From the Masthead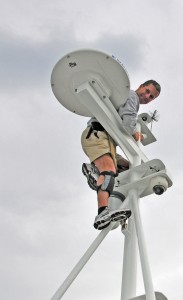
Cruising Freedom
It’s a near universal truth, boat owners use their boats, or cruise, because, among other things, it offers a sense of freedom and independence from the rules, requirements and bustle of life ashore. It’s not for everyone, losing a cell signal for instance, for some, can be a traumatic experience, and I’ll confess, being out of touch, especially for a small business owner, can be unsettling. The rewards, however, are many and varied.
My first “cruise” was aboard a sail training vessel, the R/V Westward, a 120-foot steel schooner. The first leg of this 6-week journey took Westward, her crew and complement of students from Woods Hole, Massachusetts to Grenada, over the course of 18 days. Departing in mid-October, into the cold, gray, wind-swept North Atlantic was a trial by fire for many, most of the students were sea sick, including me, however, once we rounded Bermuda, the skies brightened, the sea calmed and went from slate to azure; most of us quickly found our sea legs. Still, it was no pleasure cruise, one could shower as often as one liked, but the water was cold and salt, and students stood scientific, navigation and vessel watches (which rotated from deck, to engine room, to galley; it was Westward’s engineer who first referred to me as a “gearhead”), while carrying a full academic work load.
GPS hadn’t yet been invented and eventually, as we ventured further and further from shore, LORAN became useless, making sextant, compass, and chronometer the only means of accurate navigation; mastering the taking of sights and reducing them to a position, was mandatory for every student aboard. For me, it generated a lifelong love of, and fascination with, the sextant and celestial navigation (I cherish my WWII-vintage, David White Mk II).
Recently, while approaching the entrance to a dock, I encountered this placard; it took me aback, had I inadvertently entered a customs dock, law enforcement, state, or federal marine facility? No, this is a common marina in a southern port city. In effect, it means landing one’s vessel here, or for individuals entering from shoreward, is tacit forfeiture of our 4th Amendment rights? It’s eerily similar to the signage one encounters when entering a military base, where one might expect such a level of security, but here? It left me feeling uneasy, and thinking of the, ‘frog in the slowly boiling water’ adage.
This month’s Marine Systems Excellence e-Magazine feature is the final segment in a two-part series on troubleshooting engines that refuse to start, I hope you find it both useful and interesting.
No- Start Continued
Air leaking into the fuel system upstream of the primary filter, will accumulate here, and eventually make its way to the engine’s high pressure pump, which in turn will lead to a shut down.
Last month I reviewed some of the reasons an engine or genset might not start. I confined that discussion mainly to electrical gremlins, wherein the engine will not crank. In this month’s column I’ll delve into reasons an engine might crank but not actually start.
When an inboard diesel engine cranks, several things are occurring simultaneously. Air is being drawn into the cylinder or combustion chamber via the air intake manifold/filter, and passing through intake valves as the piston is drawn down the cylinder, creating a vacuum. As the piston returns, traveling upward, the intake valve (or valves, some have two) closes, pressurizing the air. On a common gasoline engine, the compression ratio is roughly 10:1, and the compressed air is mixed with fuel vapor. On a diesel engine the compression ratio is much higher, roughly 20:1, and the fuel is not mixed with the air until after compression has occurred, an important distinction.
Incorrect valve clearance is an often over-looked culprit in hard or no start scenarios.
While a higher compression increases the thermal efficiency of an engine, in the case of a diesel engine it’s mandatory. As the air is compressed, its temperature increases, and in the case of a diesel, it’s hot enough to ignite the fuel when it’s injected into the combustion chamber by the injection pump and injector.
Injection pumps can fail, however, this is relatively rare. Dirt and water, on the other hand, can quickly bring even the most robust injection pump to its knees.
If a diesel engine’s compression is insufficient, the air will not be hot enough to ignite the fuel. It is for this reason that a conventional diesel engine smokes on startup, the combustion chamber is still relatively cold, inhibiting complete combustion, that white smoke is actually minute droplets of unburned fuel. Therefore, low compression can be a reason for hard or no starting, and this can be caused by worn piston rings, sticking or improperly adjusted valves or a starter that turns too slowly; between 150 and 250 rpm are required for a diesel engine to start. Malfunctioning glow plugs, either the plugs themselves or the solenoid that controls them, can also make for hard or no starting, especially on cooler days.
Damaged or carbon-clogged rings can cause an engine, especially when cold, to fail to generate enough compression to initiate combustion.
