Steve D’Antonio
Copyright 2015 SDMC, Inc.
From the Editor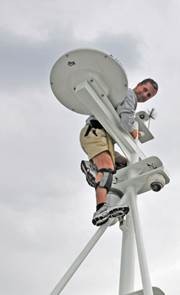
When you last heard from me I was still in China. I’m preparing this month’s feature column while returning from the Miami International Boat Show. A week prior to this show I completed a month-long travel odyssey, which began inVirginia and took me to New Zealand, Australia, China and Turkey. When I returned to the Richmond, Virginia airport, 30 days after leaving, I “crossed my outbound track” as sailors say, completing a circumnavigation by air. Turkey was an eye-opening experience, I found the people warm and inviting, the food and especially the bread particularly tasty after a week in China, and the historical landscape, as well as the geography, stunning. Turkey boasts over 10,000 registered sites of antiquity; the Roman ruins rival those in Italy. While there I visited several boat building shops, and undertook sea trials on an unusually calm Mediterranean Sea. In the coming weeks Katie will post photos from all of these locations to the gallery section of the SDMC website.
Depending on your point of view, boat shows are either a much anticipated event or a necessary evil (undeniably the former for me, I love each and every one I attend). On the day before the show began I shared an elevator with a marine industry professional from a well-known, large firm. We exchanged a few boat show pleasantries after which he said, “I hate rich people”. I’ve encountered this attitude on too many occasions. Before he made this fateful statement I recognized the ‘industry thousand yard stare’, one that cries out, ‘In spite of the fact that I spend all day on boats in idyllic locations I still hate my job”, and the show hadn’t even started. That encounter reminded me of another I had while on a pre-purchase inspection sea trial a couple of years ago. The professional captain, hired by the broker, to pilot the boat for this purpose, handed me his business card with a smirk, under his name it said, “It’s not my fault you bought a boat”. I handed it back to him and said “I won’t need this, and the boat business doesn’t need people like you”. Folks like these are also fond of using the worn out tag lines, ‘The happiest days of a boat owner’s life are…’, ‘A boat is a hole in the water into which…’ and ‘Boat stands for break out another…’. Because I detest them so much, and because I have no wish to perpetuate them, I’ve intentionally left these axioms incomplete. When I hear my professional peers use these phrases, I take them to task, pointing out that if their boat owner customers laugh at them it’s only because they are being polite. As a boat owner, when you encounter this unprofessional attitude, I encourage you to make it clear, sometimes that can be accomplished with nothing more than silence, it’s unappreciated. If you are a professional, I appeal to you to assist me in eradicating this mindset, if for no other reason than it’s bad for (your) business.
The show itself was busy, with a variety of new and interesting products, some of which I recently wrote about on the SDMC Facebook page. These include Fleming’s new 58 model (hull #4 was on display, I took hull #3 from the UK to Germany last May and subsequently wrote a review of the vessel, which will be printed in PassageMaker, my final submission to this publication, next month). Burr Yacht Sales’, the Fleming East Coast dealer, display was a hive of activity, the boat has garnered strong interest, and with good reason. I also spoke with Jeff Druek, proprietor of Outer Reef Yachts. Jeff shared with me photos of Outer Reef’s first, soon to be completed, all vinyl ester resin infused fast cruiser, the Trident series, which is being built in 55, 65, 75 and 98 models. Their first T-550 will be launched at the Cannes boat show this September. They will also premier in the US at the fall 2015 Fort Lauderdale Boat Show. These are being built at Outer Reef’s yard in Croatia.
There was no shortage of hybrid vessels and systems at the show, and on that subject, as many readers know, I’m a skeptic of these systems. In brief, they are extremely complex, and most manufacturers are only able to offer limited dealer support. The 600 pound gorilla in the room is, of course, a minuscule, if any, enhancement in efficiency. When I debated this editorially with my colleague Nigel Calder last year, he admitted that for trawlers (his testing has been on his own sailing vessel) the added “gain” is realized in enhanced support for house loads via a much larger battery bank. That logic was lost on me then and remains so now, as we already have proven large battery banks and high output charging systems, which don’t impinge, for the most part on the reliability of the apex system, propulsion. When I bring this up with hybrid propulsion manufacturers, as I did during the Miami show, they point to small gains under very narrow operating circumstances. Even then, the gains are in the low single digit percentage points, to which I can’t help think, ‘is it worth it?’ When I brought up the issue of support with a sincere and knowledgeable hybrid manufacturer, one who espoused the virtue of his redundant Airbus-inspired system, he responded by saying most troubleshooting, and even some repairs could occur via the internet. Let that sink in for a moment, via the internet…using a Wi-Fi, cellular or satellite modem.
