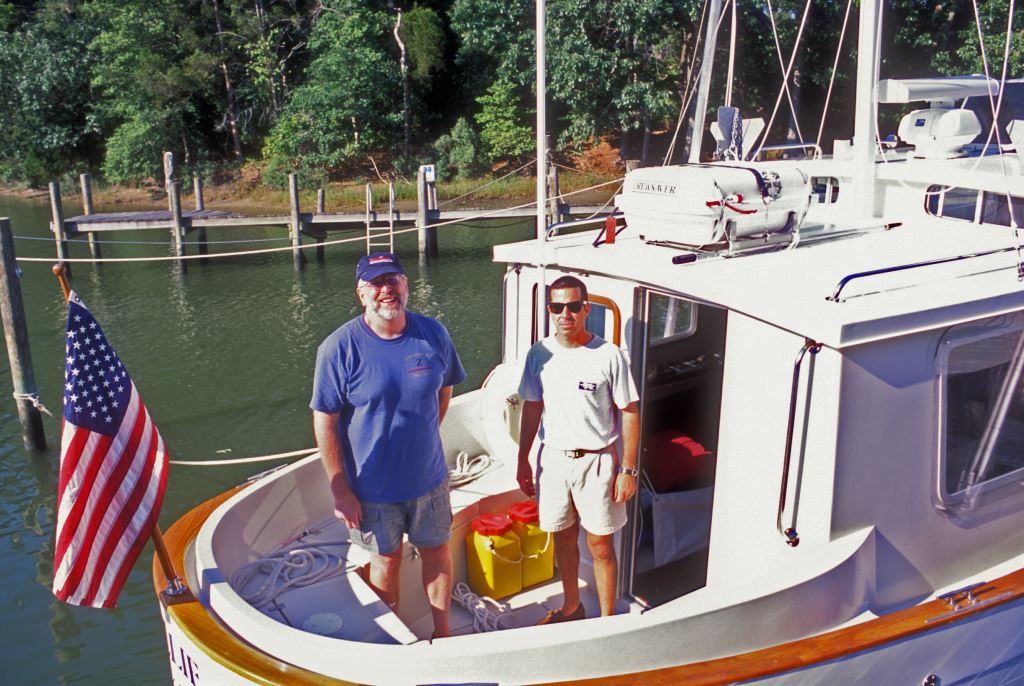
The scope of this discussion is limited to weather deck-installed, canister life rafts, since the valise style present far fewer options, and far less opportunity for errors. Provided they are routinely serviced, and kept dry, if you can drag them on deck, secure the painter, and if you can manually deploy them (by no means given), they are likely to work.
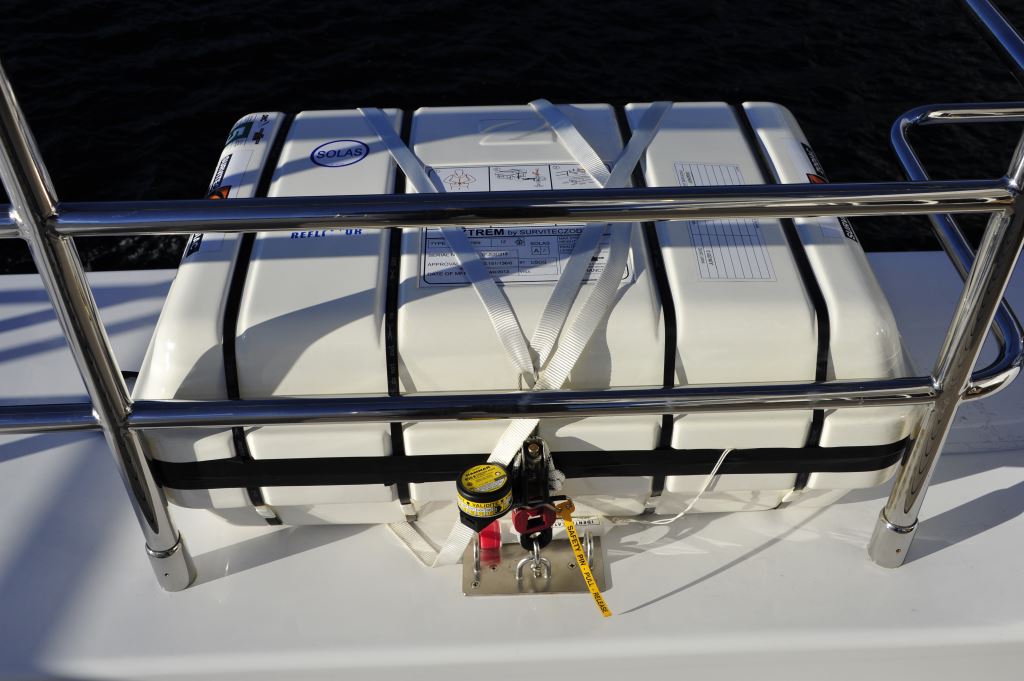
Location
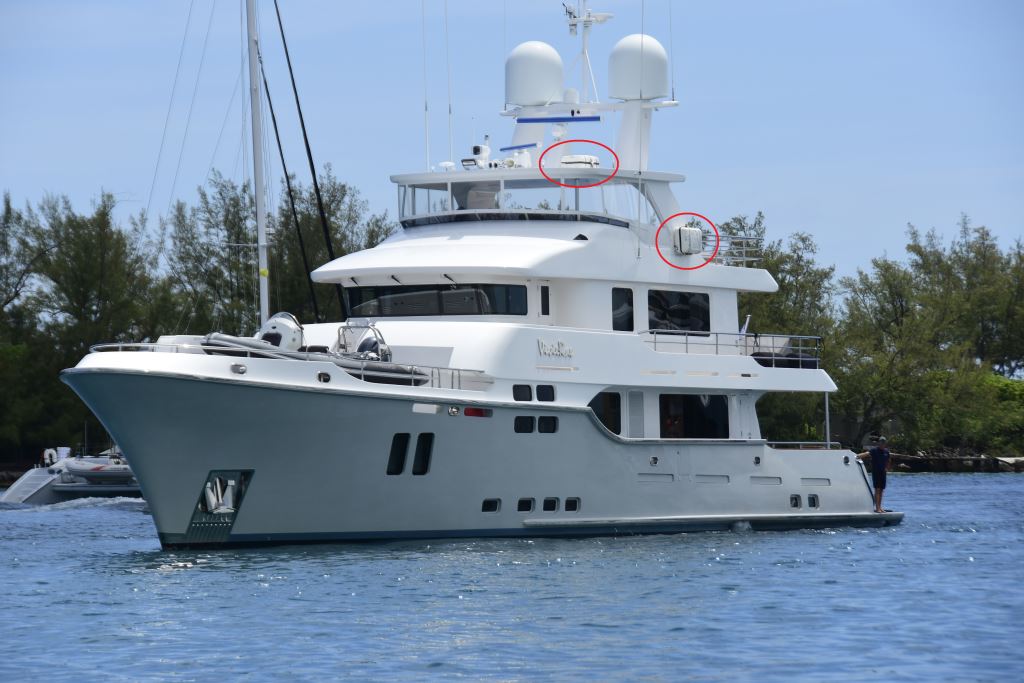
Careful consideration must be given to selecting a canister raft and cradle installation location, taking into account several requirements, including manual, and automatic/hydrostatic deployment, as well as deployment in the event of fire, along with the most efficient use of on deck real estate, which is invariably in short supply aboard most small craft.
For rafts equipped with hydrostatic release units, or HRU’s (more on those in a moment), it’s important to avoid locations where the raft may be struck by boarding seas, the fore deck of a sailing vessel for instance, the pressure of which could trigger the release of the raft. Even where a HRU is not used, the locations exposed to heavy spray and green water are more likely to result water penetration into the canister, damaging the raft stored within.
