Text and photos by Steve D’Antonio
Copyright © 2016
From the Masthead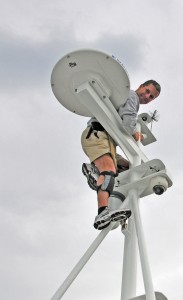
Last month I solicited readers for feedback on their marine industry customer care experiences. I received a flood of correspondence, which included a range of constructive feedback, and no shortage of tales of woe, a few of which I shared in the Ask Steve column. Those notes inspired me to continue the discussion.
Above all others, there’s one subject that dominates my correspondence with clients and readers; that is working with boat yards and marine industry contractors. I routinely receive calls and e mails from those seeking guidance and advice, along with the periodic desperate plea for help. While this is part of the work I undertake as a consultant and advocate for boat owners, it never the less remains a frustration. There are some very good yards and contractors in the US, Canada and abroad, however, they remain the exception, and it pains me to hear the frustration, and at times anger in the voices of boat owners who feel they’ve been wronged or treated poorly by an industry I’ve worked in for my entire professional career. I take it personally and feel indirectly responsible.
The good news is, in most cases these otherwise unhappy scenarios are entirely avoidable, provided boat owners do their due diligence, before making a decision as to whom they will entrust their vessel. Boat ownership should be enjoyable, and while few boat owners would consider being in a boat yard, or working with a marine industry contractor fun, it should at the very least be satisfying, you should be treated fairly and receive good value in exchange for the money you’ve paid.
This month’s feature, part one of a two part series, wades into the subject of working with the marine industry. I’ve written about this topic on many occasions for a number magazines over the years, however, this is the first time I’ve chosen to afford it comprehensive coverage on my own website. I hope you find it both useful and interesting.
Finally, as promised in my previous editorial, this link will take you to an article about new boat building standards, and how you can apply them when visiting boat shows or working with boat dealers and brokers.
Cracking the Code: Working with Boat Yards and the Marine Industry Part I
As a boat owner, you have the power to insist that boat yards and marine industry contractors do the right thing, and you have the option of going elsewhere if they can’t or won’t live up to your expectations.
The key to success lies in evaluating those you are considering allowing aboard your vessel before making a commitment. Follow these guidelines, and you’ll be able to do so while minimizing stress, hassles and disputes.
You should view your boat yard of choice as an ally with whom you work to ensure your vessel’s seaworthiness, reliability and safety.
Boat yards run the gamut, from large facilities found in urban areas to small, intimate custom shops located in rural locales. Regardless of the type, it’s up to the boat owner to carefully scrutinize the capabilities of a yard before entrusting his or her vessel to one of them.
I’ve worked in the marine industry for nearly three decades, as a mechanic, electrician, boat yard manager and now a consultant for boat buyers and owners, and boat yards. Being exposed to the inner workings of this somewhat enigmatic business I’ve learned a few lessons. Chief among these is that when it comes to maintenance, repair and other boat yard type work vessel owners should leave as little to chance as possible. It’s no exaggeration to say that a week doesn’t go by that I’m not made aware of, or called upon to directly assist a boat owner who has run afoul of a boat yard or marine industry contractor. While I do everything in my power to assist these folks, it’s both clear to me and a source of frustration that in virtually every case the difficulties they face could have been avoided, had they done their due diligence by evaluating those to whom they’ve entrusted the work. To be fair, there’s no formal training for boat ownership, and thus I’m nearly always sympathetic to those who find themselves embroiled in such challenges or disputes; boat ownership should be enjoyable, and while spending time in a boat yard, or contracting with industry professionals for work, may not be fun per se, it should be satisfying. I know things have gone wrong when I hear boat owners say, “How could I have known they’d do that?”, or “What should I have done differently?” and sadly these are refrains I hear all too often.
Because the cost of boat ownership isn’t likely to go down and because a properly built and maintained vessel is one that’s likely to bring you back to the dock at the end of the day, it pays to become and remain as involved as possible in refit , service and repair projects.
As a boat owner and boat yard customer, you have a right and a responsibility to insist that boat yards do the right thing, that they live up to your (reasonable) expectations. You are the consumer, and just as consumers have used their buying power, and their walking power, to transform other industries, you can use yours to transform the boat building and marine repair industries. While still far from perfect, many would argue that the US auto industry was transformed as a result of foreign competition, and consumers walking away from manufacturers that failed to deliver on their expectations, into the arms of those who did.