When boat owners ask me how they should prepare for extended or offshore passages, aboard vessels that use already complex yet conventional propulsion and other systems, I advise them to become as knowledgeable and self-sufficient about their vessel and its gear as possible, and assume they will have no outside assistance. Now add to that equation an esoteric, aviation-like in its complexity, hybrid propulsion system and you can understand my reluctance to embrace this technology. I believe it’s no coincidence well-respected production builders of blue water capable vessels, Fleming, Grand Banks, Kadey Krogen, Marlow, Nordhavn, Outer Reef and others have continued to avoid hybrid propulsion, in spite of the fact that many buyers would purchase them if offered. Does this mean there’s no place for marine hybrid propulsion systems? No, there are applications where it can be made to work, while offering enhanced efficiency. However, for the time being, I don’t believe these include offshore passage making vessels. For hybrid propulsion, and for that matter all marine systems and manufacturers, I advise both boat owners and industry professionals to ask sometimes difficult questions regarding support, warranty coverage and of course efficiency vs. cost/complexity before considering this path.
This month’s Marine Systems Excellence column delves into the subject of propeller removal. I hope you find it both interesting and useful.
Proper Propeller Removal
Don’t Let this Happen to You
A number of years ago, as I was strolling through a boat yard, my idea of sightseeing when I travel, I came across a mechanic who was in the process of removing a propeller. He was using a technique which, even writing about it well over a decade later, makes me cringe. He’d removed the propeller’s nuts and in their place had installed what was later aptly referred to as a “bang nut”, an over-sized, closed end brass nut. The bang nut was screwed onto the shaft; however, it was stopped short of making contact with the propeller hub. Once the nut was installed, it was hammered on using a substantial maul.
As each blow connected with the bang nut, the shock wave was transmitted up the propeller shaft, through the coupling, into the transmission’s bearings and gears, on to the engine block, where it was ultimately absorbed by the flexible motor mounts. After a score of mighty swings the mechanic was visibly fatigued and perspiring heavily, yet the propeller remained fast with the shaft. With each swing the propeller reverberated with an ear-splitting twang. After a brief rest he resumed and the propeller ultimately yielded, sliding aft into the nut with a subdued clunk.
This strut bears mute testimony from abuse by blunt force. A hammer was likely used to strike the forward end of the propeller hub, landing glancing blows on the strut in the process.
The physics of this approach are straightforward enough, with each blow, the shaft, transmission and engine were driven forward a fraction of an inch. The mass of the propeller encouraged it to be left behind in that forward advance, eventually forcing it to separate from the shaft taper. The technique worked, but at what price? It’s likely that removing a propeller using blunt force of this or any kind, including striking the forward end of the propeller hub directly, driving the propeller aft, damages or shortens the life of transmission components, gears, bearings etc. Pound for pound, transmissions are among the most costly pieces of gear aboard your boat, and repairing or replacing them is always a pricey and unpleasant experience. In short, this technique and others like it should never be employed for propeller removal.
It’s Tempting But…
Some have proffered that the way to make it easier to separate a prop from its shaft is to take removal into account during assembly. Toward that end, using anti-seize, grease or another release agent on the shaft taper is often advocated. Make no mistake about it; under no circumstances, once again, should this practice be used. Virtually every propeller manufacturer’s installation guidelines make it clear that props should be installed “dry”. The one exception to this rule is an extremely thin application of lightweight machine oil, onto the shaft taper, is acceptable in that it will help prevent binding.
This propeller was installed with grease, remnants of which can be seen at the propeller to shaft interface. The propeller was ruined in short order because it shifted on the taper each time the transmission was engaged. Grease is viscous and incompressible, traits which virtually ensure that the propeller will fail to fully engage the shaft.
The primary goal is to make certain a propeller, once installed, stays put. Using anything (grease and other viscous materials are incompressible, making a hydrolock scenario very likely) between a propeller’s bore and the shaft taper only increases the likelihood of movement between the two, which in turn can lead to sheared keys or worse, a lost propeller. If removal is challenging, that’s a good sign, machine tapers like those used on shafts are truly amazing in their ability to reliably unify disparate parts, a desirable trait where propellers are concerned (I’ll cover propeller installation next month).