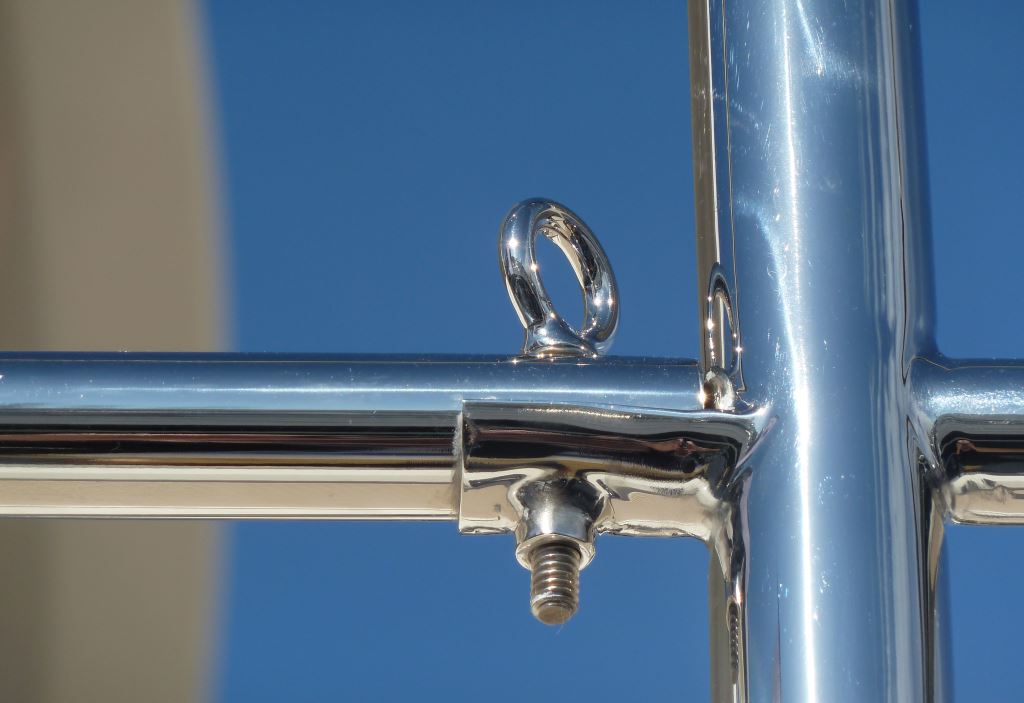
Two of the criteria that must be considered are hydrostatic, and manual, deployment. For the former, the raft should have a clear, unencumbered view of the sky, enabling it to rise from a sinking vessel (assuming it sinks on a relatively even keel); it should not be located under overhangs, canvas, or hard tops where it might become trapped when released and floating upward from its cradle. For manual release scenarios, it should be possible for one person to push the raft canister overboard. A six person, containerized offshore raft could weigh close to 100 pounds, and as such it’s unlikely to be carried even the most physically fit crew member, especially while the vessel is at sea, and thus one should be able to slide or tip it overboard. If it’s mounted inboard of a life rail, for instance, make certain it can be slid under the rail. If this isn’t possible, it may be necessary to make a section of the life rail or line easily removable.
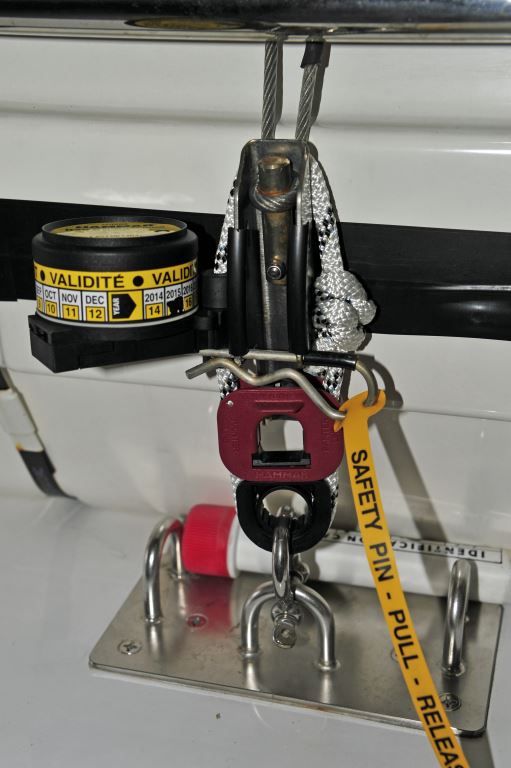
Rafts mounted outboard of, or integrated into, rails, or those mounted outside the envelope of the vessel, have the advantage of being more easily released, however, they are also more exposed to heavy weather conditions, and in my experience vertically mounted canisters are more likely to suffer water leaks via the seam in the canister halves, and from drain holes. No raft, when mounted, should stand proud of the vessel’s rub rail, or else it may be damaged by a bulkhead or piling. This scenario can be avoided by designing the life rail with a recess to accommodate the canister, keeping it inboard of the maximum beam/rub rail.
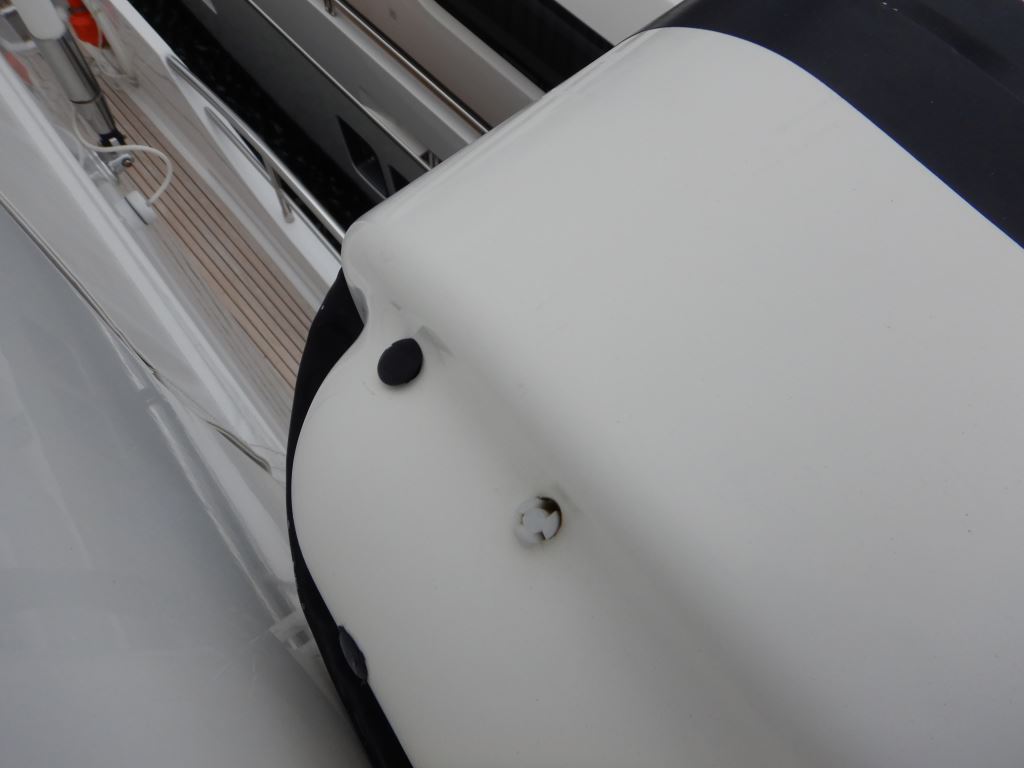
The top of a motor yacht, or trawler’s, cabin or fly bridge, hard top present yet another installation location possibility. It’s out of the way, not likely to be tripped over, it doesn’t take up valuable deck real estate, and it’s protected from boarding seas and spray. The high perch also makes it less likely to be stolen. Drawbacks to this location include difficulty in accessing it in heavy weather, and for service/inspection, or in the event of a fire, where smoke, heat and flames are rising. Never the less, when all options are considered, hard tops often represent the lesser of all evils.
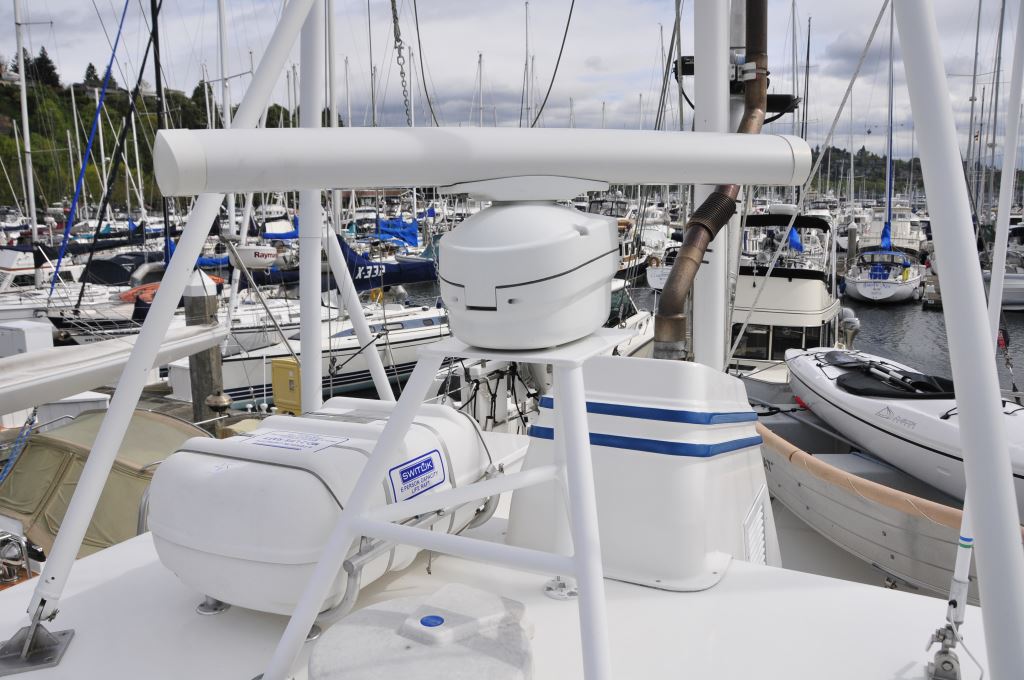
One should cast an especially critical eye on custom-made, sandwich type rail mounts, where the raft is cradled vertically within a hinged life rail lattice work, which in turn is designed to open when triggered manually or hydrostatically. I have encountered a few of these designs where the geometry of the hinge, or the means of engagement of the release, hinder smooth and unencumbered release of the canister. Also, give consideration to how such a support and release mechanism will work if the vessel heels in the direction of the raft, causing it to face the sea surface.
