Text and photos © 2020 Steve D’Antonio Marine Consulting, Inc.
From the Masthead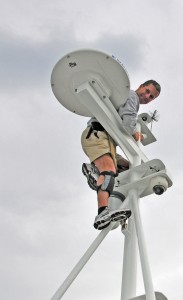
Ever the optimist, I believe if Covid 19 isn’t yet in our wake, it’s at least abeam of us, and while it’s not always easy to remain optimistic, as we are being bombarded with mass media’s regular stream of negative headlines for the “second wave”, and predictions for “doubling of deaths”, or the usefulness or uselessness of masks for those who dare to return to some semblance of normality, I never the less see many signs for optimism.
I’m not downplaying the severity or tragedy of tens of thousands who have died in the US alone, I’m simply suggesting that you not let the bad news get to you; it’s worth remembering the old news axiom, ‘if it bleeds it leads’, and that has been in full force throughout this event (I don’t like the word “crisis’ it implies resignation and failure). Good news about the virus makes headlines all to infrequently. I said this a month ago and I’ll reiterate, I remain firmly convinced that this nation, and those who fight alongside us, shall vanquish this unseen biological foe. In your discussions with your family, children, friends and colleagues, I implore you to remain positive, and optimistic; doom-saying and fear-mongering serve no purpose but to sap the energy and drain the fight from those around you, and energy is precisely what we will need in the days and weeks to come. K.B.O.
On Monday May 4th SDMC conducted its first in a series of online video webinars, this one entitled, “Identifying the Most Common New and Used Vessel Construction and Systems Flaws”, you can read more about it, as well as upcoming lecture titles, here. I’d like to thank all of those who attended and posed a slew of excellent questions. Our goal is to schedule another one of these in roughly a month, stay tuned.
Photo Essay: Ring Terminals
Solderless or “crimp” terminals play a critical role in any vessel that’s equipped with an electrical system, AC and/or DC. A modern 40 to 50-foot cruising, commercial or military vessel may have upwards of a thousand of these, several hundred at panels alone.
The terminals themselves encompass a ranger of styles, from spade to ring, fork to bullet, with each ideally used in a specific application. Beyond that, the engineering and materials from which these are made also varies considerably, ranging from automotive and “economy” to milspec, along with PVC, Nylon and heat-shrink insulation, single and compound crimp, tinned and untinned, braze, annealed, seamless, the list goes on.
One of the more common errors I encounter where solderless terminals are concerned involves ‘field modification’ of the ring style, where the far end of the ring is cut away to allow it to engage a screw. In the example shown here, when I removed the outlet, the modified ring separated from the screw of its own accord; clearly that’s not a good sign. It’s also clear to see the ring has been cut to transform it into a bastardized version of a forked terminal, also not a good sign. When I brought this to the attention of the builder, I was told this was necessary because the screw was captive. While the screws on many outlets are captive, that is done simply to prevent them from being lost, they can in fact be removed, the “captive” nature is simply slight thread deformation, making it possible to remove the screw and install a proper ring terminal. Better yet, one could use a captive fork, one whose ends are turned up at 90° (conventional fork terminals are prohibited where ABYC compliance is the goal), or a fork whose ends are pincer-shaped, requiring some tension to push them beyond the screw. Ultimately, only ABYC- compliant, and ideally milspec solderless terminals should be used for all shipboard applications; and under no circumstances should a solderless terminal be modified. For more on solderless terminal selection and installation, see this article.
Ask Steve
Hello,
I recently read (reread) your excellent ProBoat.com article “Beware the Brass” from July, 2012. Thanks for writing it.
My 2001 Mainship 430 trawler has Southeastern Foundries bronze dripless shaft logs installed. They have performed very well and I only recently had the Parker/Clipper lip seals replaced because they were over 15 years in use.
After rereading your article I’ve decided I definitely should have the threaded pipe-to-hose water injection hose adapters replaced as well and soon. I phoned Southeastern Foundries and spoke with Mr. Steve Drummond. He told me that his company did not supply hose adapters to Mainship and he would expect that Mainship used common brass fittings for the water injection ports.
The hoses are 1/2 inside diameter and from my caliper measurements it appears that the pipe threads are 3/8 nominal. Groco and others sell 1/2 by 1/2 bronze pipe-to-hose adapters but I’ve searched the internet and cannot find anyone making or selling anything in bronze with a pipe thread smaller than 1/2 inch.
Do you know of any source or have any suggestions? If I have to I would be willing to purchase some bronze bar stock in the suitable alloy and have a local machine shop make the fittings.
I just hope the old brass fittings will unscrew from my shaft logs without falling apart.
Thanks,
Jim Fidler
Jim:
I’ve faced this challenge on many occasions. True bronze plumbing is virtually unobtainable in sizes under ½” NPT. It’s a conundrum to be sure. My understanding is the machinability of these components in bronze, in these smaller sizes, is very poor. The addition of zinc, making them effectively brass, improves this feature.
In the past, I’ve had these fittings machined from bronze stock, which is readily available, or I have modified leaded red brass (zinc content no more than 15%) pipe nipples to include hose barbs. The danger in the latter is it’s very difficult to definitively determine the zinc content of most off the shelf plumbing components, regardless of how they may be marked. Purchasing stock from a reputable supplier, on the other hand, is less risky.
Steve,
I enjoyed the recent article about electric shock hazards. One point on the photo of the GFCI outlet. I am an architect and am on construction sites frequently. I am seeing most projects install all outlets, regular and GFCI with the grounding lug at the top. The reason is that if the weight of a cord starts to pull the plug out it is only the ground that is exposed to touch, not the hot lugs. A small detail, but intended to prevent a shock.