Removal Options
As desirable as it is to ensure a solid fit between a propeller and shaft, there will come a time when the two must be separated. Fortunately, there are a variety of means of easily doing this, without damaging the propeller, shaft or transmission.
Hydraulic propeller removal tools are versatile and will work with most propellers. They are, however, costly.
For boat yards, the Cadillac of propeller removal tools relies on the power of hydraulics. Combination tool kits are available to remove propellers, shaft couplings and strut-mounted cutless bearings. These tools enable yards to quickly and easily disassemble these components using a hand operated hydraulic pump, which actuates a ram, which in turn applies thousands of pounds of continuous rather than shock force to an assembly. If you are in need of propeller service or shaft coupling removal, it’s well worth finding a yard that relies on a tool of this sort.
The “Dura-Mate” hydraulic prop puller kit manufactured by Durant Machine Company of Mystic, Connecticut. This tool can also be used to remove propeller shaft couplings and shaft bearings.
It’s worth repeating, under no circumstances should it ever be necessary to use shock force to disassemble any of the aforementioned components, propellers, couplings and cutless bearings. As you might imagine, the convenience of this tool comes at a price. A combination hydraulic prop, coupling, and cutless bearing removal tool costs several thousand dollars, and it’s large and heavy, in most cases it’s housed in a rolling dolly that’s about the size of a baby carriage.
Alternatively, mechanical, scissors-like prop removal tools are also available. These are comparatively compact and lightweight, and much less expensive. While useful, these tools do have limitations. Primarily, they are incapable of imparting as much force a hydraulic tool, and they must be able to “reach” between two adjacent propeller blades, a requirement that may not be possible with some four and most five blade propellers.
A scissors style propeller removal tool. These work for smaller, and three blade props. Four blade props often don’t offer enough clearance between blades.
Yet another option relies on a custom made yet exceedingly simple pulling mandrel. This arrangement consists of three high strength threaded rods and a plate that uses the propeller shaft end as its fulcrum. The rods are screwed into matching threaded holes that have been bored and tapped in the aft end of the propeller hub. Some propellers come from their manufacturer with these holes (If you are ordering a new prop or new boat, request them); some include just two holes which I would argue is inadequate for this process, some have no holes. In any event, the holes can be easily added by most propeller shops; however, this cannot be done while the propeller is installed on the shaft.
In order to use some propeller pullers, the propeller’s hub must be drilled and tapped, with two and sometimes three holes. To keep them free of debris, these holes should be filled with stainless steel or plastic Allen head screws.
With careful measurement and a simple drawing, most machine shops could make a custom tool for you at relatively low cost (I would argue that these should be provided as an option or standard by every boat builder, for their propeller arrangement). The plate need not be made from exotic alloys, ordinary mild steel is more than adequate provided it’s painted and lightly oiled. The threaded rods should be high strength; they can be easily purchased off the shelf.
The PropSmith is a compact, low impact means of effectively removing as well as installing (no other puller can make that claim) propellers, it is virtually fool-proof. No inboard vessel should be without one.
The PropSmith, when stored in its plastic box, takes up roughly the same area as two hardback books.
The final approach, and one I favor, relies on a method that bears some resemblance to the pulling mandrel, however, it uses a purpose made tool known as a PropSmith. The PropSmith also requires a trio of threaded holes in the prop’s hub, however, its fulcrum plate engages the shaft’s threads, holding it rock steady and making it especially useful for in water use by a diver. Because of this threaded shaft engagement, an added benefit of the PropSmith is its ability to aid in installation of a propeller, pushing it firmly onto the taper.
A custom-made screw type puller. These are simple and relatively easy to make, most machine shops could fabricate one for a few hundred dollars from readily available materials.
It’s not unreasonable to suggest that every vessel carry its own means of propeller removal, even if you never intend to undertake this task yourself. Why is this necessary? If you find yourself in a boat yard for planned or unexpected propeller work, and you see a mechanic making his or her way toward your boat carrying a large hammer and a bang nut, you can intercede with your own tool; you know it will work well, it will work quickly and you can be confident that it won’t cause any damage in the process.