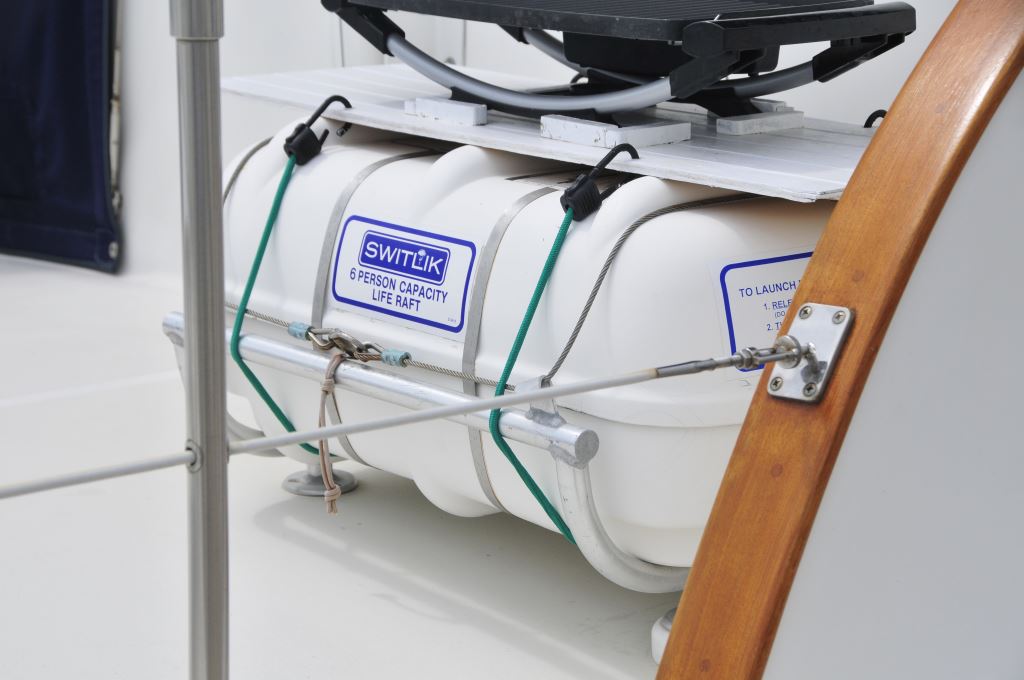
The canisters of many rafts are equipped with drain holes in the “floor”, which when installed horizontally, allows any water that does enter the raft canister to drain quickly. However, if the raft is installed vertically, then some of these drains that would normally be on the bottom of the canister, now become effective water entry points. Water entering a raft canister can lead to raft deterioration and a malfunction when deployed.
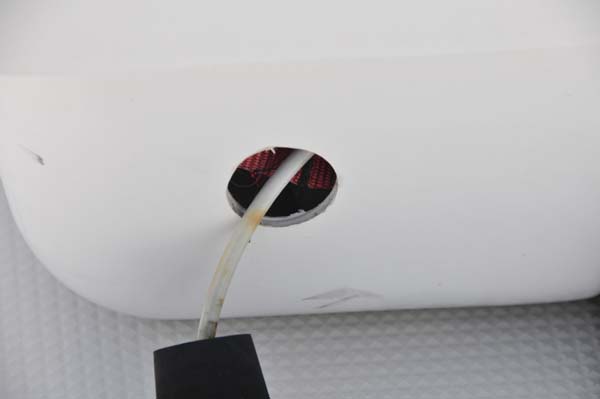
When a raft is ordered from the dealer, with a vertical mount, the dealer should plug upward-facing holes by default. However, in my experience, based on the number of canisters I encounter whose holes are not plugged, this should never be assumed; vertically-mounted rafts should be closely inspected for this potential problem.
Installation
The most common cradle installation flaws involve the fastening method. Because these rafts are exposed to the elements, and potentially boarding seas, their cradles must be securely fastened to the deck or surface on which they rest, otherwise they may come adrift, or be swept away all together.
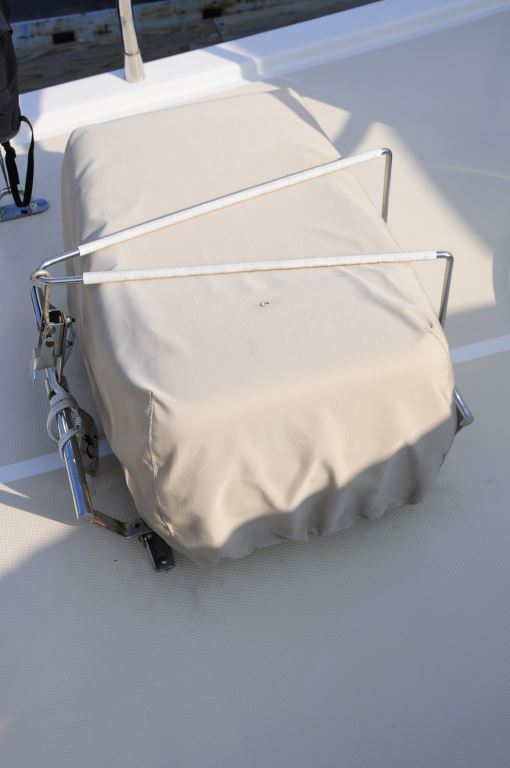
The preferred fasteners are stainless steel, through-bolted machine screws. Such a fastening method requires access to the opposite side of the mounting surface, which might be a saloon, stateroom, cockpit or other hardtop overhead. Headliner removal may be required, and for weather deck areas access ports may need to be installed.
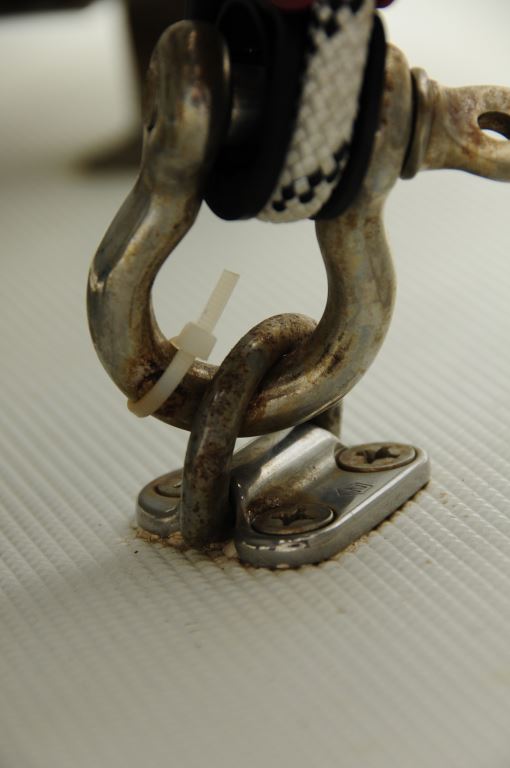
When installed through cored composite structures, the core must be reefed out and back filled (for more on that process see this article) with thickened epoxy at each penetration, and nuts should be amply backed with thick (not easily distorted) washers, and/or backing blocks. The inside of the backing plate/block and nut/washers should not be bedded, doing so will only serve to trap water in the penetration, against the fastener shank, where it will insidiously promote crevice corrosion.