Richard C. Brown
Richard:
Thanks for sharing these thoughts. When I was in college, 35 years ago, I worked as an electrician’s helper. While doing so I learned to install receptacles with the ground pin at the top as well, the logic being that if something narrow and metal fell against the plug, a coat hanger for instance, the ground pin would prevent it from making contact with either of the two blades, particularly the hot. As a result I’ve installed receptacles in that fashion. I wrote a brief column about this detail on my Facebook page a few months ago. I’ve never thought about whether it helps with exposure of the hot blade when the cord was stressed, but I suppose it would do that as well.
Hi Steve,
Just read your article on fire extinguishers and thought I’d relate something that happened on my last survey.
The surveyor, a well-respected surveyor I’ve used and appreciated for the last 20+ years, opined that I had too many extinguishers and recommended that I discard some of them! I have eight, plus a built in 90# CO2 in the engine room, of my 46′ Bertram sportfish. His reasoning was that taking the time to grab an extinguisher and discover that it was not functional wasted precious moments that could be otherwise spent extinguishing the fire.
I countered that I checked each extinguisher each year and physically inspected it for operability and damage, inverted it for those containing powder and listened to hear the powder move, and noted the proper gauge reading. He countered by saying that at a seminar he had attended the speaker tossed a hand full of gauges removed from old extinguishers on the table. All of them read in the green zone.
I gave that some thought then came up with a plan that I have used now for a few years. On a warm sunny day I take each extinguisher with a gauge and lay it in the cockpit in the hot sun, carefully noting the exact reading on the gauge. An hour later I recheck the reading on each gauge to verify that it has noticeably moved up in pressure. This is based on the Combined Gas Law: PV/T=PV/T. This confirms that the gauge isn’t frozen and is indeed operable. I note the date and “gauge checked OK” on the back of the extinguisher using a black marker pen.
I do still buy a new extinguisher every year or two to replace one of the older units on the boat and retire the old one to my home. However, this procedure helps me to assure that every gauge, even the newest ones, are indeed operable.
Tom Collins
Tom:
The surveyors logic is flawed at best, as the extra ten steps you take to get to the fewer extinguishers is time that could also be spent fighting the fire with an extinguisher that was closer at hand. Why does having fewer extinguishers make it more likely the ones you have will work? It’s also based on hearsay, were the frozen gauges from cheap, 29 year old $19.99 fire extinguishers, where’s the report that was written to document this, etc. Assuming extinguishers are good quality and regularly inspected, I’ve never heard of any reputable fire safety organization advocating for fewer extinguishers, it truly beggars belief that any marine industry professional would advocate for this position.
In the articles I’ve written about fire extinguishers I strongly advocate for the metal nozzle variety. These are far less leak prone, generally higher quality, and refillable, whereas the plastic nozzle versions are not, they tend to last a year or two, after which they must be discarded. More on portable fire extinguishers here.
I do like your test procedure.
Hi Steve,
Your June 2017 article on Alternator Charge Regulation was just excellent. I’ve been running an externally regulated stock alternator, and even if I throttle-down the maximum charging rate by adjusting the Balmar regulator down to 70%, the alternators still don’t last.
My existing stock alternator is rated at 130 amps, so in regular use it is putting out about 75 amps. And it has to put out that all day while we are cruising, to keep up with the house demand. The main house bank is an 800 amp bank, and actually I am happy with the charging rate from the existing alternator. I know that does not follow your 25% rule, but for our style of cruising it works just fine. However, I do want to change the alternator, and put a “high capacity, continuous duty” alternator, something which will have a longer life. And I want to do that without having to make modifications to the mounting. The current alternator is on a Detroit 8- v92, and it is driven by double 3/8 belts; the alternator has a double mounting foot.
Here’s the question: I’ve spent a good deal of time looking at alternators, both on the Balmar and Leece Neville sites, and it seems impossible to tell which of their alternators (or that of any other brand) are truly “high capacity, continuous duty” alternators.
The Balmar site Series 9 Large Frame lists those alternators as “Mid Duty.” The XL Frame lists those as “Heavy Duty Cycle”.
The Leece- Neville site lists their alternators as “Heavy Duty.” It is all very confusing, and in a way deceptive.
So Steve – what specific brands & models of alternators do you feel fit the definition of high capacity & continuous duty?
Thanks for your excellent work, and superb articles and advice.
Greg Allard
Greg:
Broadly speaking, the larger an alternator’s case is, the more likely it is to be capable of continuous high output. Heat dissipation is the issue, these big units are better able to dissipate heat when working hard.
Having said that, for retrofits there are often size and mounting foot limitations, which must be taken into account. This becomes your starting point. Given enough space, larger cases are preferred. For Leece Neville/Prestolite alternators, which are reasonably priced, and with which I’ve had very good success, you might peruse this site. You’ll see the headings for each category, which include “Fire Truck and Emergency Vehicles”. These alternators are typically designed for extreme working conditions of high, continuous output, high ambient temperature and the need for high reliability.
Balmar (now owned by CDI Electronics) of course is well-known for their broad selection of high output alternators as well as their easy to use website. Again, the size and mounting options will likely drive your decision. Where possible select the larger case size. Balmar’s website is user-friendly and geared toward boat owners in making a selection.
Based on your description, I would classify your application as mid-duty, making the Balmar 9 series suitable. The XL series (some of these, such as this one, are rebranded Leece Nevilles), while formidable, is probably over-kill for your goals.