Glow plugs and inlet air heaters are used on some engines to warm the air, or the combustion chamber, to ease starting, which also reduces smoke. Some air intake heaters continue to operate, in a post-heat stage, for a few minutes after the engine has started, to reduce the production of smoke. A malfunctioning pre-heat system, which could include the glow plugs or air heaters themselves, or the control mechanism, solenoid, switch, or wiring, can make an engine difficult or impossible to start, especially on a cold day. This system is relatively easy to check using a multimeter, start battery voltage, 12 or 24 volts, should be present at each glow plug, or the studs for the air heater, when in the pre-heat phase. If voltage is present, but these components are still suspect, their resistance can also be checked, an open circuit indicates a failed glow plug or air heater. More on multimeter use here.
Fuel lift pumps are simple and robust, however, they do wear out, and many include integral filters or screens, which can become clogged.
The manual lever on a fuel lift pump is used to prime, and bleed air from, the fuel system.
On the subject of electrical interfaces, many injection pumps rely on an electro-mechanical solenoid of some sort to either open, and allow fuel to flow, or close to stop fuel flow, upon start up or shut down respectively. Some rest in the open or run position, while others rest in the closed or stop position. If your engine requires the solenoid to be energized to allow fuel to flow, i.e., it rests in the closed position, and it is defective or stuck (fuel contaminates or gumming can cause it to stick), or the wiring, or switch (the key switch) controlling it are damaged or the circuit is open, the engine will not start. This too can be checked visually, if the solenoid plunger is external, as well as with a multimeter, to determine of the solenoid is being energized.
Most conventional high pressure injection pumps use some type of electro-mechanical mechanism to allow fuel to flow, or stop flowing, that is used to stop the engine. If it malfunctions, the engine may not start (or it may not stop). The pump seen here uses a solenoid plunger, visible with the rubber bellows, in the upper right, that is engaged to stop fuel flow for shut down purposes.
Even if it is being energized, it can still have failed or it may simply be stuck (external solenoid plungers can be actuated manually, as a test). Removing this solenoid and inspecting, actuating, and energizing it will determine what, if anything, has failed.
Fuel system woes account for the vast majority of engine no start scenarios. There’s a reason those Racor bowls are clear, check them often.
Another aspect of this choregraphed mechanical ballet is the injection of the fuel. For conventional pump-line-nozzle, i.e. non-electronic, injection systems, usually via rubber hose, fuel passes from the tank to a primary, coarser (usually 10-30 microns) filter, often a water separator with a clear bowl, then on to a low pressure or ‘lift’ pump, after which it turns into a steel line, where it then enters the finer (in the 2-7 micron range) secondary fuel filter, and then on to the high pressure injection pump, and finally to the injectors via again steel lines. In this sequence, the most common causes for failure are clogged filters, a defective lift pump or air in the lines.
A properly functioning injector will develop a uniform spray pattern, one that atomizes fuel into a mist, like the one shown here.
Your primary fuel filter should be equipped with a vacuum gauge, without it you are essentially flying blind, you have no way of knowing how hard your lift pump is working to draw fuel through that filter. If you don’t have a vacuum gauge here, I strongly recommend you install one, it’s a valuable troubleshooting tool, and it will alert you as to when that filter should be replaced.
The primary fuel filter vacuum gauge is an invaluable ally in failure to start troubleshooting scenarios.
If, while cranking, you observe the vacuum gauge climbing, there is a restriction somewhere between the lift pump and the filter; naturally the element itself should be checked and changed if there is any doubt. If the vacuum remains low, below roughly 3 inches of mercury, then move on. The vacuum gauge will not alert you to restrictions after the lift pump, including the secondary filter. However, if you change that filter when you change the primary filter, it’s unlikely to be the culprit. On the subject of filters, it’s worth noting, some lift pumps, both electric and mechanical, include their own integral filter or screen, which can become obstructed. More on vacuum gauge use here.
A clogged secondary fuel filter will cause an engine to starve for fuel, and shut down, without necessarily registering anything unusual on the primary filter’s vacuum gauge.
Air can make its way into a high-pressure fuel system from several sources, but most often at primary filter housings, tanks that are low on fuel, and unions in plumbing between the tank and the lift pump. Air will only be drawn in where a vacuum is present, between the tank pick up, and the lift pump, so concentrate on inspecting those areas, at rest, they may leak some fuel. Make sure everything is tight. Then, try bleeding the high-pressure system to purge any air that may be present, I’ll cover that procedure in a later column.
Fouled or otherwise malfunctioning injectors can make an engine difficult to start.
Finally, on older engines it is possible for the injection pump and injectors to wear out, and the latter can become fouled with carbon. If the engine has more than 3,000 or 4,000 hours on it, pump wear reaches a point where fuel pressure may be low enough to prevent combustion. This is often preceded by easy cold starts, where fuel viscosity is higher, and hard hot starts, where fuel viscosity is lower.