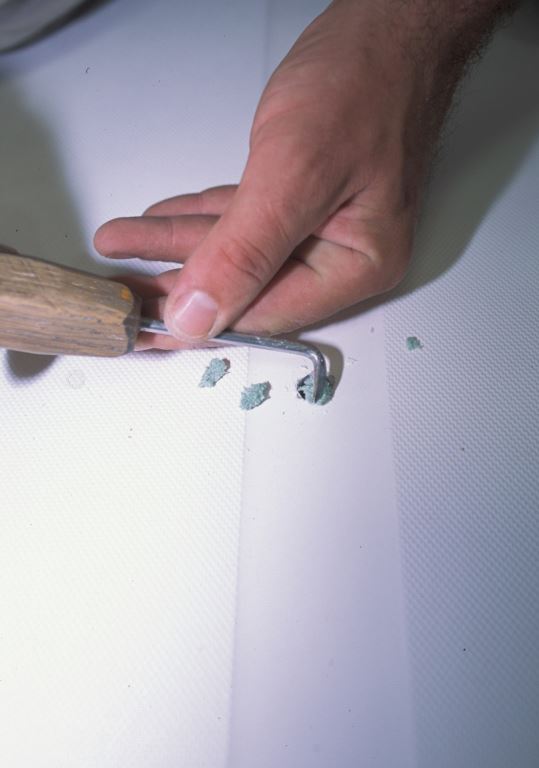
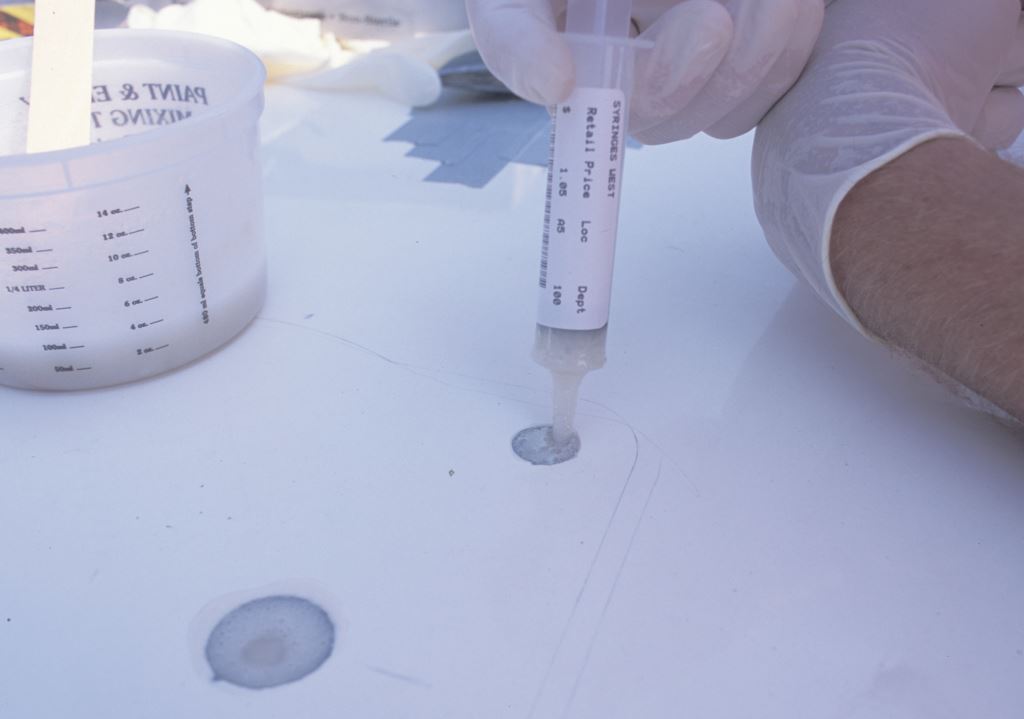
In many instances, the daunting nature of such though bolt requirements dissuade both boat owner and industry professional alike; leading them to the utilization of tapping or lag screws. Under no circumstances should something as critical as the installation of lifesaving equipment be entrusted to tapping screws, especially in the case of a cored fiberglass substrate. Not only does this make for woefully inadequate security for any piece of gear, it virtually guarantees the admission of water into the core, carrying with it all its unpleasant and expensive consequences.
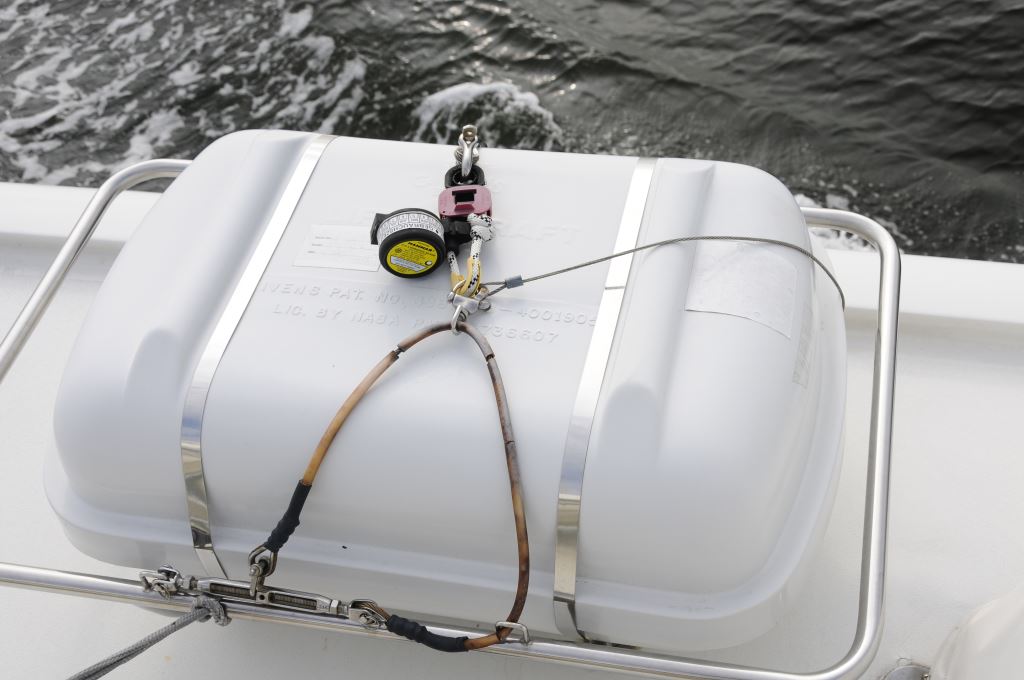
Once installed, make certain the raft’s painter is properly secured to either the HRU’s ‘weak link’, more on that below, or to a hard point such as the cradle or a pad eye. Considerable upward force could be applied to this hard point, so make certain it is secure, a pad eye fastened with tapping screws, or a non-welded life rail would represent poor attachment location choices. This connection, and its security, is critical, if it fails to be completed, the raft may drop out of, or float free from its cradle, but unless the painter is deployed, it will not inflate. Once the raft is installed route the painter so it includes a drip loop, rather than a ‘down spout’, as it enters the canister, thereby assisting in the exclusion of water.