My objective in sharing what follows is to assist the reader in becoming an educated consumer, one who will be knowledgeable enough to require that boat yards and marine industry contractors meet the high standards you deserve (here after I’ll use the term “boat yards” to describe all marine industry service providers, from custom boat builders and traditional boat yards to specialties like electronics, riggers and canvas shops). I will provide you with the tools you need to begin evaluating a boat yard from the very first moment of contact. For example, is the facility neat, clean and squared away, are the buildings well-maintained or are there piles of trash and disused equipment lying around, are windows broken and is the paint peeling, both literally and figuratively?
Make certain the yard you select is competent in the fields required for your projects, few yards are good at everything, most specialize.
While it’s not a definitive arbiter of a yard’s capabilities, neatness does count. If the yard looks shabby then it’s less likely that attention to detail is preached routinely and is a high priority.
Is the staff attentive, do they look you in the eye and greet you as you walk by, is their appearance professional?
Is the equipment, the travel lift, fork lift, vehicles, well maintained or are they streaked with rust and frayed?
The condition of the yard’s equipment can speak volumes. It’s always a good sign when essential gear is well maintained. Rust and deterioration, on the other hand means the will or funds aren’t present, neither of which are desirable.
Does the facility seem over-staffed? One of my greatest pet peeves, and I have many where boat yards are concerned, is the sight of two or more people carrying out a task that requires but one individual. This practice speaks volumes about the management structure, attention to cost effectiveness and efficiency of the organization as a whole.
- Written correspondence is a must; all questions, requests, quotes and responses must be made or followed up in writing.
- Membership in professional organizations such as ABYC (American Boat and Yacht Council), and NMEA (National Marine Electronics Association) are veritable prerequisites.
- Certifications that require those who hold them to pass rigorous written exams, such as those offered by ABYC and NMMA, are good indicators of proficiency.
There is, however, more to evaluating a yard’s or contractor’s capabilities than assessing outright appearance, of course. The next step involves evaluating the quality of the workmanship and business practices of the organization, including knowing how to get a clear understanding of the work that will be performed and what to expect in the way of progress reports, as well as, of course, the cost involved and billing practices. Until, as a consumer, you have a clear understanding of what you can, and should expect from a boat yard you are considering entrusting with your baby, and until you have clearly conveyed your expectations, you can’t expect more from your boat yard experience. If the yard is unable or unwilling to deliver on your expectations, then you must be prepared to go elsewhere.
The Nuts and Bolts of Technical Proficiency
Because, when it comes to the service and repair of a vessel, few subjects are as important as technical proficiency, industry knowledge and attention to detail and experience, technical proficiency must be at the top of your yard evaluation list.
I’m routinely asked by readers, lecture attendees and clients, “can you recommend a yard/contractor for this work?” or, “how do I know if a yard is any good?” The bottom line is the answers to these and other boat yard proficiency related questions aren’t easily obtained. There are, however, standards by which boat yards and the folks completing marine repair, refit and service work can be judged. The American Boat and Yacht Council provides a clear framework for many, but not all, of the tasks that are carried out in boat building and repair, these are clearly defined in their voluminous “Standards and Technical Information Reports for Small Craft”, a telephone book-like tome that includes everything from guidance on AC and DC electrical systems to propeller shaft installations.
Membership and adherence to rigorous industry standard setting bodies, like the ABYC, say much about a yard’s willingness to complete tasks professionally. Certification, a step beyond such membership, is a further indicator of a commitment to competency.
Additionally, ABYC offers certifications in a variety of disciplines, including composites/fiberglass; diesel and gasoline engines and support systems; marine corrosion; refrigeration and A/C; marine systems and standards accreditation. Rest assured, this is no rubber stamp program, and certifications are only given to those who successfully pass rigorous two hundred-question exams (I’m a certified Master Technician, and helped write the Systems Exam). Those who obtain three or more certifications become Master Technicians. The value of the certification is clear, you can be reasonably certain that the folks who are certified at least know the basics of a particular discipline, and likely much more. When I work with an ABYC certified electrician I’m not wondering if, for instance, he or she knows how to calculate the ampere carrying capacity of a particular gauge of wire, or where in a circuit fuses or circuit breakers should be installed. I also know that when I work with an ABYC certified composite technician there’s no question about his or her ability to properly catalyze resin or apply tabbing.