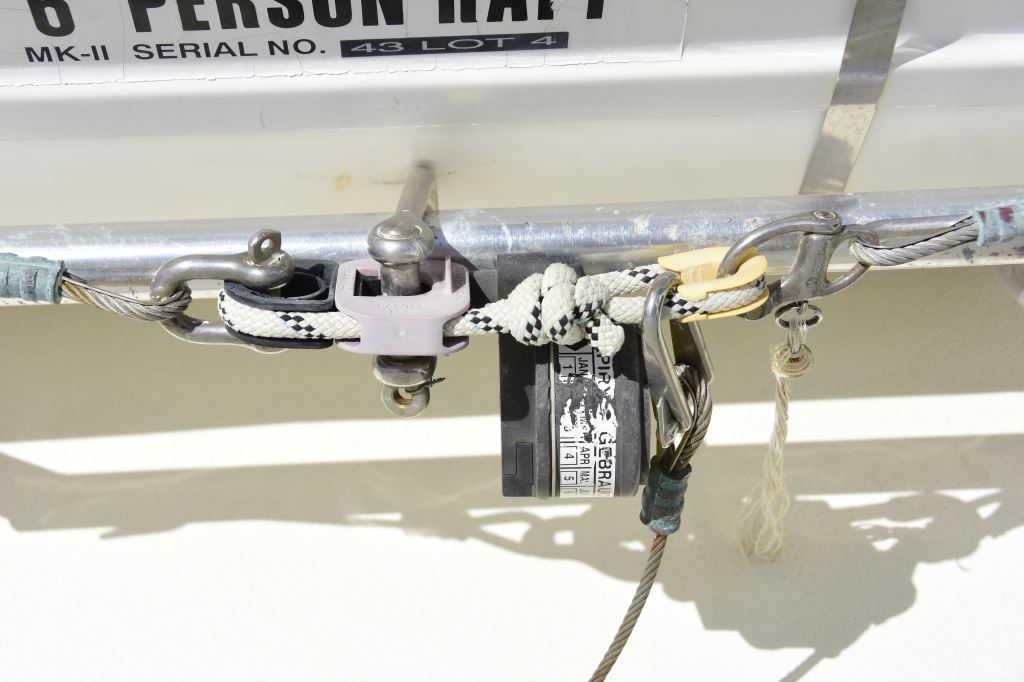
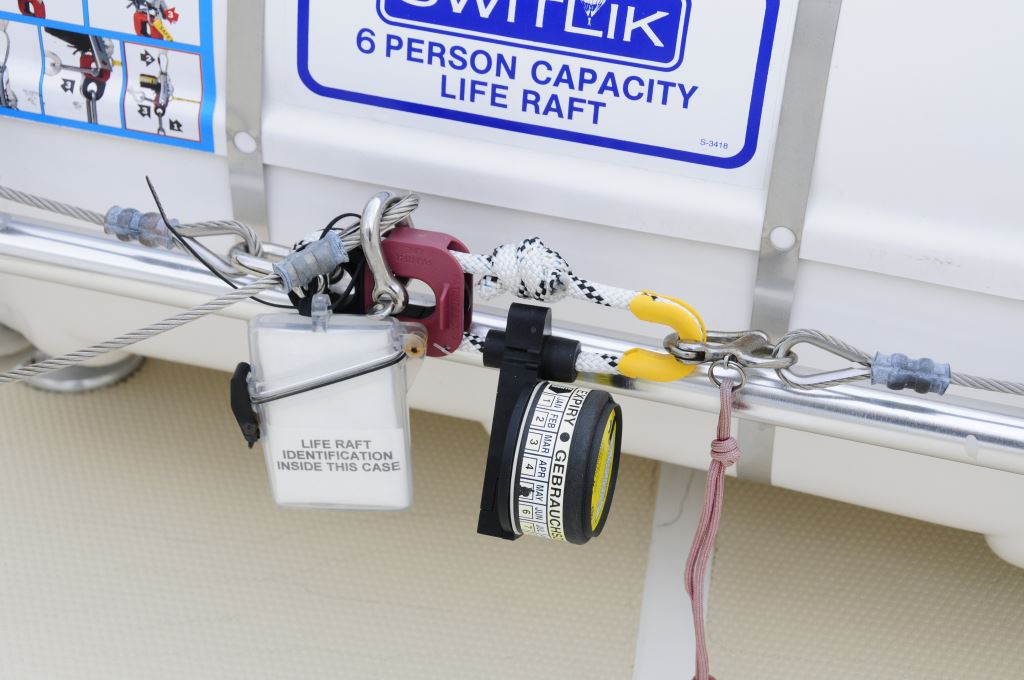
Hydrostatic and Manual Release
The familiar yellow (or less common green) label HRU, made by Hammar AB, of Göteborg, Sweden, utilizes a pressure sensitive diaphragm, and spring-loaded stainless-steel knife, housed within a glass fiber reinforced Nylon cover, along with a ‘weak link’ feature. The Hammar “H20” HRU is designed to be triggered by water pressure encountered at a depth of between four feet and twelve feet (1.5m and 4m) for the yellow, and 12 feet (4m) for green label models, at which point the spring-loaded knife is released, cutting what Hammar calls the red and white “strong rope”, which in turn releases the raft to float free and upward. As the raft floats to the surface, its painter line pays out, these are usually between 30 feet to 50 feet (10m-12m) long. This line should be secured to the hydrostatic release’s red ‘weak link’, which is labeled “painter”. When the raft’s painter is fully deployed, it triggers the rafts inflation mechanism. As the vessel continues to sink, the buoyancy of the raft creates enough tension to cause the weak link to shatter, releasing the raft.
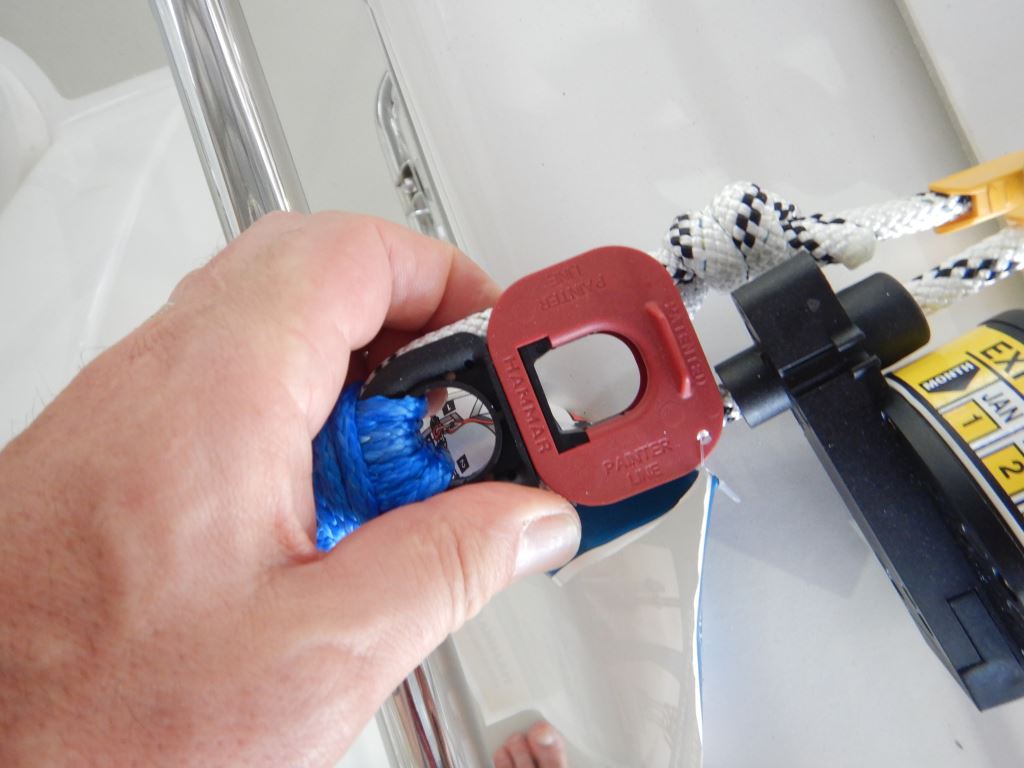
While some raft painter lines include a weak link of their own, if the raft’s painter is lashed to something other than the hydrostatic release’s weak link eye, the raft cradle for instance, it’s possible the raft could be damaged before the painter parts. Hammar “H20” weak links are designed to shatter, releasing the raft at about 500 lbs. (2.2 kN) of upward lift for the yellow label, and 270 lbs. (1.2 kN) for the green label, model. Smaller rafts, those under four-person size, with consequently less buoyancy, should use the green label unit.
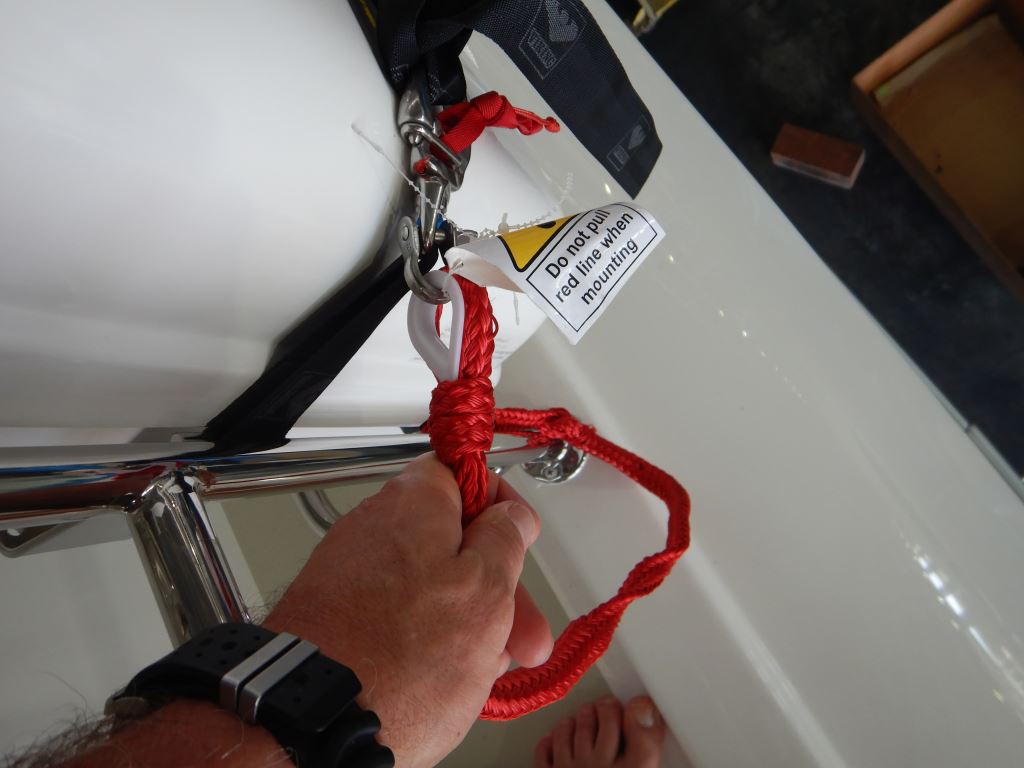
Hammar hydrostatic release mechanisms are designed to be replaced every two years. When installed, the date decal should be scratched (not simply marked with a felt pen) away to indicate the expiration date, two years from the date it was placed in service.
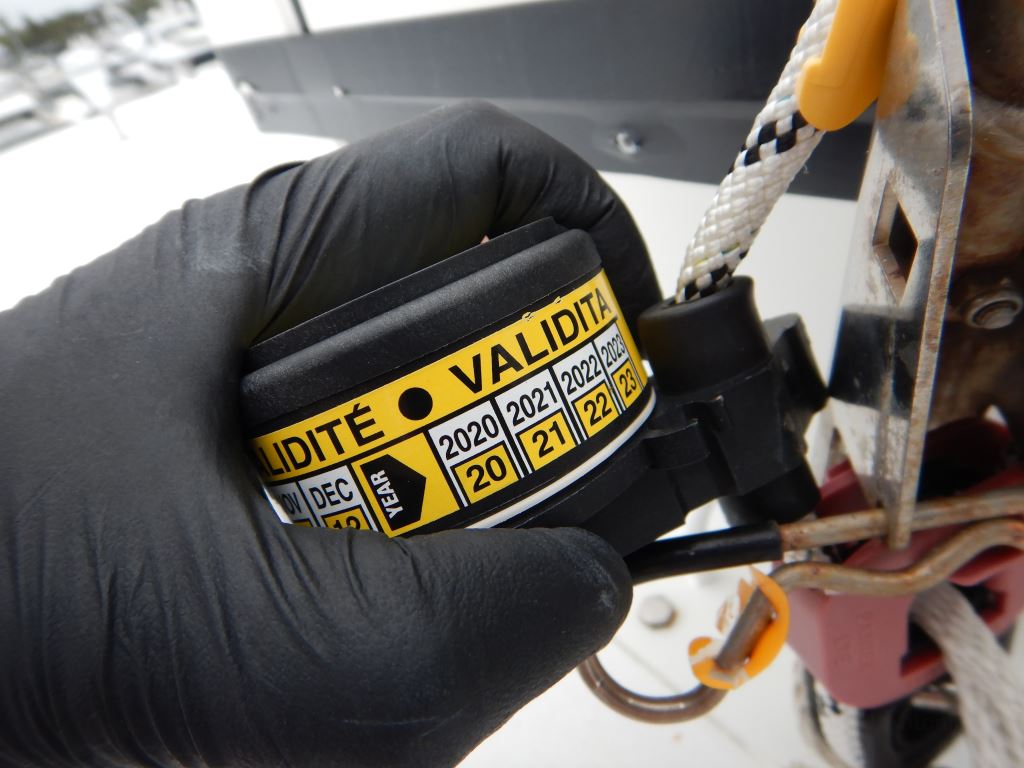
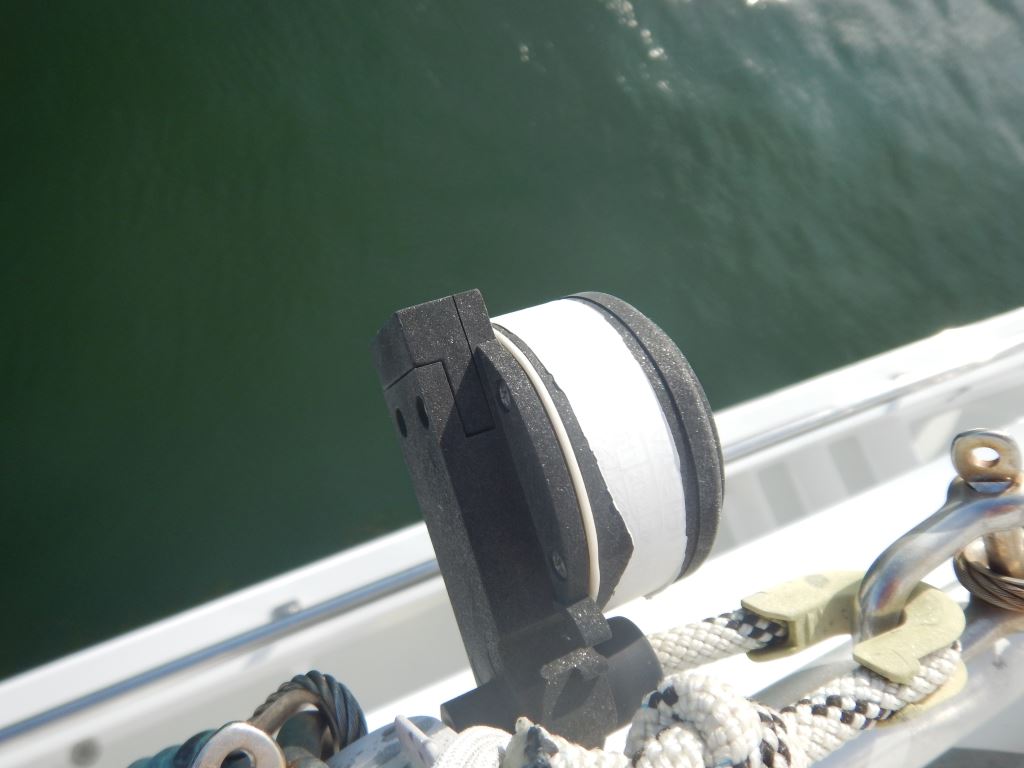
Beware, counterfeit hydrostatic release mechanisms have made their way into the supply chain. To the untrained eye, the fake units look almost identical to genuine Hammar H20 release units. Every Hammar release has its own unique serial number, which can be verified by contacting Hammar directly. Additionally, the underside of a genuine Hammar H20 unit includes five fabrication marks on all units produced since April 2006. The fabrication mark on the upper side of the unit should point directly towards the rope. If you are having your raft serviced, and the Hammar H20 hydrostatic release is being replaced, ask the dealer to give you the box the unit was shipped in, along with the enclosed instructions; reports indicate counterfeit units are not shipped in Hammar-labeled boxes and they do not include instructions.
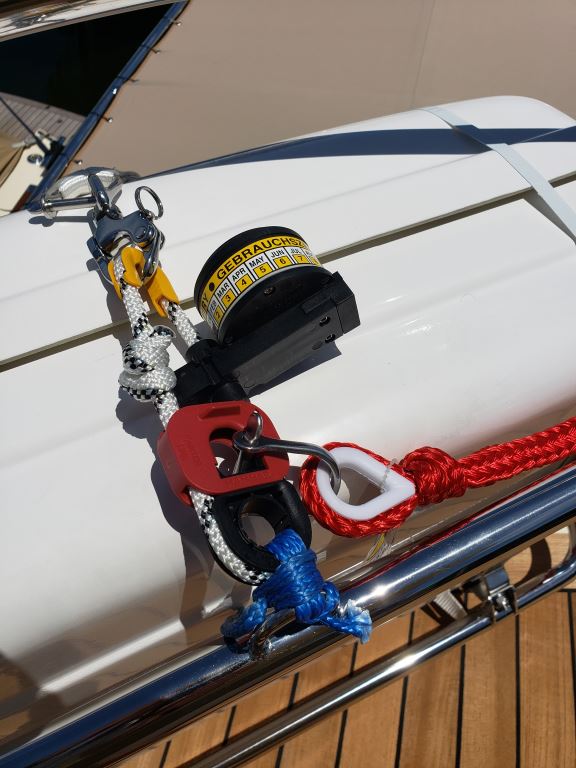
Every raft should have a means of being easily released manually, whether or not it’s equipped with HRU. This can take the form of a common ‘snap shackle’, or a proprietary release mechanism such as Hammar’s “Easy Release”, which uses a simple fulcrum design, or a senhouse slip or pelican hook (these are available generically as well as from Hammar). Most raft manufactures who offer canister cradles include straps with built in release mechanisms. Chief among the requirements for manual release mechanisms are absolute reliability, the mechanism must be trouble free after years of inactivity and exposure to the elements, and simplicity, one should be able to activate it single handedly, in the dark, even if the vessel isn’t on an even keel; it must not become jammed by tension. The release actuation mechanism should be equipped with a lanyard that is either clearly labeled or at least color coded red or yellow, to distinguish it from other lashings, or raft security mechanisms.