A New ABYC Certification Standard
In an effort to further enhance the value of these certifications, and to reduce the confusion created by those with certifications but no practical experience, ABYC will, in January 2017, segregate certifications into two categories, the first, “Adviser” is for those in an advisory role, surveyors, service writers, compliance specialists etc, with the second, “Technician”, being for those actually building and working on boats in a hands-on fashion. This approach emulates those used in other technical industries, including the Automotive Service Excellence (ASE) program. In order to be eligible for “Technician” status, the candidate must have a minimum of two verifiable years’ industry experience (a “year” of experience is defined as 500 hours spent performing certification related hands-on tasks), in the filed in which he or she seeks certification. Thus, someone who primarily works on outboard motors or fiberglass repair would be ineligible for “Electrical Technician”, or “Corrosion Technician” certification. Additionally, those seeking recertification, which is mandated every five years, will also be required to obtain continuing education credits.
The professionalism of the staff is often clear to see when observing the manner in which they carry out their work. Is their work area neat and clean, are their personal tools well taken care of and are they using the proper safety gear such as eye protection and respirators?
While it’s no guarantee of competence, you get the point, it’s a valuable baseline and the more certified folks a yard has on staff, the more confident you can be in their skill set and commitment to their own professional development. Having made the case for ABYC certification and its undeniable value, the absence of a certification doesn’t mean these folks are unqualified; on the contrary, there are many savvy industry professionals who haven’t gone through the trouble of obtaining an ABYC certification, although I would argue strenuously that they should obtain this valuable credential. As a bare minimum, anyone to whom you entrust technical work should be a member of ABYC and therefore have access to the Standards and agree to follow them whenever and wherever applicable.
There are other standards by which you can measure a yard’s competency. For those carrying out marine electronics work for instance, membership in, and certification by the National Marine Electronics Association or NMEA means they have access to yet another standard, this organization’s own 230 page “Installation Standards for Marine Electronic Equipment”. If you enjoy serious technical prose, as I do, this manual is well written; I keep a copy on my tablet for airport and in flight reading.
Where electronics work is concerned, those carrying it out should carry both ABYC and NMEA membership, as well as agreeing to ensure all installations and repairs are compliant with these standards.
Not only does this organization and its accompanying guideline spell out, chapter and verse, an impressive variety of requirements for ensuring reliable marine electronics as well as electrical installations, it too offers a Certified Marine Electronics Technician credential. Once again, while a certification is no guarantee of competence, it’s certainly a good indicator of the individual’s commitment to excellence and professionalism. And, once again, those designing and installing electronic packages should, at the very least, belong to this organization and they should be willing to carry out installations that comply with NMEA’s standards. Ask these questions pointedly and preferably in writing “Will your installations comply with all applicable ABYC/NMEA guidelines and if not will you let me know, in advance where and why this may be the case?”
Training certificates and certifications in specific disciplines show a yard’s willingness to live up to third party guidelines. ABYC and NMEA certifications are obtained only after the successful completion of rigorous, written examinations, making them especially valuable.
Professionals take pride in their work and in their tools. A custom built tool box, with tools that are clean, sharp, complete and functional, says much about its owner.
The final standard you can and should expect a yard to uphold is the most self evident and yet it’s the most often violated; a clear agreement to follow all equipment manufacturer-supplied instructions. In the vessel inspections I carry out I routinely cite this violation above all others. Today, even for older gear where the printed manual may not be available, virtually every installation and operation manual is available on line, making failures to follow these instructions inexcusable.
When I point out such “installation instructions violations” to boat builders, yards and contractors they often respond by saying ‘that’s the way we’ve always done it and it’s never been a problem’. While that may be true, I, and you should as well, point out that this approach means they, rather than the equipment manufacturer, are accepting responsibility for any failure related to the manner in which they’ve installed the equipment, in perpetuity, because the manufacturer’s warranty will likely be void. Ultimately, while it may seem superfluous, you should insist that all manufacturer installation instructions and recommendations be followed to the letter.
Next month I’ll cover cost control, time and material vs. quoted work, maintaining a good working relationship with those carrying out work, and avoiding conflicts of interest.