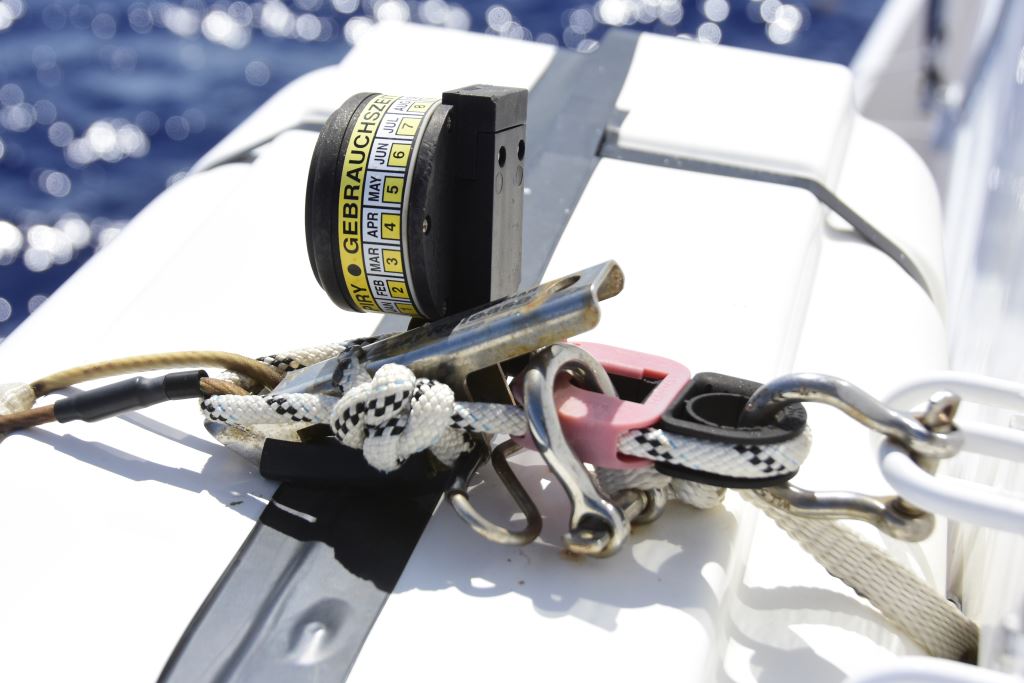
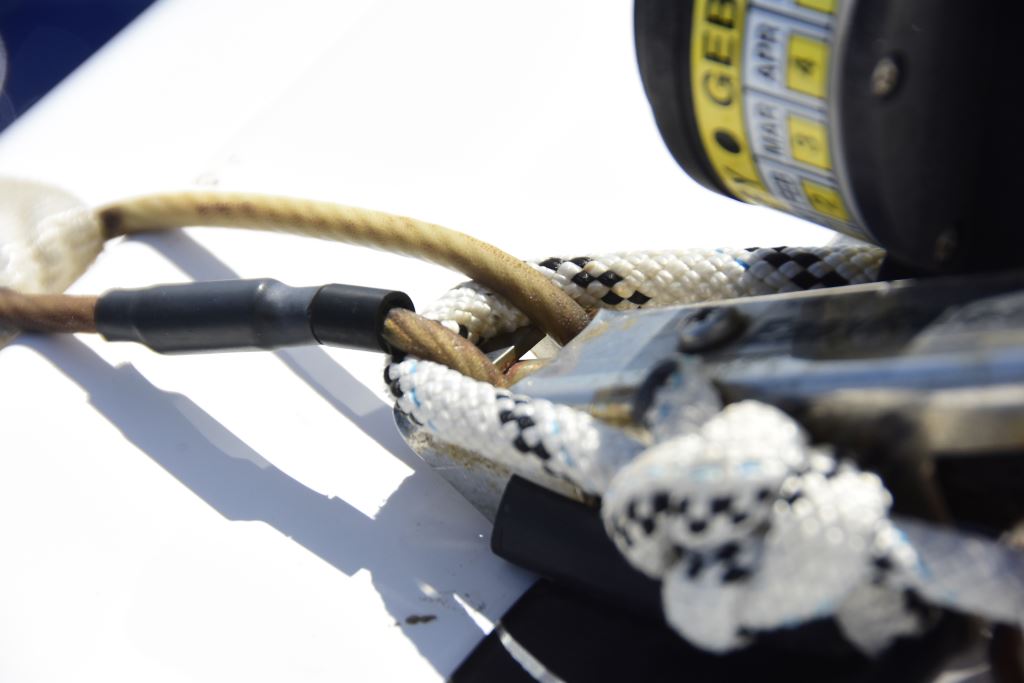
HRU’s are not mandatory for recreational craft, and thus it’s natural to wonder whether or not one is really needed. If it were my vessel, I would not dream of installing an on deck, canister type raft without a hydrostatic release mechanism. The only exception to this rule might be in the case of a small vessel where there is risk of a boarding sea triggering the release. Even in that case, the green Hammar hydrostatic release, which will not trigger until the raft sinks to a full 12 feet (4m), could be used to prevent such accidental deployment.
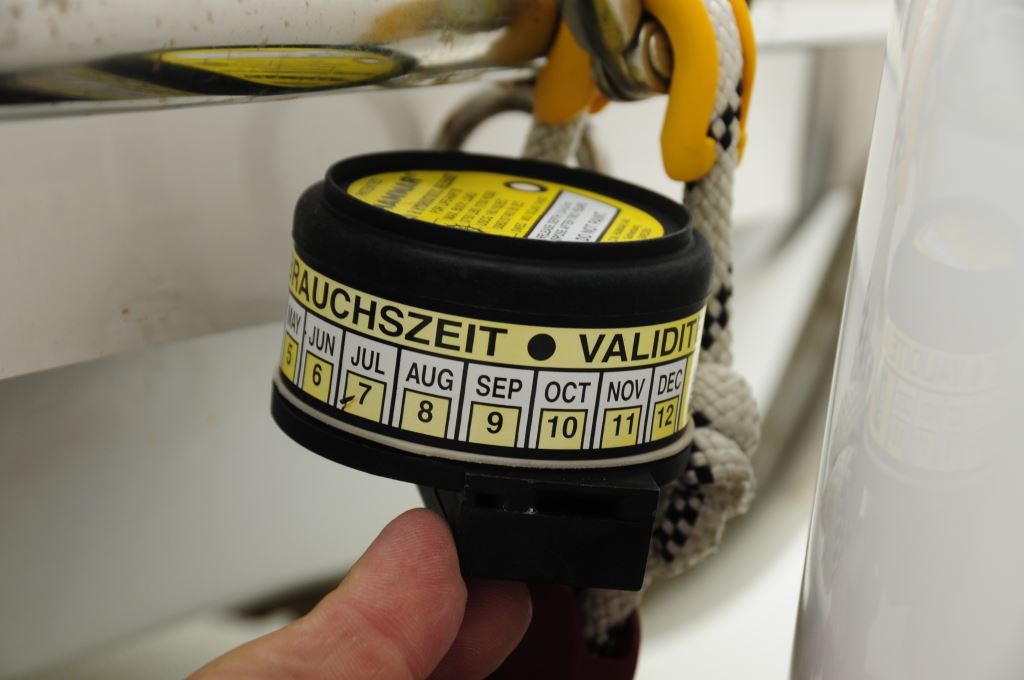
A Tale of Two Straps
On a recent new vessel inspection, I noticed that the life raft canister, which was supported in a vertical mount, was retained by a lashing that was connected to a hydrostatic release mechanism. I looked it over carefully to ensure it was properly routed, and in doing so noticed a puzzling detail, the raft was also retained by a separate lashing, of a different color, that was equipped with a manual release. It seems the builder ordered a raft with a hydrostatic release, and the raft dealer shipped the builder a cradle with a manual lashing, and the hydrostatic release, while neglecting to remove the manual release lashing. Therefore, if the user tried to deploy the raft manually, it would not have dropped out of the cradle unless both lashings were released, and the release on the manual lashing was not immediately obvious; in the dark or under stress, which is to be expected if one is faced with the need to deploy a liferaft, raft deployment must be quick, easy and intuitive.
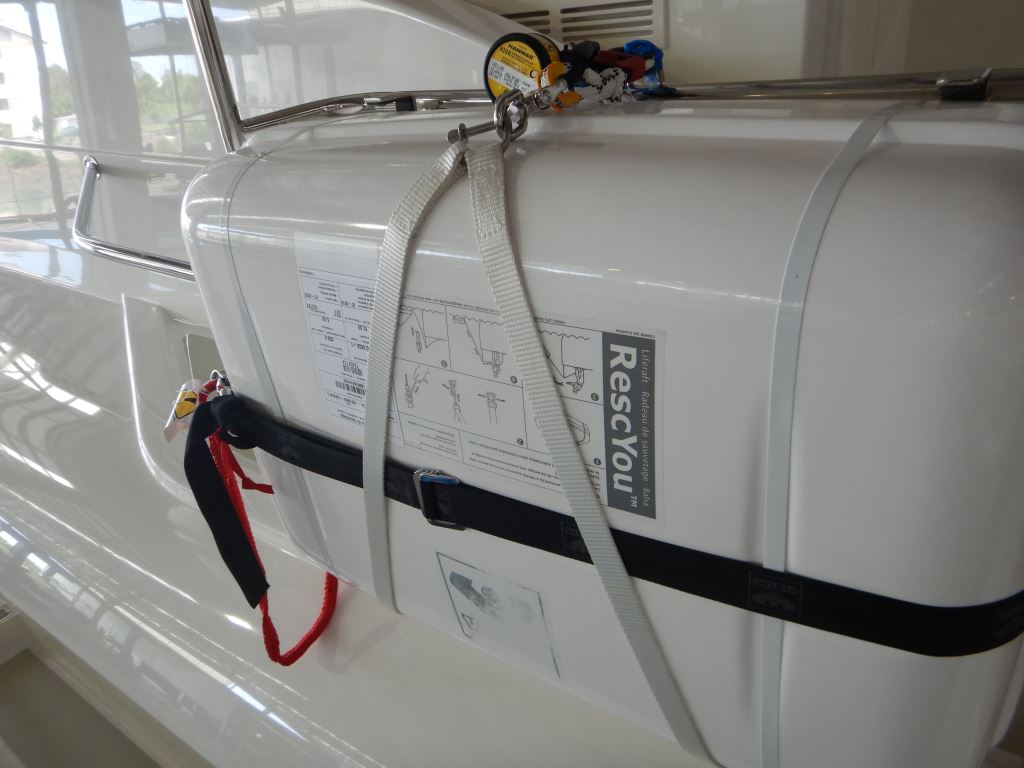
More importantly, if the vessel sank before the raft could be deployed manually, the hydrostatic release mechanism would have triggered, but the raft would have gone to the bottom with the sinking vessel, as the manual lashing would have kept it firmly retained within the cradle. I sent phots of this set up to the raft manufacturer and they initially said it was correct, that the manual strap had a weak link that would break. I looked at the strap closely and could find no weak link. I sent more photos and pressed the issue; it ultimately took four exchanges for the raft manufacturer to finally understand the issue and identify the problem, that two sets of straps had inadvertently been used.
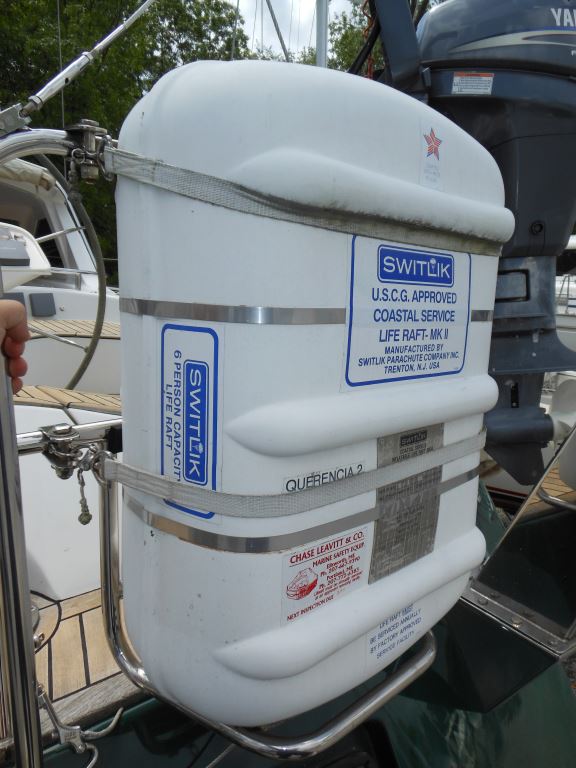
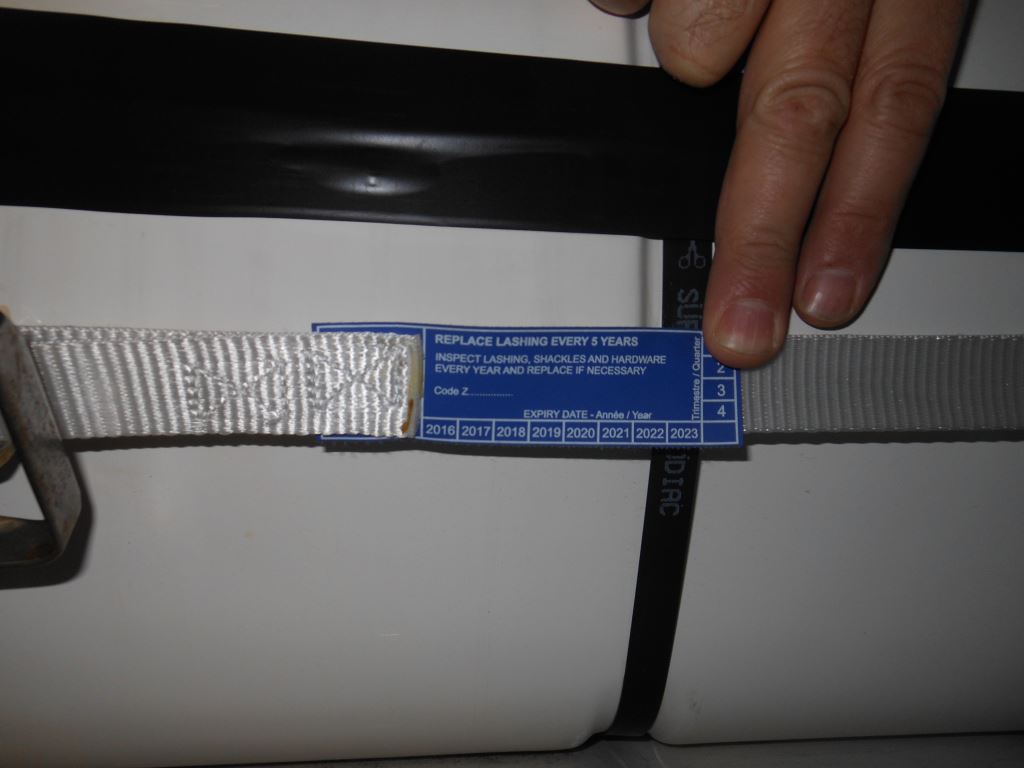
The moral of this story is this, read the instructions for your raft and its release mechanism, and then inspect the installation, and make certain you fully understand how it functions. If something doesn’t look right, query the raft and/or release manufacturer (I prefer going directly to the manufacturer with questions of this sort, as the dealer may have been the one who made the error, and may not understand the problem, or they may be unwilling to admit fault) until you get a clear, logical and unambiguous answer.
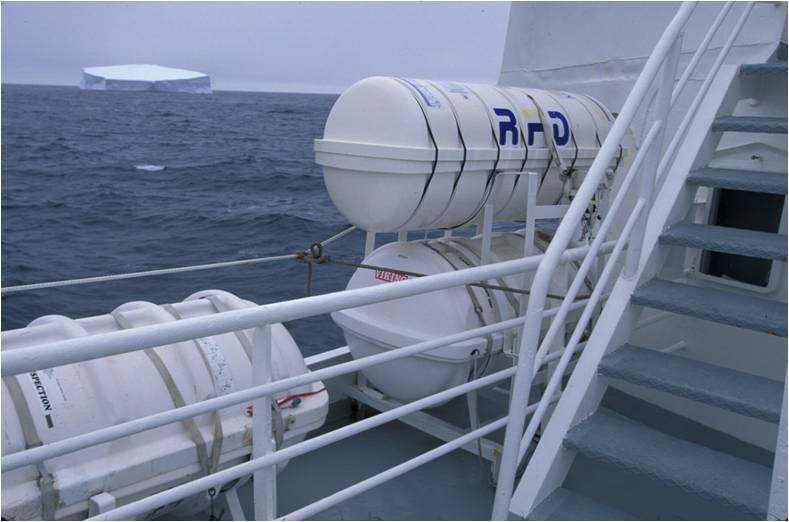
Liferaft installations are anything but complex, however, as straightforward as they may be, in my experience a disturbing number of them are incorrect. Don’t assume yours is correct just because it was installed by professionals; check it yourself and confirm it meets the manufacturer’s installation requirements, as well as marine industry best practices.